Company Name | Contact Info | Location | ||||||||||||
---|---|---|---|---|---|---|---|---|---|---|---|---|---|---|
AKKAYA EPS MAKİNA İMALAT SAN. VE TİC. A.Ş.
Ulaş OSB Mah. 202. Sok. No: 12/1 / Ergene / TEKİRDAĞ / TÜRKİYE
|
Contact Info: +90 282 655 5894
|
Hall: 9
Stand: 901C
|
||||||||||||
Product Groups | ||||||||||||||
|
- Company Info
- Products
- Represented Companies
- Company Brands
Since 1980 AKKAYA engineers and manufactures machinery for processing expandable Polystyrene (EPS) Intensive exchange of experience with all our customers enabled the engineering of cost-efficient, highly productive, easy to maintain and user friendly machines and production lines - which are exported global since 1990 as well. Our export share above %89 is due to the steady further developments of practical production-systems with the newest technology. Akkaya has been producing EPP machinery and equipments since 2010, together with Foamatec.
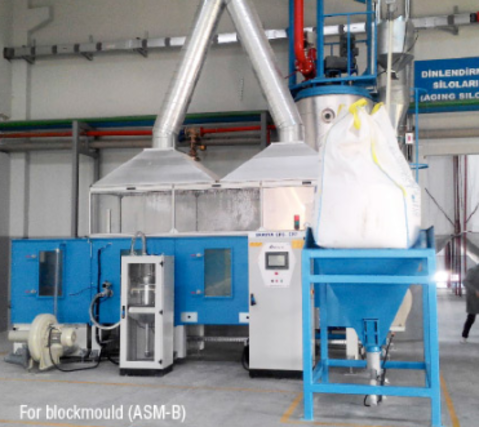
Working pricible of the batch type, to expand a fied mass of raw material in a fied volume which enables to reach easily desired density.Dosing Unit, to weigth the rigth amount of EPS for the adjusted density. Filling to the vessel is done by gravity. Expansion chamber made of AISI 304 stainless steel, cylindrical shape. Agitator and accessories made of AISI 304 stainless steel, speed control via drive. With the adjustable speed in different steaming phases, enables to process different materials. Discharge door located on the floorof the vessel, to empty the chamber fast.Machine has a built-in silo control system, with the rigth hardware you can operate this part. Pre-expanded beads from the pre-expander conveyed to the storage silos for 1st and 2 nd expansion stages by starwheel rotary.
Blockmould is designed in vertical shape, with only one side openning which ensures the steam and vacuum tigthness 100% during the process. This is also needed for the pressure sertification and during operation machine needs less service. Described dimensions on the blockmould and working pressure indictes that the unit is a kind of pressure vessel (box) and needed to be used specifed materials and inspection from a notify body.(TUV-Bureu Veritas vb) The certificates for inpection will be delivered together with the machine and this protects the buyer and the seller from the future problems against labour issiues. Machine is produced with fixed walls according to the demand we can also offer adjustable walls.
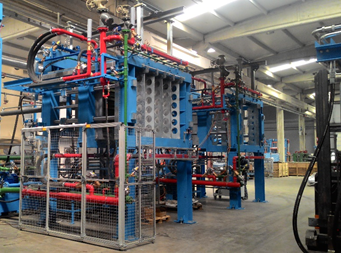
Shape Moulding with hi-tech process control with advantages like, fast mould change system with a clamping frame galvanized. Mould change within 15 minutes. Roboust body with complete milling job is done with all parts.Guide bars 2-4 pieces according to the size of the machine. Hydraulic system allows fast movemets with a soft action, or alternative Electrical drive even more faster action. All steam and air control is proportonally driven which creates energy saving and fast cycle times. Equipped with fast mould change system Proportional control for Steam & Air De-loading and Stacking robot Surface treatment mouldings Electrical drive with knee lever

AKKAYA EPS cutting line, equipped with oscillating cutting, rigid body, precise cutting properties. Modular system enables the line for upgrade whenever necessary, operator friendly control system for large productions. Special designed hot wire oscillation, has an automatic speed control system during cutting. This gives the change for fast cutting without any wire break. This option installed only on horizontal cutting station. With long stroke oscillation and adjustable oscillation speed guarantees the fastest cutting speed at all time with a smooth surface. Horizontal cutting unit equipped with wire break system, which stops the cutting for broken wire. Oscillation system operates only with autowire setting option.
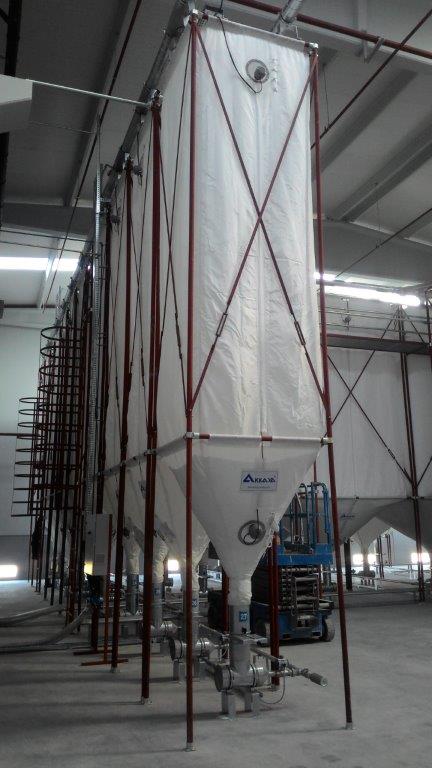
SILO BAGS Antistatic Polyester Material (Made in Germany) Custom made silo bags Silo-bag sewn of synthetic permeable to gas fabric, color similar to white in antistatic design (Electrostatic discharges are via woven carbon threads-not steel threads!) Silo top-cover with large filter cloth sections for optimal dust free venting Silo-inlet suitable for feeding pipes 200-250 mm i.d. (or as per requirement) Silo-outlet suitable for Akkaya- Silo-outlets for block or shape moulding production (or as per requirement) Two (2) inlets on side for level control sensors (min/max level) Zipper in the cone part for complete silo cleanout SILO FRAMES Corrosion protected 1 layer primer painted Custom Made Silo Frames Produced by round pipe or rectangular profile which is calculated and designed according to the silo volume. It is protected by anti-rust.
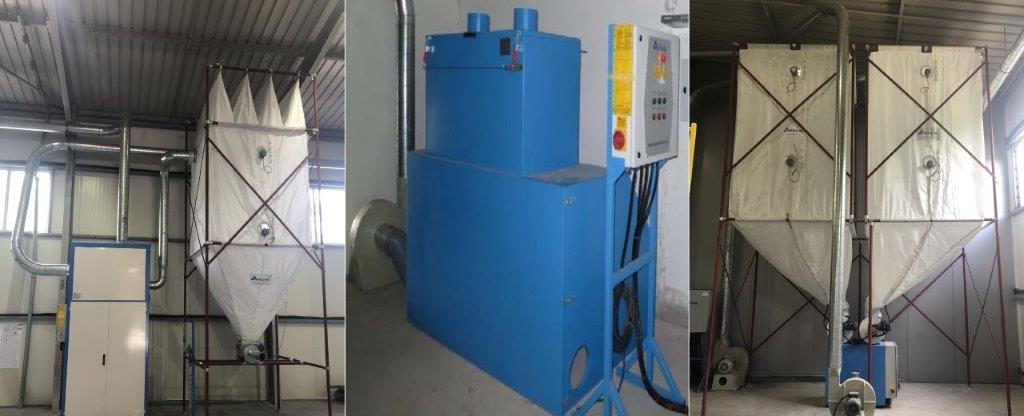
EPS PRE CRUSHER UNIT-AKM: Unit used for the recycling of scrap materials. With opening on the top 1230x600 mm built into sound insulated cabinet.(4 Kw) with 6 mm screen 10 m3/h, with 10 mm screen 15 m3/h Density range: 6-35 kg/m3. Other screen sizes upon request. Made by mineral wool,painted steel sheet. TRANSPORT FAN 1 Pcs Type: FHR 18 5,5 Kw EPS COMPLETE DE-DUSTING UNIT-ATM: Unit used to collect EPS dust generated during the recycling process. In complete sound insulated cabinet with one dust-separation unit and transport fan ( 4 Kw) to transfer the recycled material to the storage silos as well as blower (2,2 Kw) to transfer the dust to the filter unit. Max. 300 lt. filter bags to filter the dust coming from the dust separation unit. COMPACTOR FOR DUST TYPE-ATS: During the recycling process, the dust generated in the De-duster unit is collected in the silo. Machine for compacting the dust which remains in the silo that located below the dust filter groups. EPS MIXING STATION-AMX: 2 rotary type mixers 400 mm diameter. 1 rotary is running at constant speed (virgin material). 2 rotary is running upon mixing percentage ,controlled electronically. The system includes two identical silos , one is for virgin material and second one is for crushed material. Capacity: 10 m3 Connection dimension: R200 pipe.
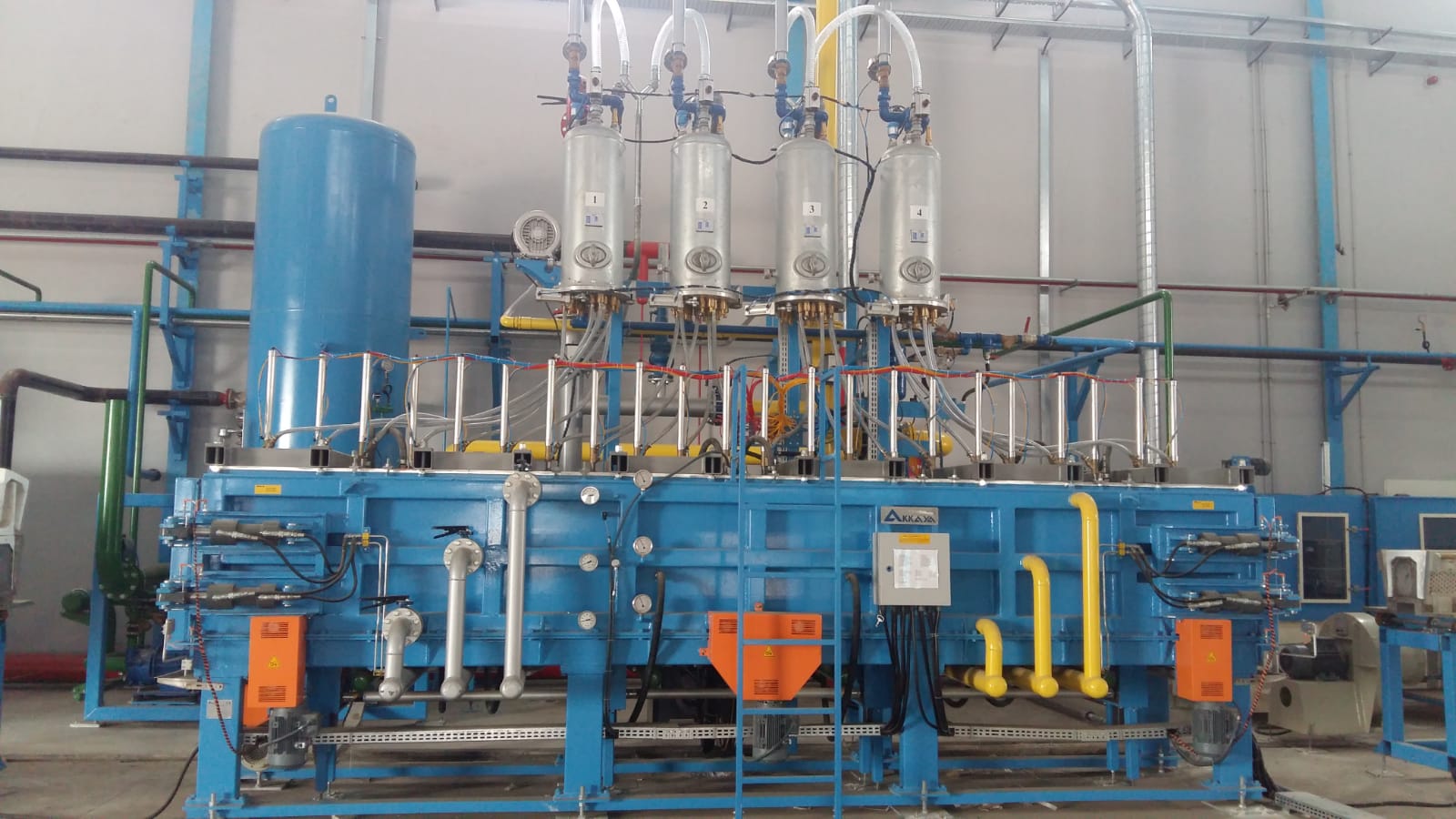
General explanation of the process: The machine is located horizontally with two door opening on the left and rigth sides.Machine itself has a fixed mould for the top part of the element and the moulds are external for each dimension. Top of the machine can be dismantable for preparetion and service during the operation. Movement: For the top figures on the element and demoulding step , bottom of the machine is moving Max.100 mm by Spindle Drive (SERVO). Filling of the machine: Material filling of the machine is done by fill injectors with quantity of 2 pcs every 50 cm distance.And has a filling tank 4 pcs of 150 lt volume which is suitable for minimum two continous cycles. Cooling: The top of the machine has a fixed cooling with water. And the bottom part(mould )has a self cooling when the mould is deloaded from the machine. Demoulding: Bottom of the machine is moving by spindle drive up to 100 mm tol et the mould come out of the steaming chamber.Then with a crane finished parts are taken out from the mould by operator manually. Vacuuming: The machine has a vacuum system with 2 vacuum pumps 5.5 Kw each and a vacuum tank 5 m3 to prevent enough vacuum for the process. Steaming: The body of the machine has a design to have a good fusionon the all sides of the part even on the inserted parts with cross steaming process from top to bottom as well as inverse direction. Steaming is controlled with a proportional steam valve and a feed back from a foam pressure sensor to have less stabilization time and enough steaming, which is located on the fixed side of the machine. -Process Control: By Siemens S7-200 type PLC unit with a touch screen display from Siemens. Operetaion Language English. All the process is controlled via touch panel and process continued automatically for every cycle. Mould Inserts: The mould (female part)has a design like butterfly which means moveable both walls with a angle 30°.This helps to put the metallic and ceramic inserts on the outer walls of the part and the metallic structure inside the material.
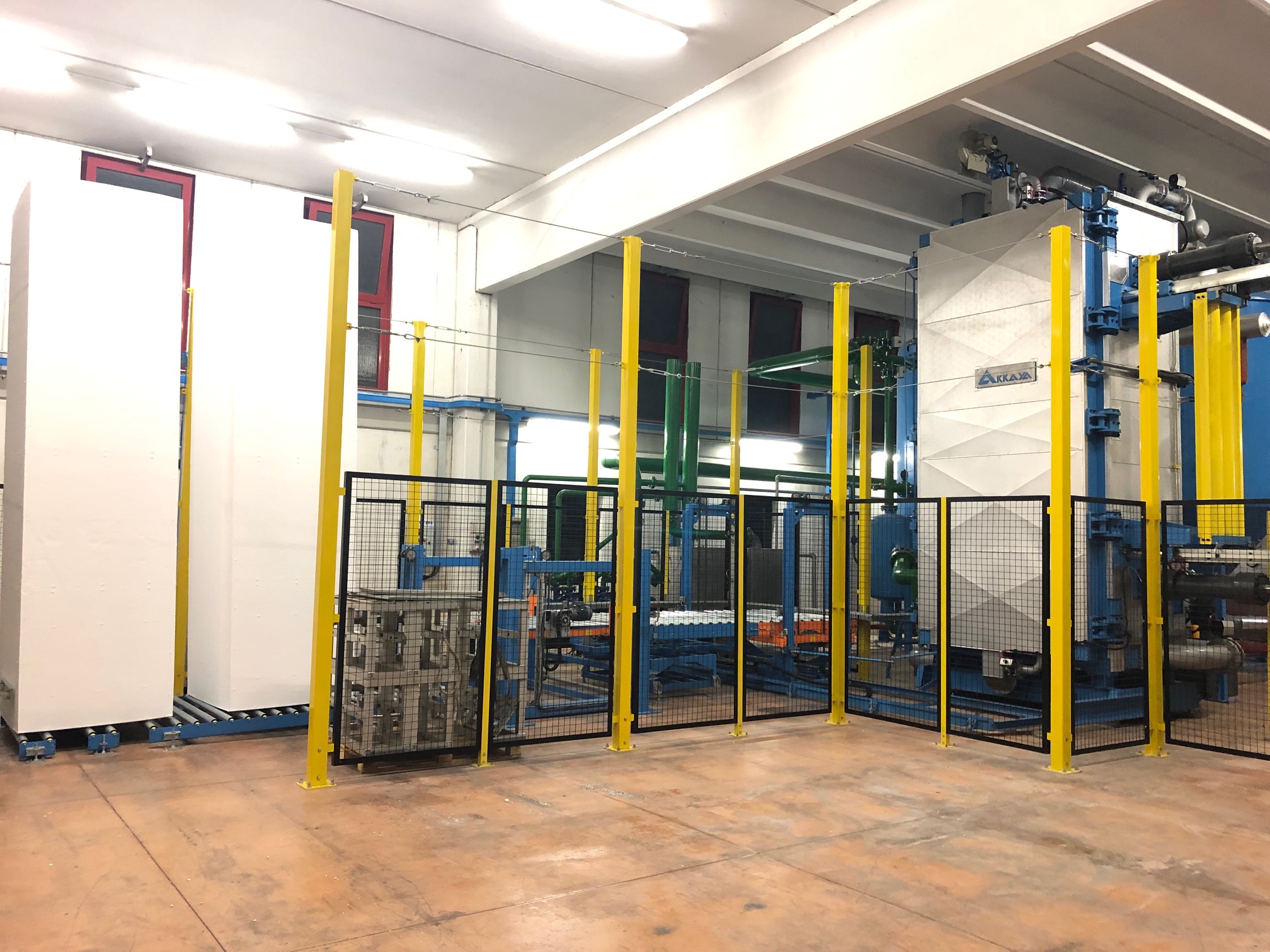
Blockmould is designed in vertical shape , and only one side openning which ensures the steam and vacuum tigthness 100 % during the process. This also needed for the pressure sertification and during operation machine needs less service. Described dimensions on the blockmould and working pressure indicates that the unit is a kind of pressure vessel(box) and needed to be used specified materials and inspection from a notify body. (TUV-BureuVeritasvb) The certificates for inspection will be delivered together with the machine,and this protects the buyer and the seller from the future problems against labour issues. Machine is produced with adjustable walls with hydraulic drive. Machine steam chamber made of SSWW (stainless steel wedge wire) with 0,25 mm openning. 12% plate open surface for slots different for each plate . This accelerates the steam and vacuum cycles and in the end cycle time shortens. The plates connected with 6 screws ,easy to service when needed. Machine filling is done on the top of the mould operated with hydraulic piston , openning diameter 250 mm. This allows fast ad homogenous filling with vacuum .The difference between top and bottom part is max 3 % different in density. This brings a big advantage esspecially producing with scrap material.
No represented companies found.
- AKKAYA
- AKKAYA EPS EPP PRDODUCTION TECHNOLOGIES