Company Name | Contact Info | Location | ||||||||||||
---|---|---|---|---|---|---|---|---|---|---|---|---|---|---|
GÜVEN TEKNİK MAKİNA KALIP SAN. DIŞ TİC. LTD. ŞTİ.
Kavaklı Mah. Pamukova Sok. No: 6 Kavaklı Silivri / / İSTANBUL / TÜRKİYE
|
Contact Info: +90 212 485 0967
|
Hall: 12
Stand: 1241B-1230B
|
||||||||||||
Product Groups | ||||||||||||||
|
- Company Info
- Products
- Represented Companies
- Company Brands
GT Form is the leader thermoform and mould manufacturer company in Turkey, with turn key innovative solutions which has been manufacturing inmould cutting tools and all equipments for Tilt bed Thermoform and Steel Rule Die Thermoform machines in its 5,000 square meter production facility with a staff of 35 years of experience. GT Form has been operating own facility with team of 105 expert staff and R&D department, presenting innovative solutions, rebust thermoformers at a resonable price, has grown into a position to export to 5 continents and more than 20 countries. GT Form provides service with more than 400 machines and more than 1000 molds in more than 30 countries in 5 continents with its turnkey production lines. GT Form, which has taken its place among the most important brands of the world packaging industry with its reliable brand and fast after-sales service, is the only and leading company in Turkey that manufactures both machinery and molds.

Effective forming area: 700×400 mm. Extra reinforced monolithic body and reinforced mould holding and cutting systems. Maximum forming depth: 150 mm. Speed : Max 45 production cycle ( 71mm-1.5 gr PP ) Production material: PP, PET, PS Max width of sheet: 710 mm Power : Three - phase neutral + G 3/PE, 50 Hz, 400 V Electric consumption 70 Kw/h (71mm-1.5 gr pp ) No need preheating with the advanced heaters design. Niddle bearing systems for mould holder arms and moving systems. Omron Servo Drive main motor Omron Servo drive plug assist Motor (with automatic lubrication) Omron Servo drive chain pulling engine. Sew Eurodrive Gear Box. DVP Brand (Italian) or Becker Brand (German) vacuum Pump. Bekamaks Brand (German) automatic central greasing. Rittal or Pfannenberg Brand (German) air conditioner for electric cabin. Ceramicx Brand ( Ireland ) or Elstain Brand (German) H Series Ceramics heaters. SMC brand (Japan) grease-free operating pneumatic valves. Mac brand (American) forming valves. Full automatic Omron motion control operation. 24 area controlled upper pan heat controlling. 4 area controlled lower pan heat controlling. 10 year warranty for machine cam. 5 years warranty for special design chain guides. 5 years warranty for plug assist mechanic system. 1 year warranty for general parts and electtronic parts. Powered solid main body for high speed. Special design cam system for high speed. Special production steell ejector pistons. Motorized PLC control cutting design.
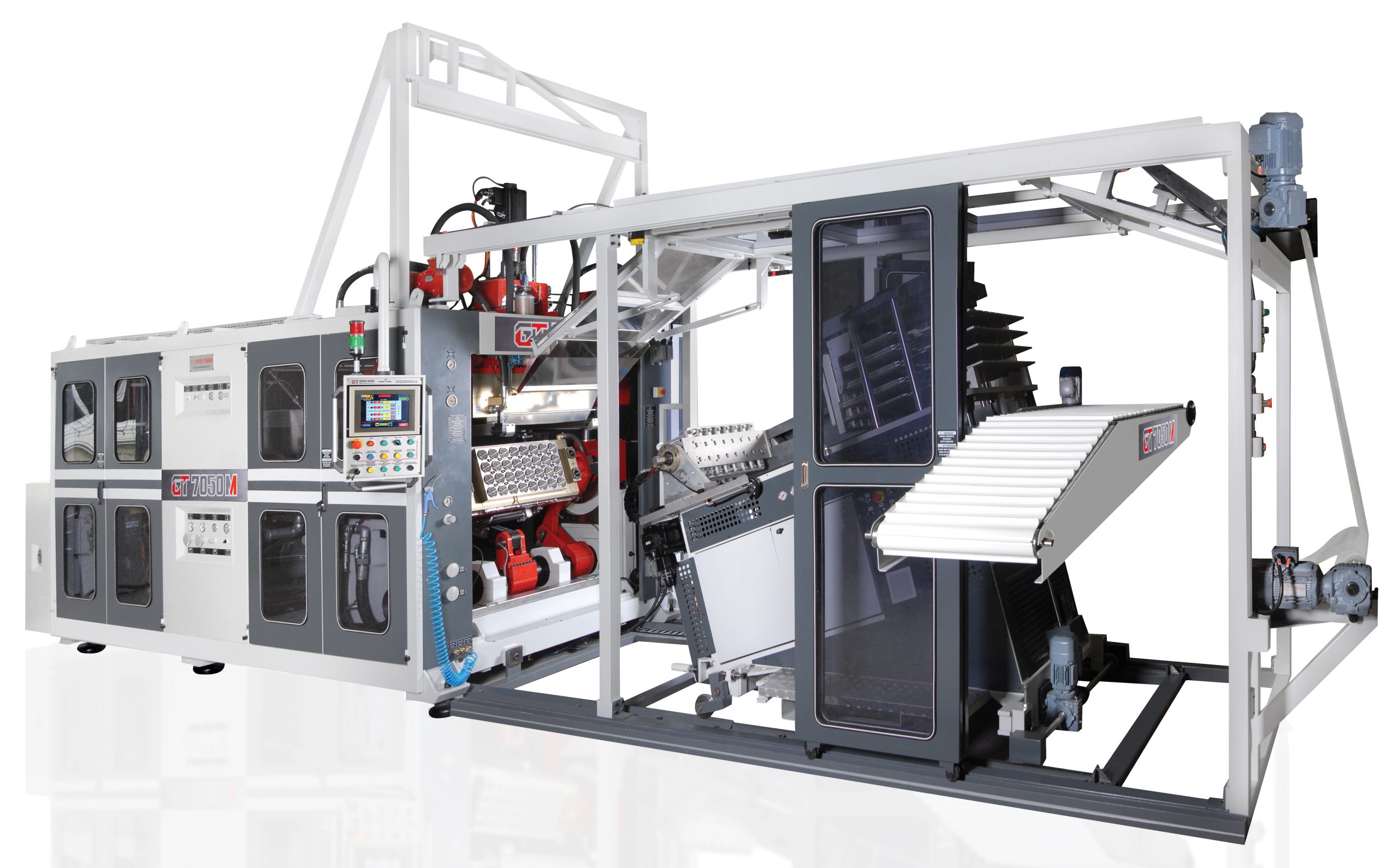
TECHNICAL SPECIFICATIONS OF GT 7050 M THERMOFORM MACHINES Effective forming area: 700×500 mm. Extra reinforced monolithic body and reinforced mould holding and cutting systems. Maximum forming depth: 150 mm. Speed : Max 45 production cycle ( 71mm-1.4 gr PP ) Production material: PP, PET, PS Max width of sheet: 710 mm Power : Three - phase neutral + G 3/PE, 50 Hz, 400 V Electric consumption 70 Kw/h (71mm-1.5 gr pp ) No need preheating with the advanced heaters design. Niddle bearing systems for mould holder arms and moving systems. Omron Servo Drive main motor Omron Servo drive plug assist Motor (with automatic lubrication) Omron Servo drive chain pulling engine. Sew Eurodrive Gear Box. DVP Brand (Italian) or Becker Brand (German) vacuum Pump. Bekamaks Brand (German) automatic central greasing. Rittal or Pfannenberg Brand (German) air conditioner for electric cabin. Ceramicx Brand ( Ireland ) or Elstain Brand (German) H Series Ceramics heaters. SMC brand (Japan) grease-free operating pneumatic valves. Mac brand (American) forming valves. Full automatic Omron motion control operation. 24 area controlled upper pan heat controlling. 4 area controlled lower pan heat controlling. 10 year warranty for machine cam. 5 years warranty for special design chain guides. 5 years warranty for plug assist mechanic system. 1 year warranty for general parts and electtronic parts. Powered solid main body for high speed. Special design cam system for high speed. Special production steell ejector pistons. Motorized PLC control cutting design.
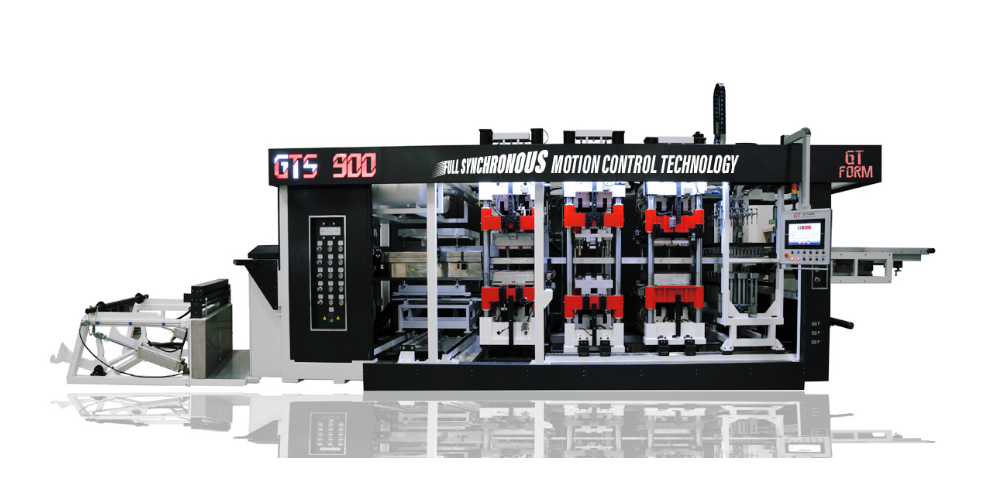
GTS 900 STEEL RULE CUTTING MACHINE GENERAL SPECIFICATION High performance, easy and safe operation with high techology. Rebust and solid machine body specially for high speed and non-stop production. Smart speed setting ability by touchscreen. Advanced heating system with izolated ceramic heater. NO NEED FOR PREHEATER. Quick tool changing and smart tool locking system. Reliable after sale service. Latest generation of software program and touch screen operating panel. High speed modem connection in order to facilitate after sale support. Induvidual lubrication inlets for each bearing.Technical Specifications Model : GTS 900 Maximum tool size : 900 630 mm Pozitive stroke : 150 mm Negative stroke : 150 mm Production material : PP, Pet, PS, PVC, OPS Material thickness : 1.5 mm ( Maximum ) Pet 2.0 mm PS, OPS, PVS, PP Lenght of the heater pan : 2300 mm Upper heater pan power : 97 Kw Lower heater pan power : 117 Kw Dry cycle : 80 cycle Vacuum pomp power : 3 kw Air requirement ( filtered air ) : 7 bar Electricity: 3 Phases 380 vollt 50 Hz 1. Feeding Unit Pneumatic roll lifting unit. Double roll lifting capacity. Sheet entrance ceramic side heaters for sheet transport. Nonstop unwinding system. 2. Chain & Chain Rails Omron servo motor chain pulling system from front side. 55 Hrc heat treatment steel channel for chain transport. ( Not Aluminum !!! ) 42 Hrc custom manufacturing chain. Aluminum body with water cooling system. Dropsa Automatic lubrication for chain rails. Automatic sheet stretching ability. Motorised chain rails distance adjustment ability controlling by touchscreen. 3. Heaters Elstain brand izolated, energy saver H series ceramic heaters. 13 line standart ceramic heaters. 2360 x 935 mm dimensions heater trays. No need for pre heaters. Hig precission temperature controling with the horizontal and vertical cross heater design. Close timbered ceramic heaters with short gaps. 23 zones controlled upper pan. 13 zones controlled lower pan. Thermocouple PID temperature controoling system. Sheet melting laser sensors. Upper heater total power: 97 Kw standart. Lower heater total power: 117 Kw standart Anti-vibration heater trays lineers mowing design from bottom. 4. Forming Station 4 columns, each columns are 100 mm heavy duty shafts. Servo motor driven plug assist system. Servo motor driven, clamping force 60 ton. Max. Tool size 630mm x 900 mm. Max. Stroke up and down 150 mm. Motorised up and down height adjustment ability controlled by plc. Lineer system clamping frame design. Automatic lubrication for clamping frame. Induvidiual lubrication feeding for each beraing. Needle type heavy duty bearings. Flow rate controlling system for cooling water. Faster tool change, quick mould locking and automatic centering. Upper block take up system with support piston. 5. Punching Station 4 columns, each columns are 100 mm heavy duty shafts. Servo motor driven, clamping force 60 ton. Two movable platen ( upward and downward ) driven by Servo motors. Max. Stroke up and down 150 mm. Motorised high precission punching system for upper platen. Induvidiual lubrication feeding for each beraing. Needle type heavy duty bearings. Upper block take up system with support piston. ( to adjust paralelling between of the platens ) 6. Cutting Station 4 columns, each columns are 100 mm heavy duty shafts. Servo motor driven, clamping force 60 ton. Two movable platen ( upward and downward ) driven by Servo motors. High precisse heating system for cutting knife controlling by touchscreen. Motorised X-Y position adjustment with lineer scale. Quick knife fixing. Cutting platens with minimal deflection to increase knife life. Induvidiual lubrication feeding for each beraing. Needle type heavy duty bearings. Upper block take up system with support piston. ( to adjust paralelling between of the platens ) 7. Servo motorised Upward Stacking System -Lower cost with high efficiency. -A-B stacking. -High accuracy linner guides. 8. A-B-C Upward 3 Axess Robot Stacking System
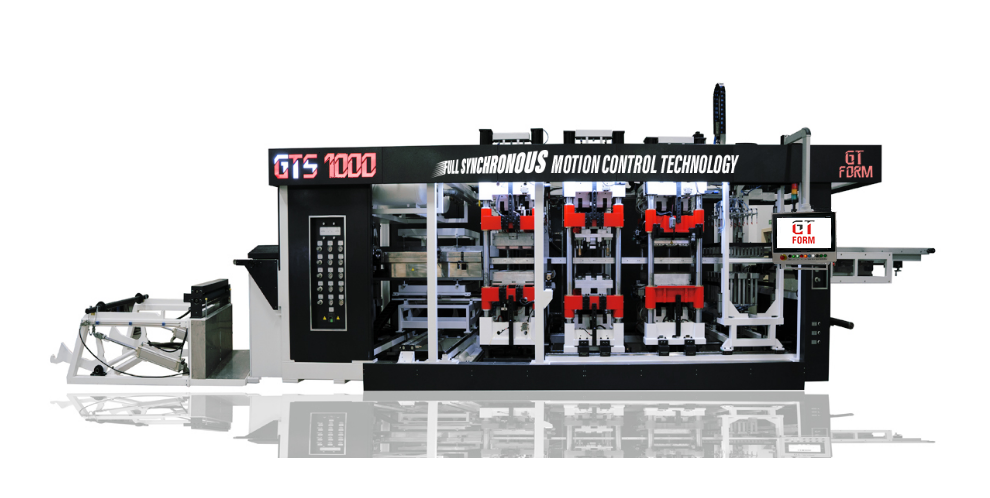
Technical Specifications; Model GTS 1000 (Form- Punch- Cut- Stack) Maximum tool size ( With out stretching ) 1140 800 mm Maximum tool size ( With stretching ) 1000 790 mm Pozitive stroke 150 mm Negative stroke 150 mm Production material PP, Pet, PS, PVC, OPS Material thickness 1.5 mm ( Maximum ) Pet 2.0 mm PS, OPS, PVS, PP Lenght of the heater pan 2300 mm Upper heater pan power 96.2 Kw Lower heater pan power 91.8 Kw Dry cycle 82 cycle Vacuum pomp power 3 kw Air requirement ( filtered air ) 7 bar Electricity 3 Phases 380 vollt 50 Hz Brands of the used equipments Omron brand (Japan ) servo motors and drivers. Omron brand (Japan ) Plc software. Omron brand (Japan ) touchscreen. Sew Eurodrive brand ( German ) gear boxes and AC motors. DVP brand ( Italian ) or Becker brand ( German ) vacuum pomp. Smc brand ( Japan ) fast communication pneumatic valves. GT Brand ultra energy save forming valve system. Elstain brand ( German ) or Ceramicx ( İreland )H series, black energy saver ceramic heaters. Pfennenberg or Rittal brand ( German ) air conditioner for electric cabinet. Ina, Faq, Ors brand bearings. OMRON, CELDUC, SIEMENS, SCHNEIDER, EBM PAPST brand electric componenets. 1. Feeding Pneumatic roll lifting unit. Double roll lifting capacity. Sheet entrance ceramic side heaters for sheet transport. Nonstop unwinding system. 2. Chain & Chain Rails Omron servo motor chain pulling system from front side. 55 Hrc heat treatment steel channel for chain transport. ( Not Aluminum !!! ) 42 Hrc custom manufacturing chain. Aluminum body with water cooling system. Dropsa Automatic lubrication for chain rails. Automatic sheet stretching ability. Motorised chain rails distance adjustment ability controlling by touchscreen. 3. Heaters Elstain or Ceramicx brand izolated, energy saving H series ceramic heaters. No need for pre heater ! 42 Zones high precission temperature controling with the horizontal and vertical cross heater design. Close timbered ceramic heaters with short gaps. 27 zones controlled upper pan. 15 zones controlled lower pan. Thermocouple PID temperature controoling system. Sheet melting laser sensors. Upper heater total power: 127,8 Kw standart. Lower heater total power: 114 Kw standart Anti-vibration heater trays lineers mowing design. 4. Forming Station 4 columns, each columns are 100 mm heavy duty shafts. Servo motor driven, static clamping force 110 ton. Max. Tool size 1000 x 790 mm. Max. Stroke up and down 150 mm. Motorised up and down height adjustment ability controlled by plc. Lineer system clamping frame design. Automatic lubrication for clamping frame. Induvidiual lubrication feeding for each beraing. Needle type heavy duty bearings. Flow rate controlling system for cooling water. Faster tool change, quick mould locking and automatic centering. Upper block take up system with auxilary piston. 5. Punching Station 4 columns, each columns are 100 mm heavy duty shafts. Servo motor driven. Two movable platen ( upward and downward ) driven by Servo motors. Max. Stroke up and down 150 mm. Motorised high precission punching system for upper platen. Induvidiual lubrication feeding for each beraing. Needle type heavy duty bearings. Upper block take up system with support piston. ( to adjust paralelling between of the platens ) 6. Cutting Station 4 columns, each columns are 100 mm heavy duty shafts. Servo motor driven, static clamping force 144 ton. Two movable platen ( upward and downward ) driven by Servo motors. High precisse heating system for cutting knife controlling by touchscreen. Motorised X-Y position adjustment with lineer scale. Quick knife fixing. Cutting platens with minimal deflection to increase knife life. Induvidiual lubrication feeding for each beraing. Needle type heavy duty bearings. Upper block take up system with support piston. ( to adjust paralelling between of the platens ) 7. Servo motorised Upward Stacking System ( Standart ) -Lower cost with high efficiency. -High accuracy linner guides. 8.
No represented companies found.
The company has no registered brand information.