Company Name | Contact Info | Location | ||||||||||||
---|---|---|---|---|---|---|---|---|---|---|---|---|---|---|
SHANGHAI JIAHAO MACHINERY CO.,LTD
NO.333 ANCHENG RD, ANTING NEW TOWN, JIADING DISTRICT / / SHANGHAI / CHINA
|
Contact Info: +86 139 1791 9565
|
Hall: 10
Stand: 1017D
|
||||||||||||
Product Groups | ||||||||||||||
|
- Company Info
- Products
- Represented Companies
- Company Brands
SHANGHAI JIAHAO MACHINERY CO.,LTD
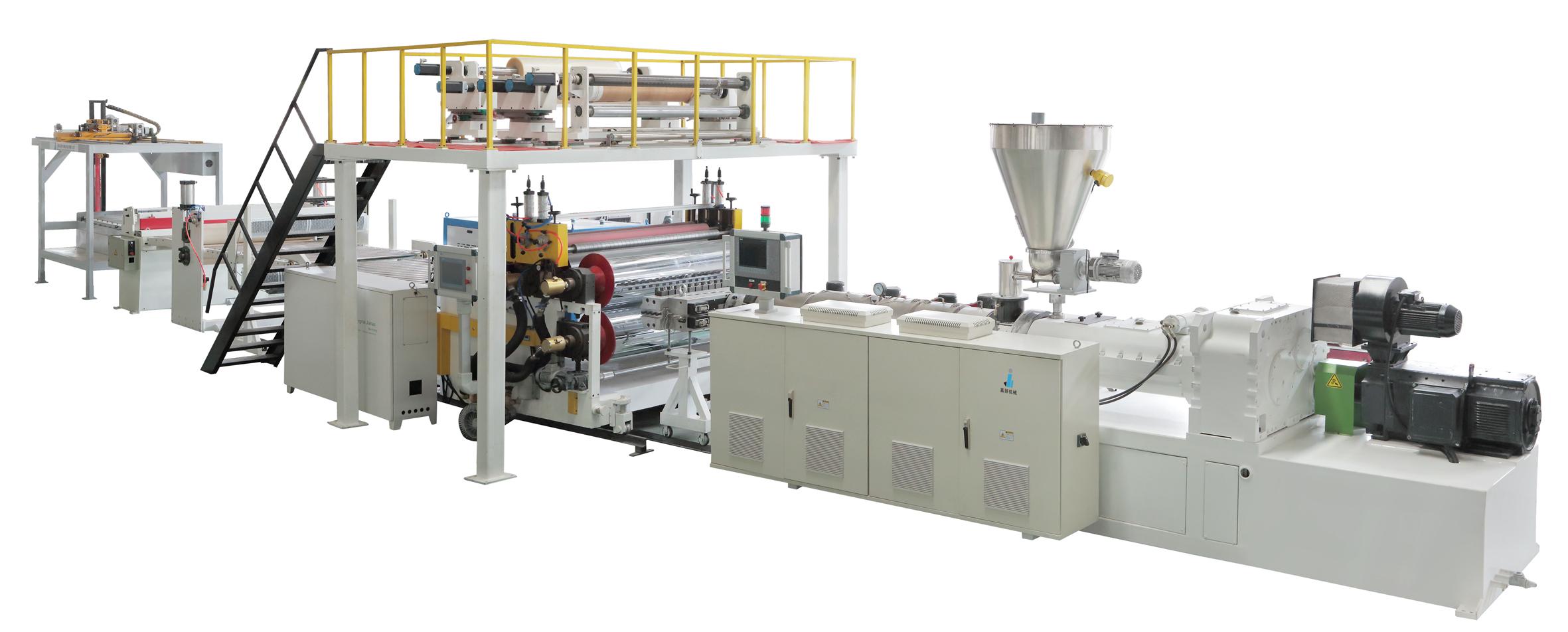
patent design on base of over 10 years sheet extrusion and lamination production experience, the production will be energy saving ,high efficient and stable. The embossing roller replacement be easier Easy operation and maintenance and QC checking, and working with high safety Compare with other companies machine, our online lamination system make the wearing layer have better plasticization and more peef strength on product surface. Pattern film and wearing film can connect, which make no waste during change winders.. Suitable for special SPC flooring formulation, with good performance on shrinkage and bending. Equipped with embossing tracking system to make sure depth of embossing be even all the time.. Make special design for SPC flooring production and offer turnkey project.
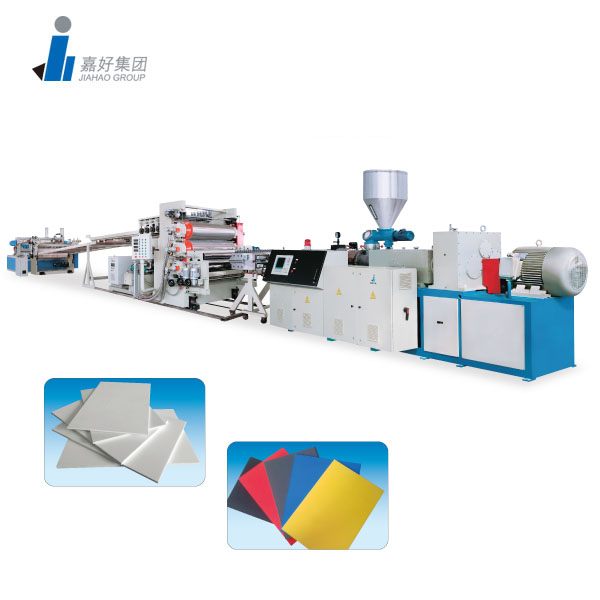
PVC sheet and board extrusion machine is a key piece of equipment in the plastic processing industry used to produce PVC (polyvinyl chloride) sheets and boards. Here is an introduction to its main components and functions: 1. Extruder1: o Screw: The screw is a core component of the extruder. It is responsible for transporting, compacting, melting, and homogenizing the PVC raw materials. The screw typically has different sections, such as the feeding section, compression section, and metering section. The feeding section has a larger diameter to facilitate the intake of materials, while the metering section has a smaller diameter to ensure accurate extrusion of the molten plastic. o Barrel: The barrel surrounds the screw and provides a heating and cooling environment for the plastic materials. The barrel is usually heated by electric heating elements or other heating methods to melt the PVC materials. At the same time, cooling systems are also installed to control the temperature of the barrel and ensure the stability of the extrusion process. o Drive System: The drive system is used to drive the screw to rotate, providing the power for the extrusion process. The drive system usually consists of a motor, a reducer, and a coupling, which can ensure the stable operation of the screw at a certain speed. 2. Die Head2: The die head is connected to the extruder and is responsible for shaping the molten PVC into the desired sheet or board shape. It has a specific structure and size according to the product requirements, such as a T-die for sheet extrusion or a special-shaped die for board extrusion with specific profiles. o The die head needs to ensure the uniformity of the extruded material flow, so that the thickness and width of the produced sheets or boards are consistent, and the surface quality is good. 3. Calibration machine 4. Cooling and haul off System: o After the PVC material is extruded and shaped, it needs to be cooled quickly to solidify the structure and maintain the shape and properties of the product. The cooling system usually consists of a cooling tank or a series of cooling rollers. The cooling medium can be water or air, depending on the specific requirements of the production process1. o The cooling system needs to have sufficient cooling capacity and good temperature control performance to ensure the uniformity of the cooling of the sheets or boards and prevent deformation and other quality problems. 5. Cutting and Stacking System: o The cutting system is used to cut the continuous extruded PVC sheets or boards into the required lengths. It can be equipped with a variety of cutting methods, such as saw cutting, knife cutting, or laser cutting, depending on the thickness and hardness of the materials and the accuracy requirements of the cutting. o The stacking system is used to stack the cut sheets or boards neatly for subsequent packaging and transportation. The stacking system needs to have high automation and stability to ensure the efficiency and quality of the stacking process. In general, a PVC sheet and board extrusion machine is a complex and sophisticated piece of equipment that integrates mechanical, electrical, and thermal control technologies. It can produce high-quality PVC sheets and boards with different specifications and properties by adjusting the process parameters and equipment configurations according to the specific requirements of the products.
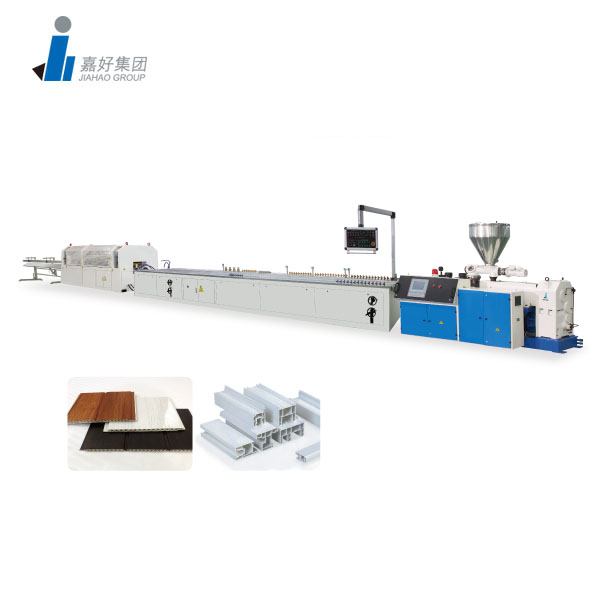
YF series PVC profile production line is mainly used to produce PVC door and window profilewide door panel, window sill and multi hole cable pipes ( 4 holes, 6 holes, 9 holes, etc). Thiskind of production line can adopt different kinds of extruders and moulds according todifferent profiles and be equipped with corresponding vacuum calibration unit, hauf-offcutting unit, tilting unit, etc. The haul-off adopts special rise and fall technology which ensures stable working and highdrawing force, The vacuum calibration unit adopts special eddy-increasing cooling system tosatisfy cooling, and high-speed extrusion, Cutter moving speed should be synchronous withhaul-off speed. All the operation was controlled by PLC, with professional design, stableoperation, fixed -scale cutting and equipped with dust-recycled device. Calibration unit has thespecification of 4m, 6m, 8m, 11m etc according to different moulds.
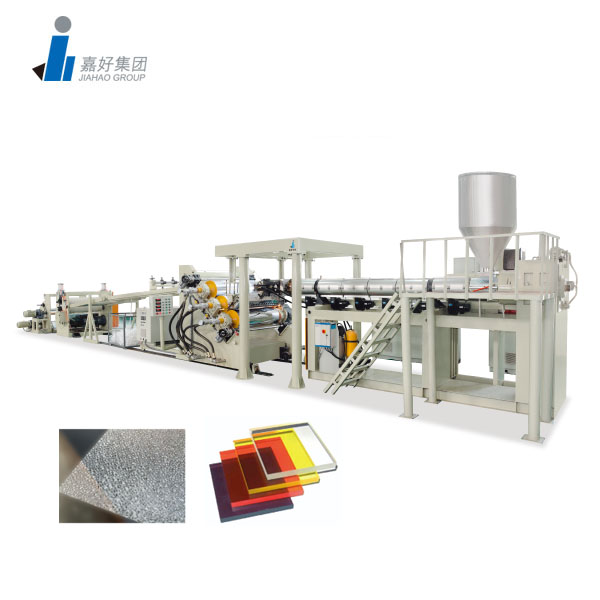
Our machine can produce PC/PP/PE/PS/ABS/PMMA SHEET AND BOARD PRODUCTION LINE . The products produced have the characteristics of high strength, good temperature resistance, good corrosion resistance, etc. Additives can be added according to different requirements, such as increasing strength, increasing endurance, increasing rigidity, height, embossing, frosting, etc. Main applications: such as packaging, printing, stationery, cultural relics, etc. Main products gift/advertising/document bags, lampshades, food packaging, etc.
No represented companies found.
The company has no registered brand information.