Company Name | Contact Info | Location | ||||||||||||
---|---|---|---|---|---|---|---|---|---|---|---|---|---|---|
GRUPAK PLASTİK MAK. İÇ VE DIŞ TİC. LTD. ŞTİ.
İSTOÇ 45. ADA NO: 18 / BAĞCILAR / İSTANBUL / TÜRKİYE
|
Contact Info: +90 212 659 6488
|
Hall: 8
Stand: 817
|
||||||||||||
Product Groups | ||||||||||||||
|
- Company Info
- Products
- Represented Companies
- Company Brands
We started our activities in 2003 with the sale of Plastic Packaging Machines and after-sales technical service. Since the day we were founded, we have acted as a reliable bridge between the Turkish Plastic Packaging Material manufacturers and the leading Plastic Packaging Machinery manufacturers from different countries. While choosing our representatives, we took care to have machine manufacturers who are experts in their fields and aim to use the latest technology in their production, in line with the importance we attach to experience and specialization. We are aware that we are on the right track as a result of the support and appreciation we have received from our customers. In line with the mission we have undertaken, reliable service without sacrificing quality would continue to be our basic principle.

It distinguishes itself from its competitors with its strong construction, long-lasting screws, fast and reliable after-sales service and high film quality. Extruder diameters of 45mm - 55mm- 65mm - 80mm- 100mm - 120mm, width options between 650mm and 3500mm are offered. High quality and suitable films produced in 2, 3 or 5 layers with multilayer film extruders depending on the film properties required by the customers, It is used in areas such as garbage bags, heavy-duty bags, chemical material bags, greenhouse film, shrink film, industrial stretch and food packaging.
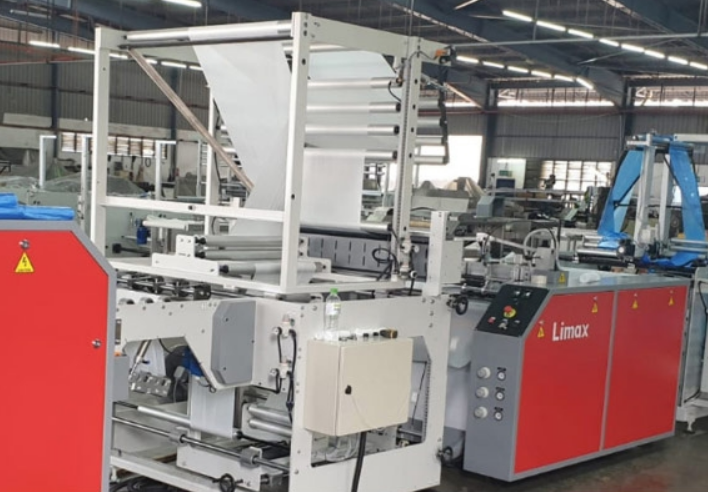
LIMAX company, with its experience in the sector, constantly renewed technology, and R&D investments, is a leading brand especially in roll garbage bags, industrial bag cutting, multi-line high-speed flat bag cutting machines and wicket bag cutting machines. It is known for its longevity and durability, with the highest quality equipment in its sector, especially in Europe, with its worldwide awareness and high quality used in its machines. With the ALPHA 1100 series, perforated roll garbage bag machines produced by the company, it is possible to produce either single line or double line options, t-triangle fold, c-fold and star welded productions in the configurations prepared in line with customer demands.
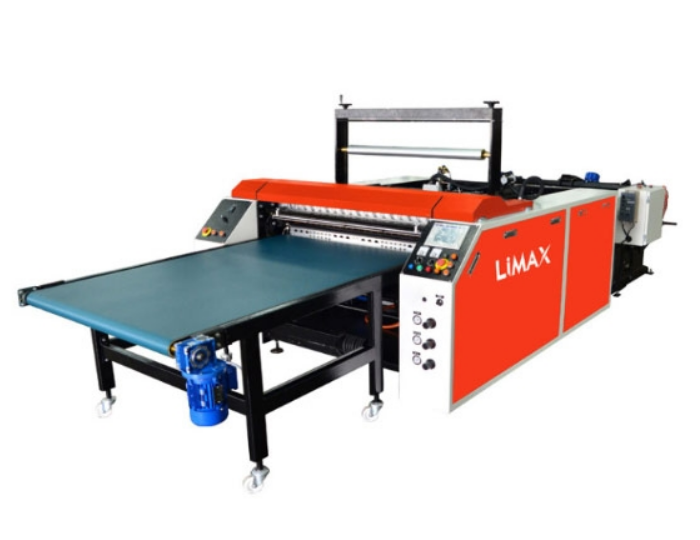
ALPHA series, with its flying knife system, has the feature of cutting flat bags with a minimum 200 mm, maximum 3 meters length, double layer thickness between 40 microns and 500 microns. With its servo motor feeding and needle-free stacking technology, it provides high-speed working performance in this type of bag production. With the bonding wires located on the upper and lower sealing jaws, it provides a single or double seam welded, uniquely robust final product. Thanks to the needle-free stacking system, With this, the stacking and inefficient working problems experienced by industrial bag manufacturers have been eliminated.
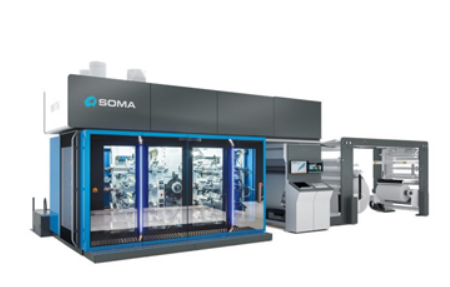
When designing Optima, we focused on bouncing and registration accuracy issues and developed Advanced Bounce Control System to raise your confidence in high speed printing of problematic designs. We implemented IRIS to address short run issues. We also made OPTIMA ready for Expanded Gamut, Enviromental (WB) Printing or UV LED.
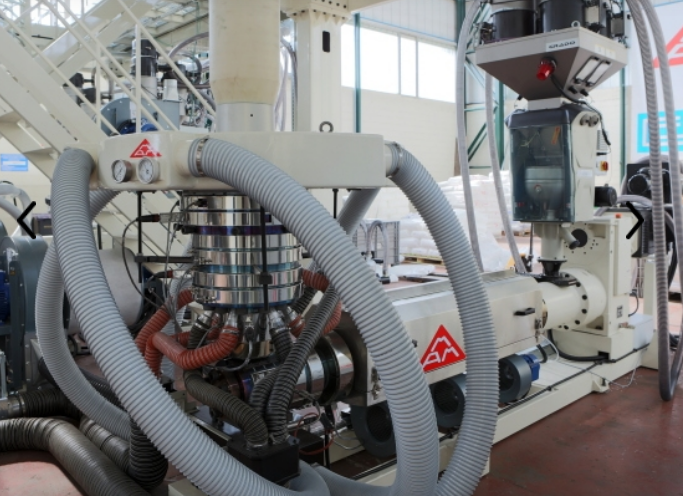
Founded in 1953, CMG-MAM is the leading company in the industry, specializing in the production of high density Mono and Coex Film Extruders. CMG-MAM HDPE MONO FILM EXTRUDERS; Screw Diameters: 50mm, 63.5mm, 70mm, 80mm Machine Widths: 1200 mm, 1400 mm, 1600 mm, 1800 mm, 2000 mm, 2200 mm Film Thickness: Between 10 microns-200 microns Head diameter options from 50 mm to 300 mm according to screw diameter and machine width. CMG-MAM HDPE ABC COEX FILM EXTRUDERS Screw Diameters: 50mm, 63.5mm, 70mm, 80mm Machine Widths: 1600 mm, 2000 mm, 2400 mm, 2800 mm, 3200 mm Film Thickness: Between 10 microns-200 microns Head diameter options from 175 mm to 650 mm according to screw diameter and machine width.
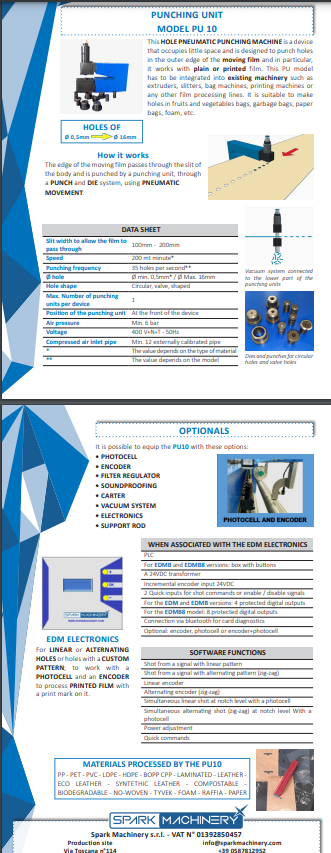
PUNCHING UNITS Perforation machines to punch holes in the OUTER EDGE of the moving film Especially recommended for PLAIN OR PRINTED PLASTIC FILM To be integrated into existing machinery such as extruders, welding machines, slitters, bag machines and in all production lines with MOVING FILM Possible shapes of the hole: circular - valve - euroslot - handle - drop shaped - for mulching For holes with a Ø ranging from 0,5mm to 100mm HOT NEEDLE MICRO PERFORATORS - HN MODEL Perforation machines to punch holes in MOVING FILM Especially recommended for PLAIN OR PRINTED PLASTIC FILM To be integrated into existing machinery such as extruders, welding machines, slitters, bag machines and in all production lines with MOVING FILM For holes with a Ø ranging from 100µ to 3mm
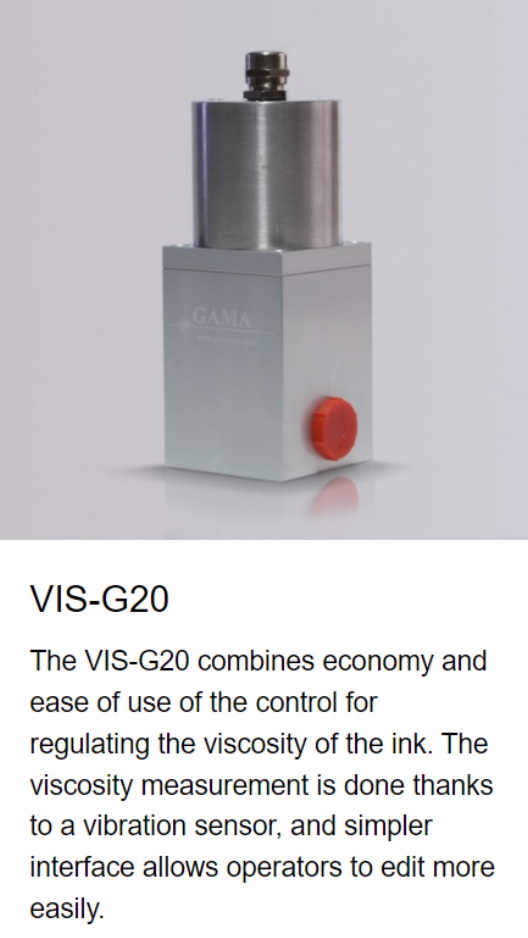
Gama Srl - ITALY; develops and manufactures ink control systems for the packaging, labelling, converting and commercial markets. More than 5,000 viscosity control systems installed worldwide bear the Gama signature. Gama s product range includes dropball and new generation ultrasonic (measuring with sound waves) viscosity control systems, ink cooling systems and magnetic ink filters for rotogravure and flexo printing machines, which can be used with water-based and solvent-based inks. With the use of viscosity control system, continuity of ink formulation is ensured and stable ink-solvent amount is obtained. With the system, deviations in viscosity value are controlled and savings are achieved in solvent-ink consumption. With all these advantages, the quality of the printing process is increased. With magnetic ink filters, which you can easily apply in your existing systems, metal dust particles in the ink line can be easily filtered. In this way, damage caused by scratches on the anilox is prevented and long-lasting usage times are ensured.
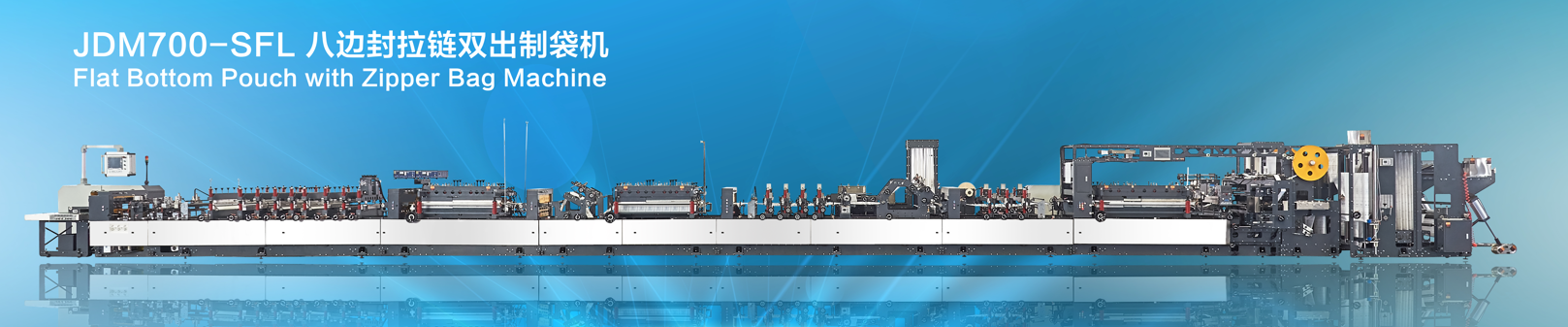
JUDING MACHINERY (SHANGHAI) Co., Ltd, Barrier bags, which have been increasingly used by the food industry in recent years, are available in different shapes and seams depending on the product characteristics; 3 different shapes and seams such as side sealing, doypack-stand up pouch, back seam (center seal & quattro) or flat bottom types are produced. Ju Ding Machinery manufactures 3 side seam, back seam and 4 side seam (quattro), locked or unlocked doypack and flat bottom (square bottom) With its bag cutting machines, it offers manufacturers the possibility to produce all versions of this type of bags. With its 26000 square meter smart production factory, Ju Ding Machinery has an annual production capacity of 400 cutting machines. cutting machines are distinguished from their competitors with their precise and high quality workmanship, strong mechanical design and smooth running performance, has become a preferred brand in the industry in the last few years. JDM600-S High Speed Vacuum Bag Cutting Machine with Three Side Sealing 600 AND 800MM JDM700-SFL Flat Bottom Bag Cutting Machine 450/700/800/1000/1200mm widths Possibility to apply coffee valve, plastic hand fitting, die cutting, double warp, perforated hole and different zipper types. JDM600-Z Bag Cutting Machine with Back & Four Side Seams (Quattro) 450/600/800mm widths This model, which is produced in different jaw widths according to the size of the bag to be produced, can be used in addition to central seam bags, called Quattro.
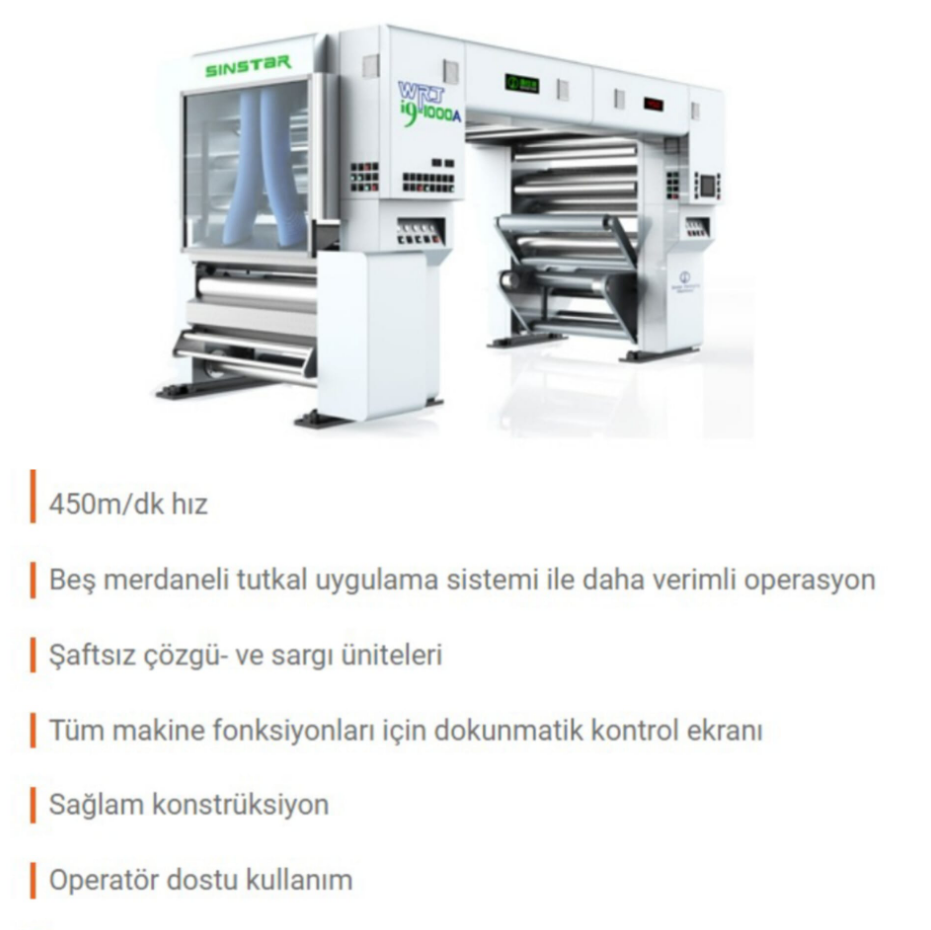
Sinstar Packaging Machinery Co., Ltd. is established in high-tech industrial zone in Chongqing City and has a production capacity of 200 units of solvent-free laminating machines per year. Sticking to the design concept of Innovation Changes the World, Innovation Rules the Future , the company has developed many technological innovations. Among these innovations: - Veneer Cavity Memory System - Error-free Adhesive Preparation System - Targeted Coating Weight Direct Entry System - Accurate Veneer Weight Detection System - Multiple Mixing Ratio Protection System - Zero Error Voltage Compensation System - Fast Cleaning System The company s successful models include the WRJi9, WRJFi9, S1L90 and WRJSLi5. It has more than 2000 machine installations worldwide and its machines are recognized for their simple operation, safety, and durability.
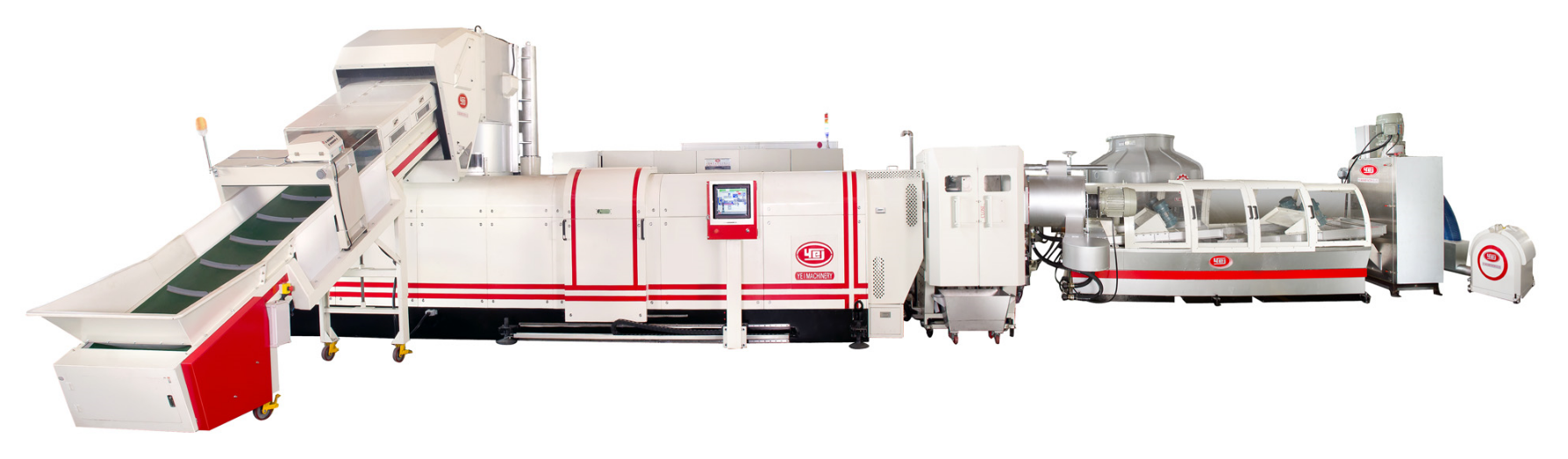
Optimization of the recycling experience. YE I s professional high-efficiency recycling machines are used in 120 countries around the world. As the first step of the plastic circular economy, recycling technology ensures efficiency and sustainability. Plastic recycling machine includes conveyor, shredder, extruder, screen changer, pelletiser, cooling equipment, silo and other optional devices. All equipment is integrated into one single customised production line. Simple and efficient operation methods can easily increase the production of high-quality plastic particles, and recycled pellets can be used in the manufacture of various products. YE I mainly offers two (2) types of waste plastic recycling machines, water-cooled and air-cooled. The way to distinguish which one to use is to look at the differences in materials and their properties. Currently commonly used are PP, PE, PS, ABS, PC, PLA, EPS, EPP, EPE, PET, PA... etc. materials.
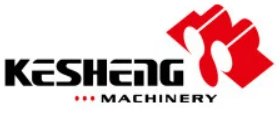
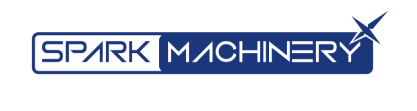
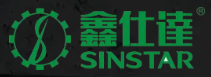
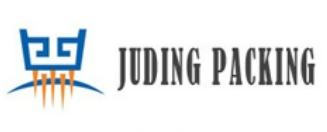
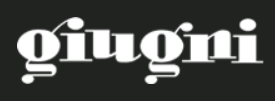
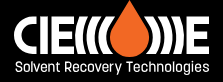
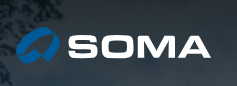
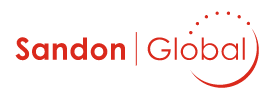
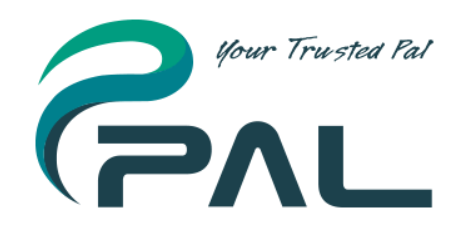
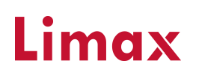

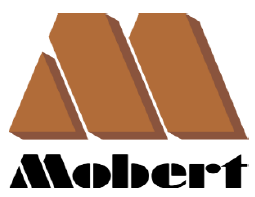
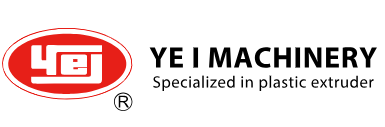
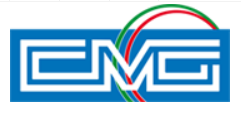
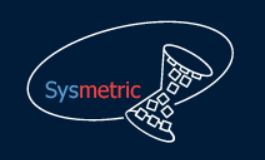
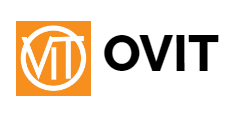
The company has no registered brand information.