Company Name | Contact Info | Location | ||||||||||||
---|---|---|---|---|---|---|---|---|---|---|---|---|---|---|
MOTAN GMBH
Max-Eyth-Weg 4288316 Isny / / / GERMANY
|
Contact Info: +49 7562 760
|
Hall: 12
Stand: 1204
|
||||||||||||
Product Groups | ||||||||||||||
|
- Company Info
- Products
- Represented Companies
- Company Brands
The motan group based in Constance was founded in 1947. As a leading provider for sustainable raw material handling, they operate in the areas injection moulding, blow moulding, extrusion and compounding. Innovative, modular system solutions for storage, drying, conveying, dosing and mixing of raw materials for the plastics manufacturing and processing industries are part of the application orientated product range. Production takes place at different production sites in Germany, India, and China. motan distribute their products and system solutions via their regional sales centres. With over 600 employees currently, a yearly turnover of roughly 147 million euros is achieved. Because of their network and long-standing experience, motan can offer their customers what they really need Individually tailored solutions with real added value.
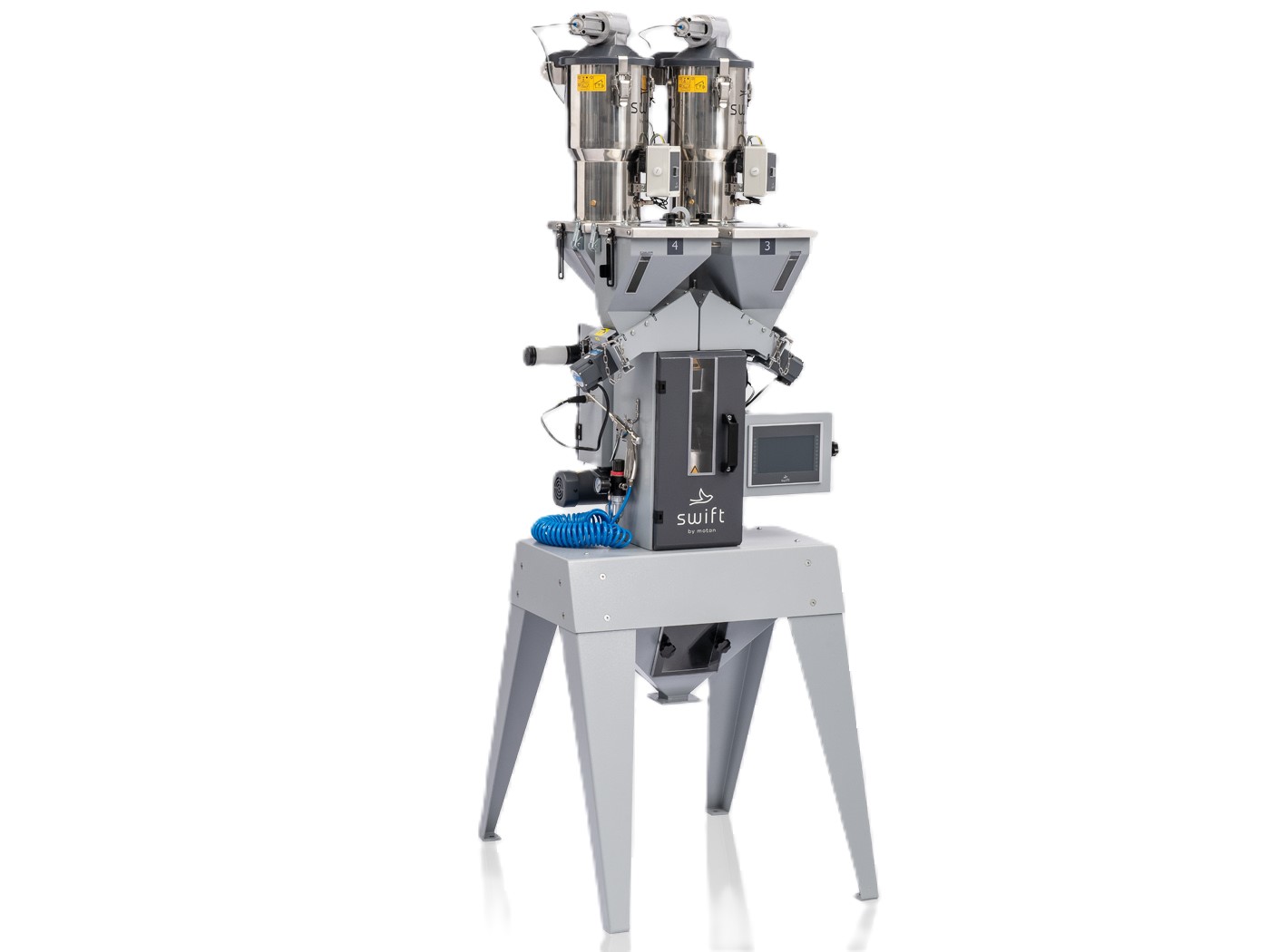
Innovative dual dosing methods The sBLEND G employs two distinct dosing methods: vertical slide valves for main components and screw feeders for precise additive dosing. This dual approach ensures unparalleled accuracy and flexibility. The bowl-shaped mixing chamber, equipped with an optimized agitator, guarantees homogeneous mixing in a dead-spot-free zone, monitored by the advanced sBLEND microprocessor control system. This allows for reducing additive quantities to the lower tolerance limit, ensuring cost savings without compromising quality. Versatile and modular design The sBLEND G unit supports gain-in-weight dosing and mixing for up to four materials, available in three sizes for throughput rates of 50, 130, and 300 kg per hour. The standard configuration includes two vertical slides, controlled by pneumatic cylinders, for precise dosing of main components like virgin material or regrind. For finer dosing and greater accuracy, optional screw dosing modules can be added. These modules prevent material trickle and avoid overdosing expensive additives. They are available in various sizes and can be removed and exchanged without the need for tools, offering flexible configuration to meet specific application requirements. Efficient cleaning and maintenance Designed for convenience, the sBLEND G features a quick-change system for dosing modules and quick-release screws, simplifying cleaning and material changes. The weigh bin and mixing chamber can be easily removed without tools. All contact parts are made of stainless steel, ensuring contamination-free operation and easy cleaning. The brushless, swivel-mounted dosing motors with integrated motor management are maintenance-free and easily removable, guaranteeing reliable continuous operation. Reliable and consistent performance The bowl-shaped mixing chamber design ensures a homogenous mix and consistent material discharge. When mounted on the processing machine inlet, the material path from the mixing chamber to the processing screw is minimized, preventing unwanted material segregation. Alternatively, the unit can be mounted on a frame and placed on the floor or serve as a central station for multiple processing machines. Advanced control and network integration The sBLEND G, like all swift units, features a modern microprocessor control with an innovative, open network architecture based on Ethernet. This allows for both direct operation via a 7-inch colour touchscreen and remote control. The sBLEND controller monitors and displays throughput and supports weight calibration, automatically calculating material addition speeds. Exceptional value and performance The sBLEND G stands out as a unit that combines motan s renowned quality with an excellent price-performance ratio and state-of-the-art control technology.
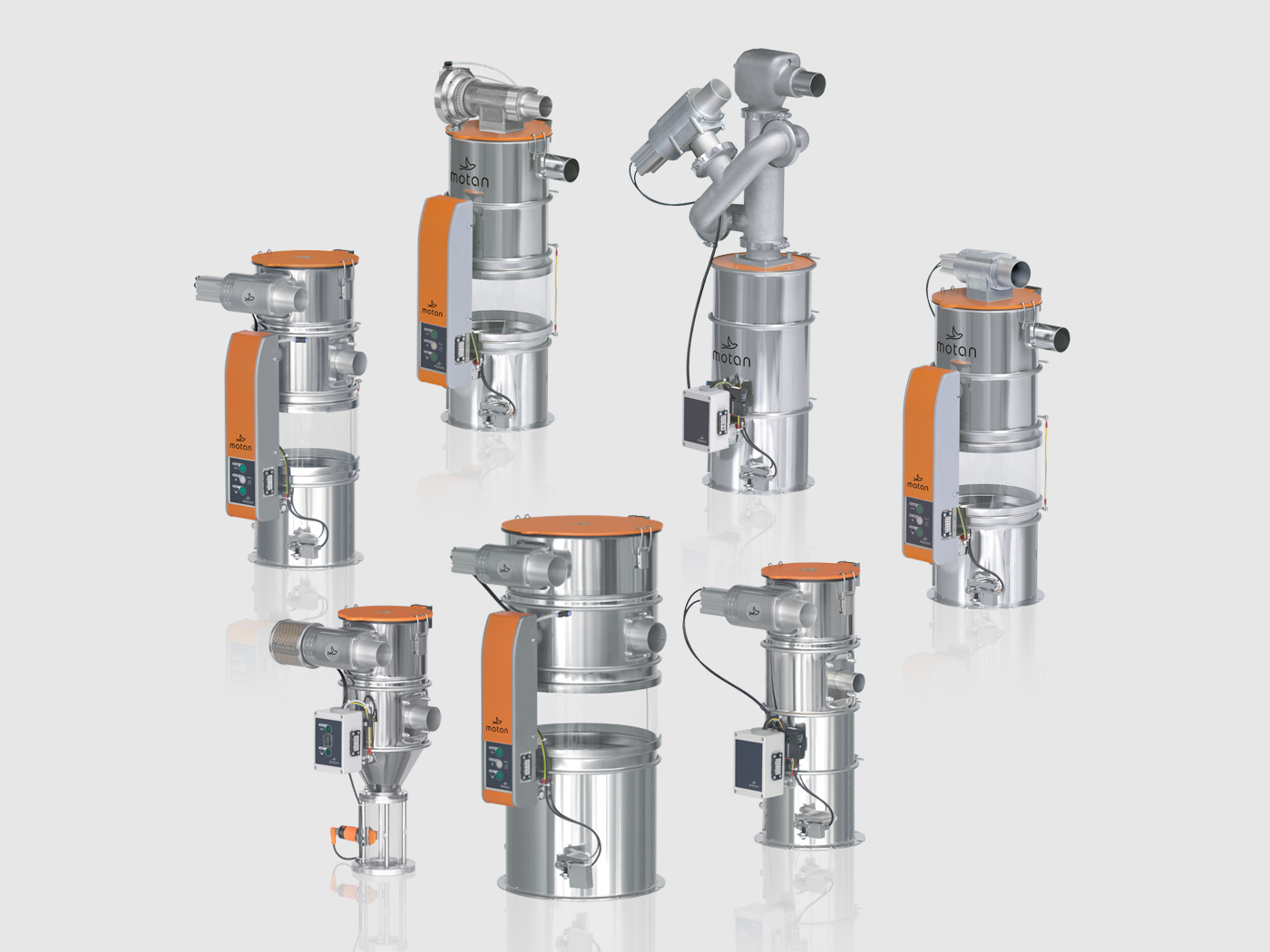
METRO G is the most comprehensive and flexible material loader range on the market. It combines the best of two established material loader ranges colortronic and motan. Whether simple or highly complex, METRO G s modular building block system will provide you with an individual solution tailored to your needs. Modular design No product redundancy - as your production requirements change so does the material loader. All material loaders are fully modular and can be matched to different throughputs and requirements depending on the application. Not only are there different material loader volumes but also different material inlet and outlet sizes which can be accurately adapted to suit throughputs and conveying distances. De-dusting module Guarantees consistent material quality for critical applications. The de-dusting module removes dust from high performance engineering plastics directly at the hopper loader, sending them to the central dust filter via the air flow. These expensive materials, now dust-free, can be processed without further delay. Vacuum module with Blow Back Safe option for very dusty materials. The implosion vacuum module with blow-back function enables safe cleaning of the screen filter for very dusty materials. The standard implosion cleaning is reinforced by additional blasts of compressed air. Tangential material inlet with trumpet air outlet The ideal solution for fine or dusty materials. If the materials that you need to convey have a small granule size, are very dusty, or contain angel-hair, then the METRO G loaders can be supplied with a tangential material inlet. During conveying this produces a cyclone effect which is perfect for separating different types of materials. With the trumpet air outlet, the exhaust air speed is well below the levitation speed so that no granules or particles can be carried back to the central dust filter. Membrane implosion vacuum valve No compressed air required and guaranteed contamination free. The membrane implosion vacuum valve offers the same functions as the implosion vacuum valve but works without compressed air. Instead, the vacuum required for the switching process comes from the conveying system, which opens and closes the valve. This valve is therefore ideally suited for use in clean room applications.
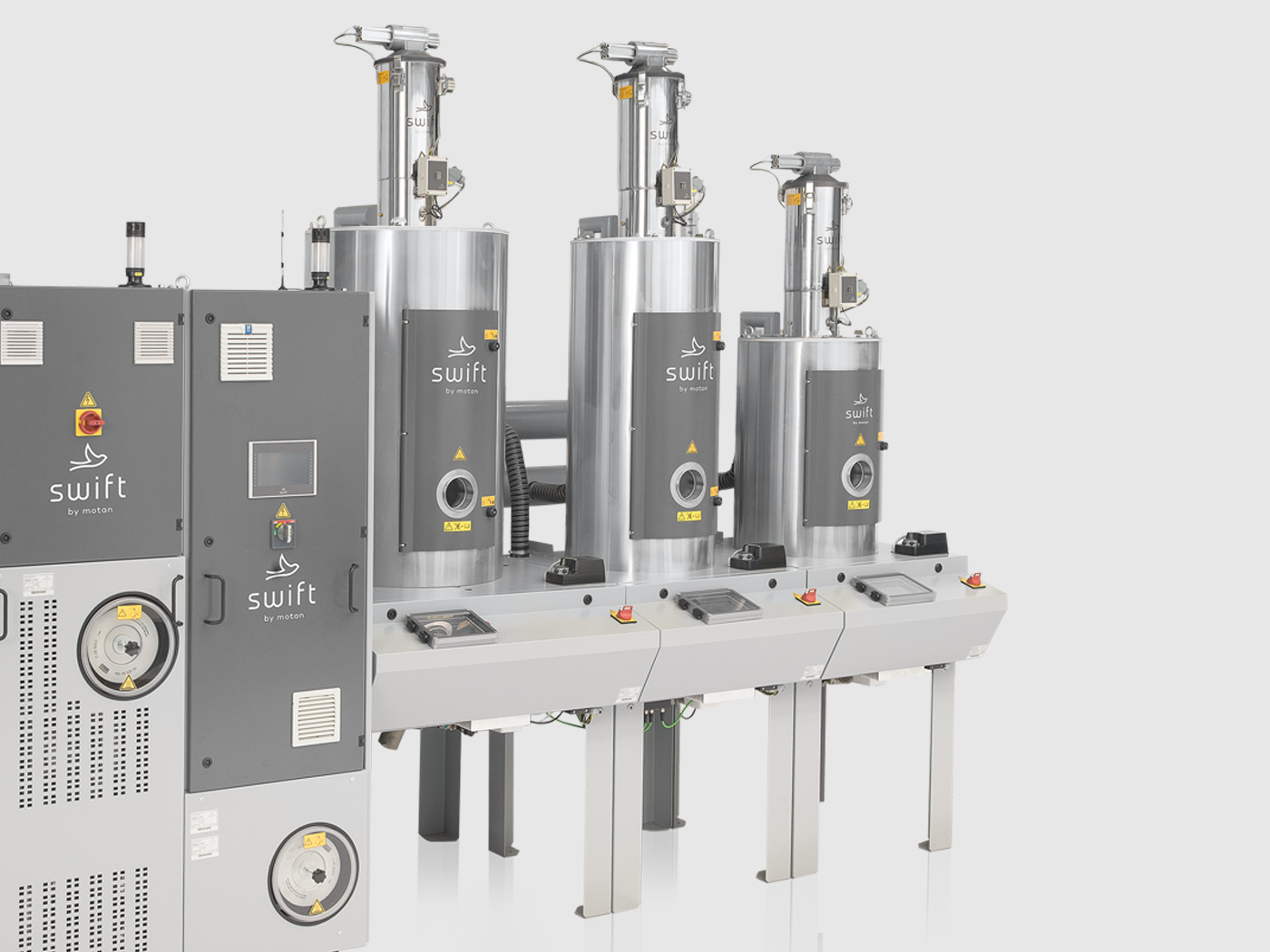
The sDRY MM / MD dryer series offers a fully modular drying management system. The system consists of one sDRY MM main module and can be flexibly combined with up to twelve sDRY MD drying modules. Each drying module can be operated independently and can be expanded or reduced at any time by adding further sDRY MD modules. The system can therefore be adapted to current production requirements by freely combining and arranging the drying modules. It offers maximum flexibility without interrupting the production process. The series consists of one sDRY MM main module. This can be supplemented with up to twelve sDRY MD drying modules. Drying capacities from 900 to 5400 m³/h can be achieved. This drying can be combined with a wide range of sDRYBIN A drying bins from 15 to 2400 litres. The sDRYBIN A drying bins are equipped with an intelligent and independent control system. The series consists of drying bins with a volume from 15 to 2400 litres. This series can be flexibly combined with the sDRY MM / MD drying system, which can be flexibly extended or reduced at any time with additional drying bins.
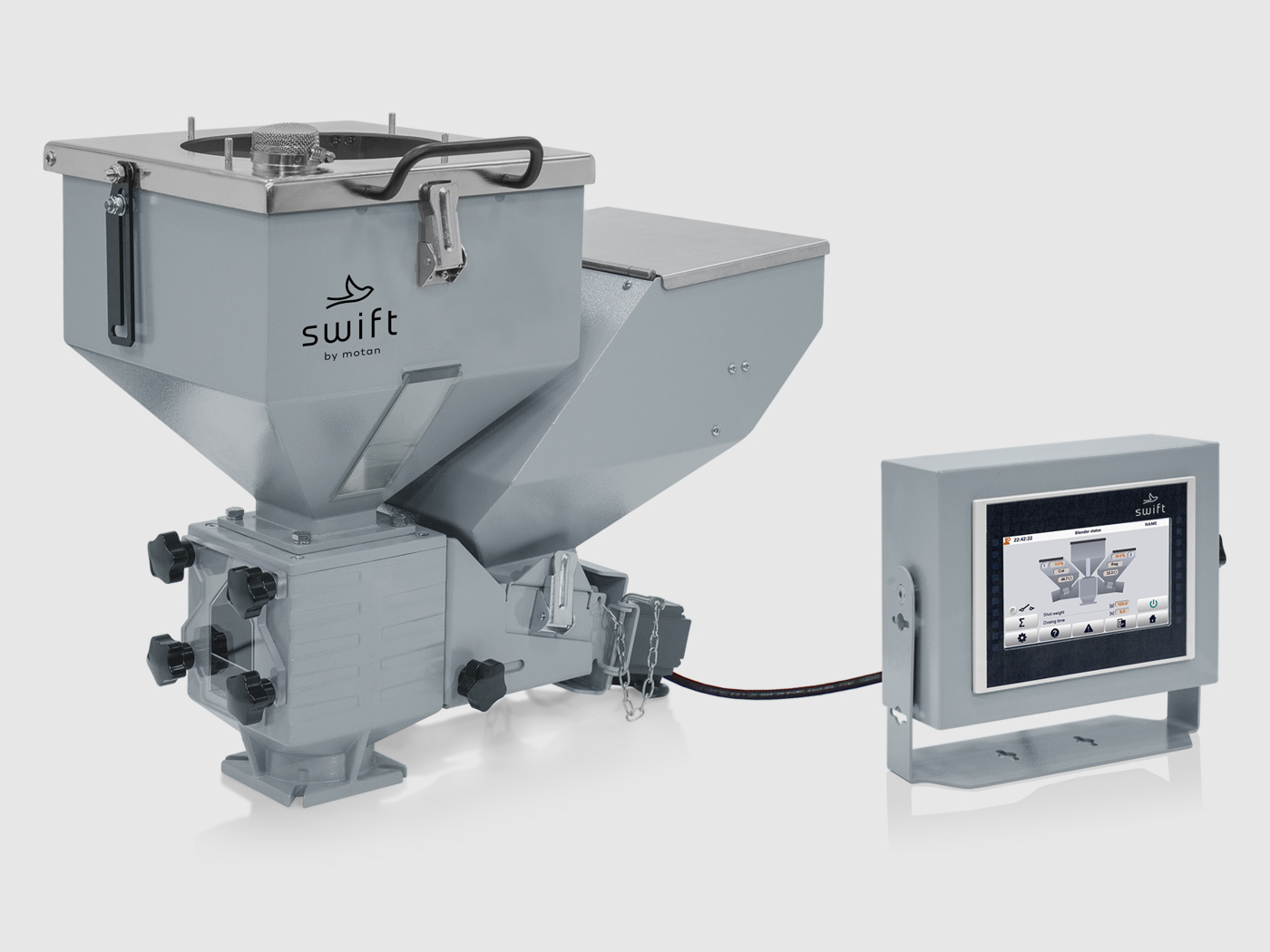
Combining additives with the virgin material at the processing machine requires excellent mixing quality and consistently accurate dosing. These requirements can be achieved and exceeded with the volumetric sCOLOR V dosing and mixing unit. The units are mounted at the feed throat of the plastics processing machine and are space-saving. Simple calibration No material spillage during calibration. By loosening two star-grips, you can easily withdraw the dosing module in order to collect and weigh the additive sample during calibration. This means you save time and there is no material spillage. sCOLOR control Intuitive colour graphic display with touch screen for easy operation of sCOLOR V. The modern microprocessor control comes with 16 user interface languages. It is suitable for one or two dosing modules and has a user-friendly additive calibration wizard. The regrind compensation function ensures that only the necessary masterbatch is dosed.
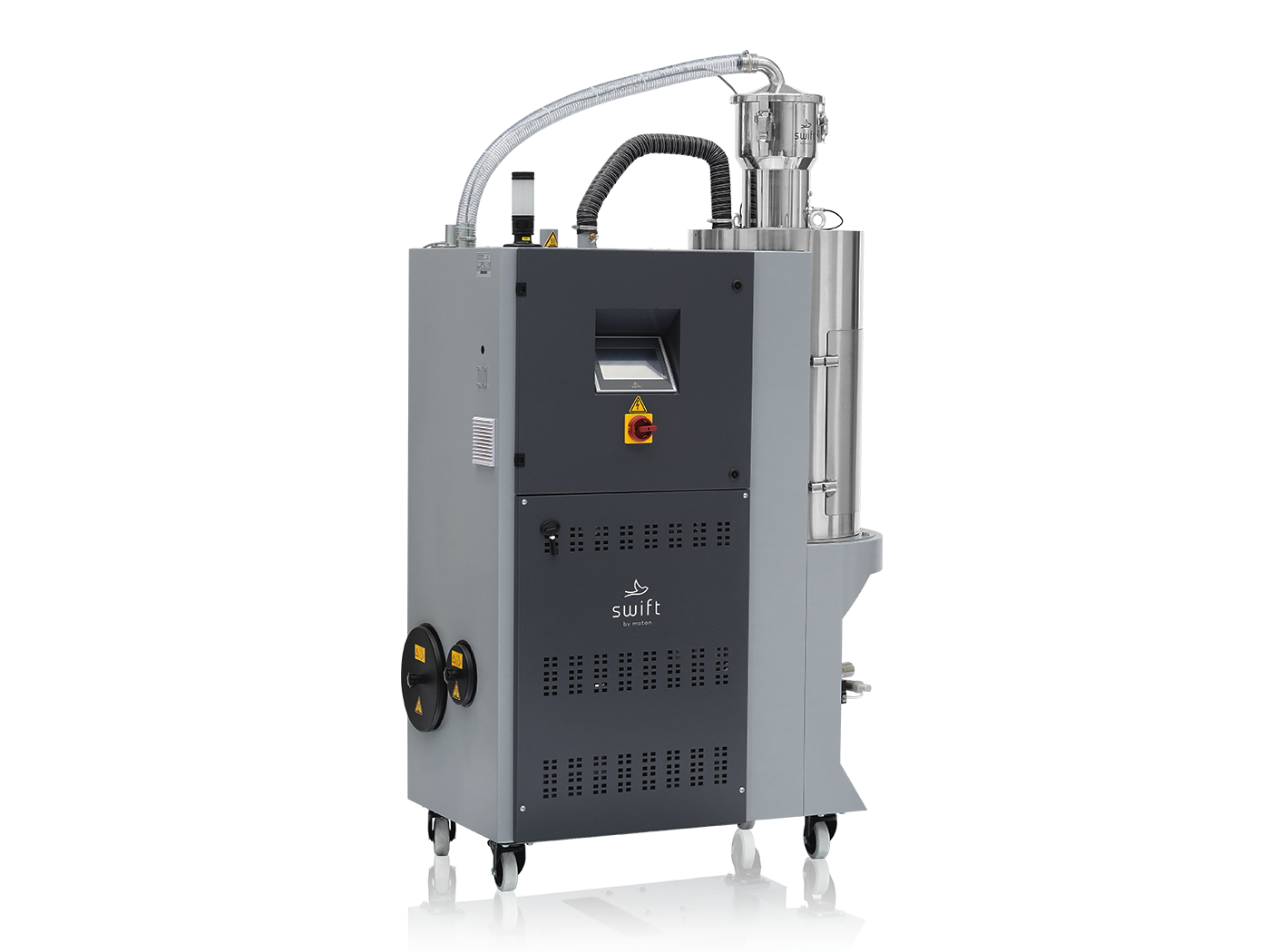
The sCOMPACT dryers are designed with flexibility in mind. The compact dryers offer an integrated solution, combining the drying and conveying of the raw material in one unit. The dryers are available in three versions, each with a drying bin of the size 80, 150 or 250 litres and up to three hopper loaders for conveying to the drying bin and two processing machines. As standard, this compact dryer is equipped with dew point control, overdry protection and dry air conveying function with line purging. Thanks to a modern 7 touch screen colour display, all conveying and drying functions can be shown and monitored in a user-friendly way. 16 user languages can easily be selected. Dew point display and control Optimised regeneration time saves energy. The sCOMPACT version of the dryer, offers dew point display and dew point control as standard. Regeneration of the molecular sieve is triggered when the maximum dew point set value of the return air has been reached. This value can be defined and set by the user and offers large energy savings. Overdry protection Protects material and saves energy. The standard automatic overdry function prevents material from being over dried. This reduces the heating capacity of the drying bin if the process return air temperature remains high for a long period of time. This function can be either enabled or disable dependant on your process requirements. Integrated conveying 3-in-1 drying technology saves space. The integrated conveying function in the sCOMPACT saves you space and money as no separate conveying system is needed. It can control one drying bin hopper loader as well as the hopper loader on up to two processing machines including the blower and filter. Dry air conveying & line purging Maintaining material temperature and eliminating reabsorption of moisture. The sCOMPACT A version offers dry air conveying and line purging as standard. This is essential for hygroscopic materials which reabsorb moisture quickly. Conveying is carried out in a closed loop and dry, warm air is used for transporting the material to the processing machine. After every conveying cycle the material feedline is purge. So, maintaining material temperature and eliminating reabsorption of moisture.
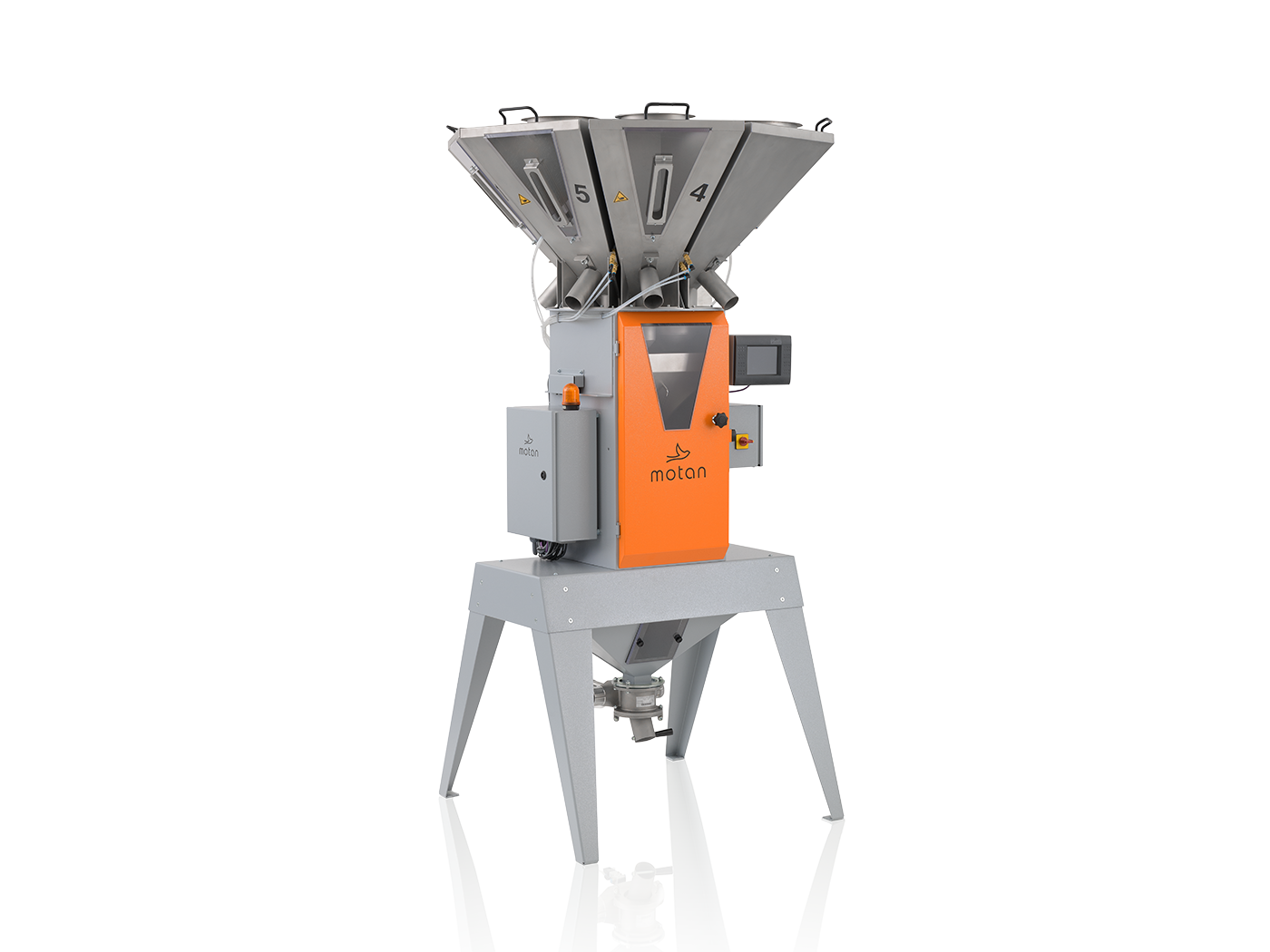
The GRAVICOLOR 310 and 610 dose and mix up to eight different materials precisely and with maximum recipe accuracy thanks to the unique motan cone dosing system. The modular design and excellent engineering guarantee optimum performance, flexibility, and reliability of the units. This gravimetric batch dosing and mixing unit can be used for injection moulding, blow moulding and extrusion processes. The integrated and improved IntelliBlend analysis function records the recipe, material and operating environment and documents all process data. With the help of the software, the user achieves continuous self-optimisation of the system and consequently the best possible operating point with the highest recipe integrity and consistent, high product quality.
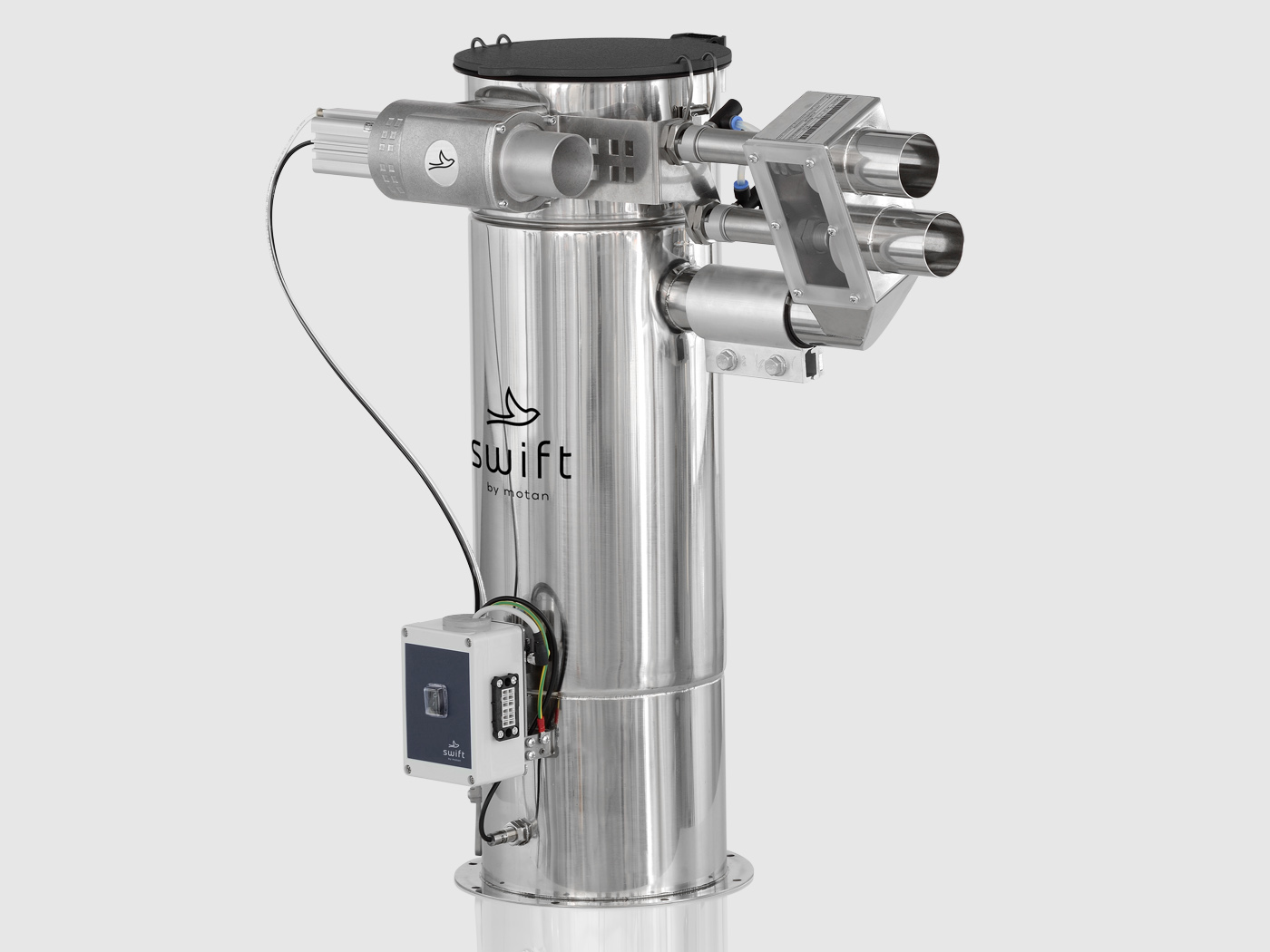
Cost-effective and efficient material conveying can be realized with sCONVEY HOS material loaders. This improves the overall process management of your system. The plastic granules are transported quickly and cleanly into hoppers, drying bin or other dosing and mixing units and fed to the machine as required. This eliminates material wastage and keeps the work-space clean and safe. sCONMIX proportioning valve Accurate and reliable addition and mixing of regrind and virgin materials. The polished stainless steel sCONMIX proportioning valve can be connected to the sCONVEY HOS material loaders. You can easily adjust the percentage and number of material layers per conveying cycle. A large transparent access panel gives you easy access for cleaning. Machine loader Perfect for hygroscopic materials and where space is limited. When conveying hygroscopic materials with small throughputs or where space is limited a machine loader version is available. The unit must be mounted directly on the feed throat of the processing machine. Integrated into the loader is a discharge flap which ensures a stable conveying and eliminates material being pulled during conveying from the processing screw of the moulding machine. Your benefit is that no machine supply hopper is required, and very little material is stored at the machine. This is especially important for dried materials as the holding time of the material is kept to an absolute minimum.
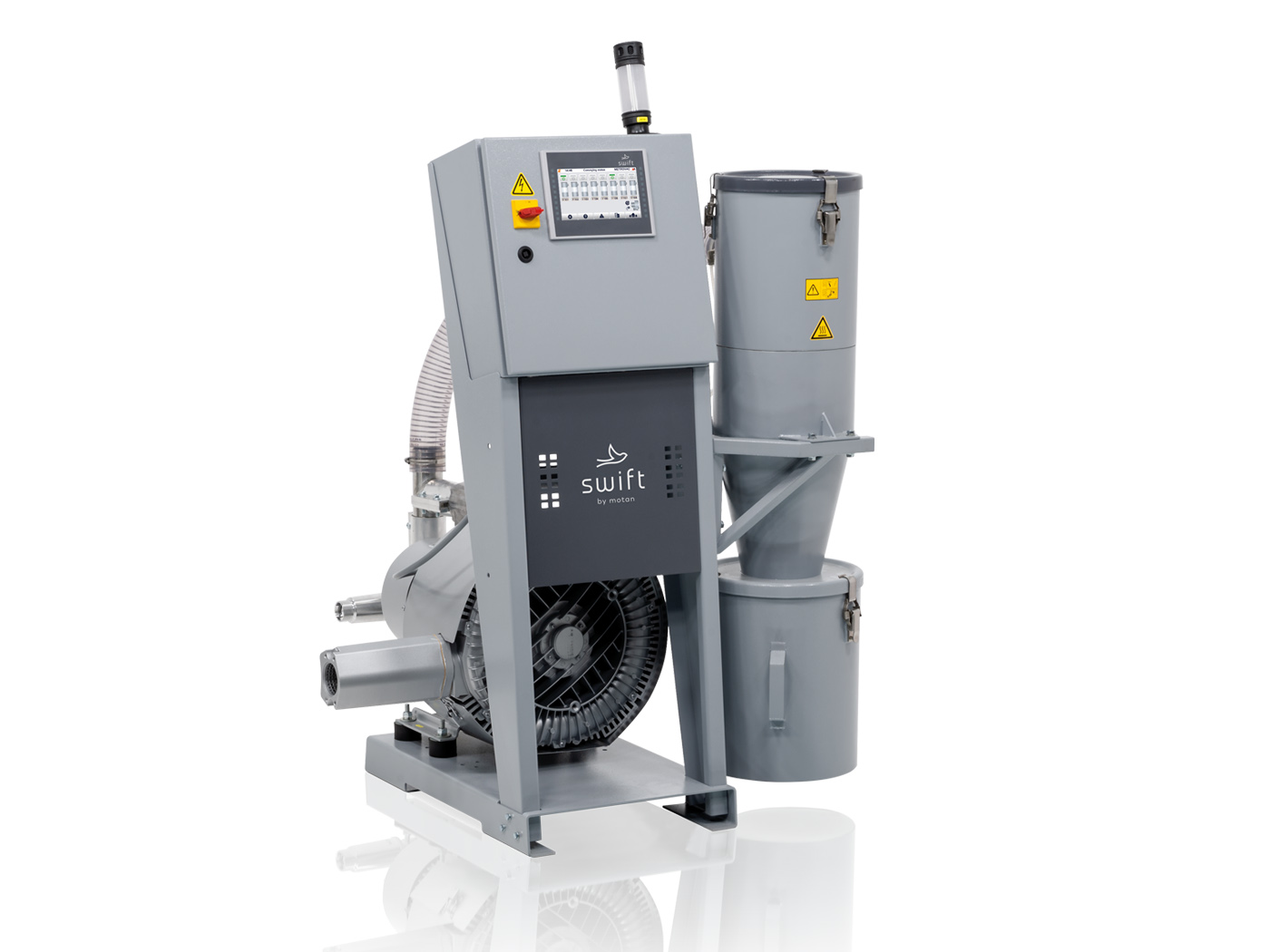
With the sCONVAC flexible conveying station, small conveying systems can be operated cost-effectively. The three-phase conveying station can be used for a wide range of central conveying applications with a large choice of blower sizes. The three-phase blower is low-noise and maintenance-free. The station is available with a blower protection filter or optionally a cyclone dust filter with collection bin. The integrated sCONVAC control is equipped with a 7 colour display which can operate up to 12 sCONVEY HOS material loaders and up to 8 purging valves. Cyclone dust filter / the blower protection filter The central dust collection with two options : The sCONVAC conveying stations are either equipped with an efficient CF7 cyclone dust filter unit or a BPF6 blower protection filter. The CF7 filter combines cyclone dust collection with a fine dust filter. The dust collection bin makes removal of accumulated dust quick and easy. Line Purging Perfectly conditioned material always in the right place. Purging and cleaning of the material feed lines is possible after each conveying cycle. This is essential when conveying hygroscopic materials and for fast material changes. It also prevents conveying lines with long, vertical sections plugging up. The sCONVAC conveying station can control up to 8 purging valves or suction boxes with integrated line purging.
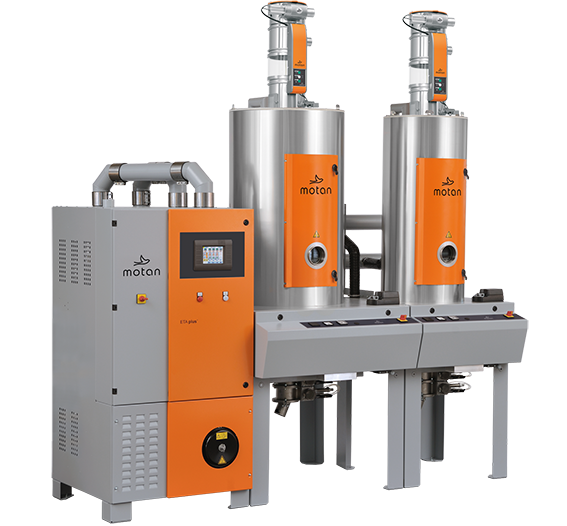
LUXOR A series dryers with ETA-process® and ETA plus® energy saving technology are specifically designed for supplying dried plastic granulate for many different plastics processing applications. They have either two or three fully insulated stationary desiccant beds with separate process and regeneration blowers which provide consistently low dew-point air to the process, while reducing energy consumption. The advanced LUXOR A series consists of ten models with drying capacities from 80 to 2400 m3/h. Each advanced system dryer can be flexibly combined with all LUXORBIN A drying bins from 15 to 2400 litres. In addition, motan offers a range of extra-large drying bins with volumes from 3,000 to 13,000 litres. These are also available with gas heating. All motan system drying bins are made of stainless steel, are completely insulated, and have individual heating as well as temperature control. All LUXOR A drying systems have a LUXORnet control and utilise modern, flexible Bus-technology. As standard, LUXORnet manages the dry air generator, 16 drying bins, and up to 24 machine hopper loaders. The integration of dry-air conveying, line purging, as well as manual and automatic manifold stations provide maximum flexibility and productivity.

motan s material selection stations assure that every desired connection of a material to a processing machine in your production process can be made quickly and reliably without contamination. Fixed pipe connections throughout the whole production process until the next material change ensures maximum security.
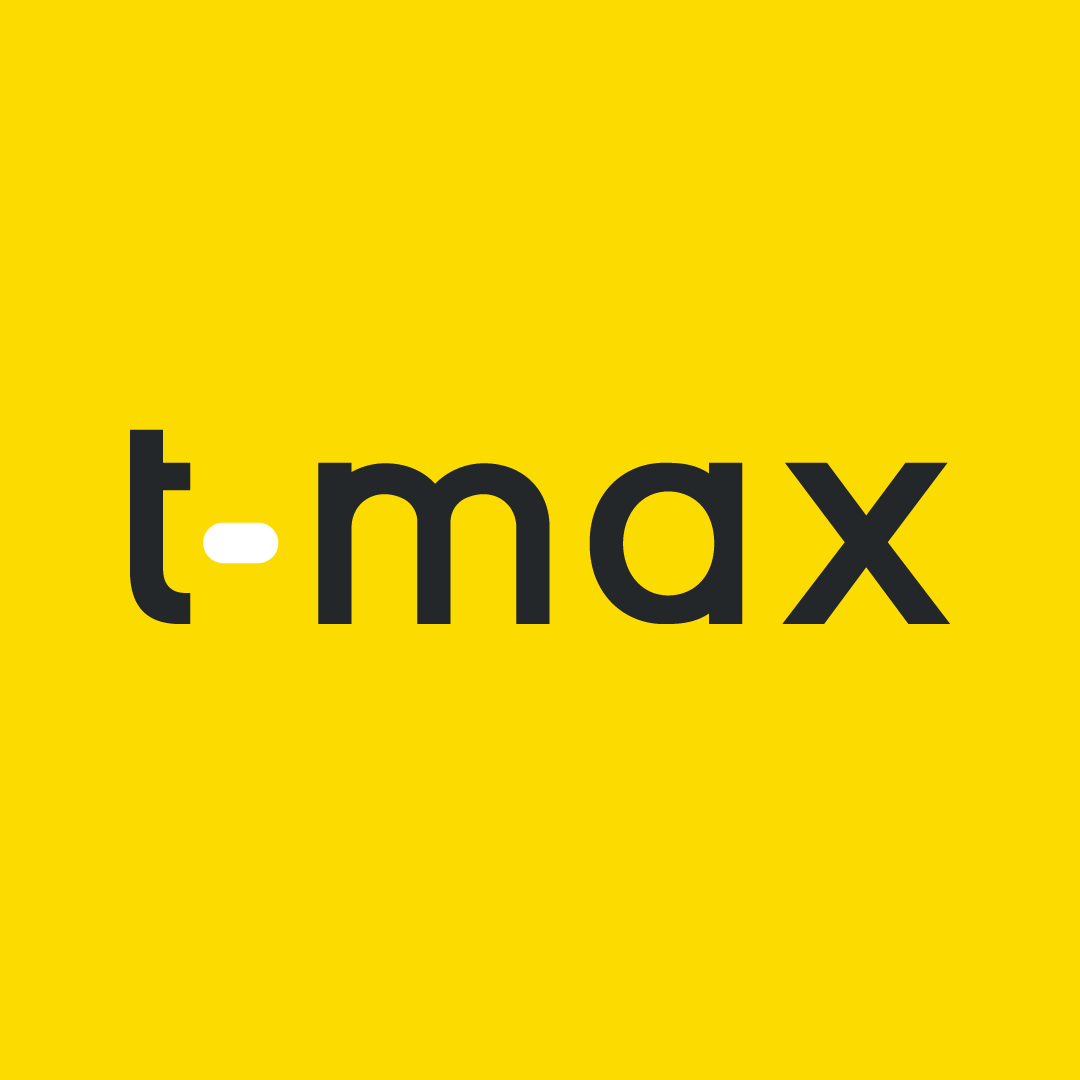

- GRAVICOLOR
- SCOLOR V
- SBLEND G
- LUXOR
- SDRY
- SDRYBIN
- METRO
- METROLINK
- SCONVEY
- SCONVAC