Company Name | Contact Info | Location | ||||||||||||
---|---|---|---|---|---|---|---|---|---|---|---|---|---|---|
NOKTA PLASTİK TEK. SAN. VE TİC. LTD ŞTİ.
Çerkeşli OSB Mahallesi İmes 9. Cadde No: 26 / DİLOVASI / KOCAELİ / TÜRKİYE
|
Contact Info: +90 530 472 5541
|
Hall: 11A
Stand: 11A-136A
|
||||||||||||
Product Groups | ||||||||||||||
|
- Company Info
- Products
- Represented Companies
- Company Brands
Founded in 2001 by experienced engineers in the plastics industry, our company always introduces new technologies to companies in the sector and offers them more efficient working opportunities. By providing the necessary machinery, automation systems and accessories that we call side equipment for the plastics industry, it serves consumers with plastic injection machines, rubber injection machines and equipment in the plastic and rubber industry. Our company, which adopts customer satisfaction as a principle, has been with its customers since its establishment with its sales and service team. As a company, our aim is to increase the productivity of the companies in the sector and to ensure higher profits. For this purpose, we carefully select the companies we work with. Working with companies that are open to new technologies, can renew themselves and produce new technologies allows us and our customers to be at the forefront. Considering that the most important problem of the world today is energy, it is certain that the plastics industry will also be affected by this, considering that energy can rise every day. For this reason, innovations in plastic machinery have focused on efficiency and savings. Class A machines have started to take their place in the sector. Nokta Plastic Technologies San. And Tic. Ltd. Şti., it is our most important principle to always offer the right and efficient investments to the service of our industrialists.
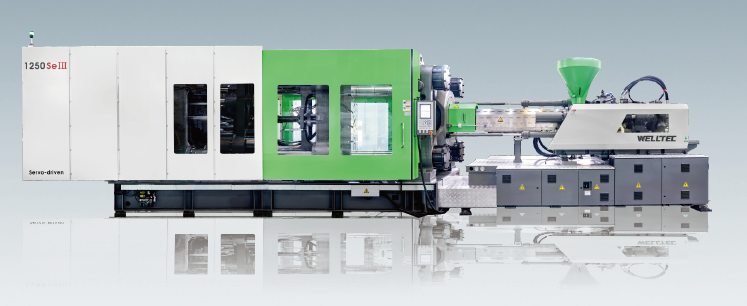
Our SEIII series machines have double close-loop control system. Excellent Energy Saving The newly developed SEIII series energy-saving injection molding machine is the integration of advanced servo-drive pump system and our 35 years of experience in injection molding machine production. Compared with the standard machine, you can save 25-85% energy. This percentage range varies especially depending on the ironing and cooling time. Energy savings reach the maximum percentage in cycles with high cooling and ironing times. Fast Response High Efficiency With the quick response feature of the servo motor, the motor can accelerate from stationary to 1500 rpm in as little as 40 ms. This increases the speed of the hydraulic system and reduces the ironing and injection time. Thus, the production quantity is increased. Printing Accuracy The use of the servo hydraulic system has minimized the weight differences in successive prints. Printing accuracy in consecutive cycles is around 0.3%. Low - Speed Stability The system pressure and speed show excellent performance in a closed circuit controlled low pressure and low speed operating environment. Even when the injection speed is below 1 mm/s, there is no jitter or stuttering and high stability. The system allows the freedom to change the speed and pressure settings as desired according to the mold in order to avoid extra heating of the hydraulic oil, which can be destabilizing as in conventional machines. In addition, the system automatically compensates for pressure and flow losses, ensuring stability, precise control and high repeatability.
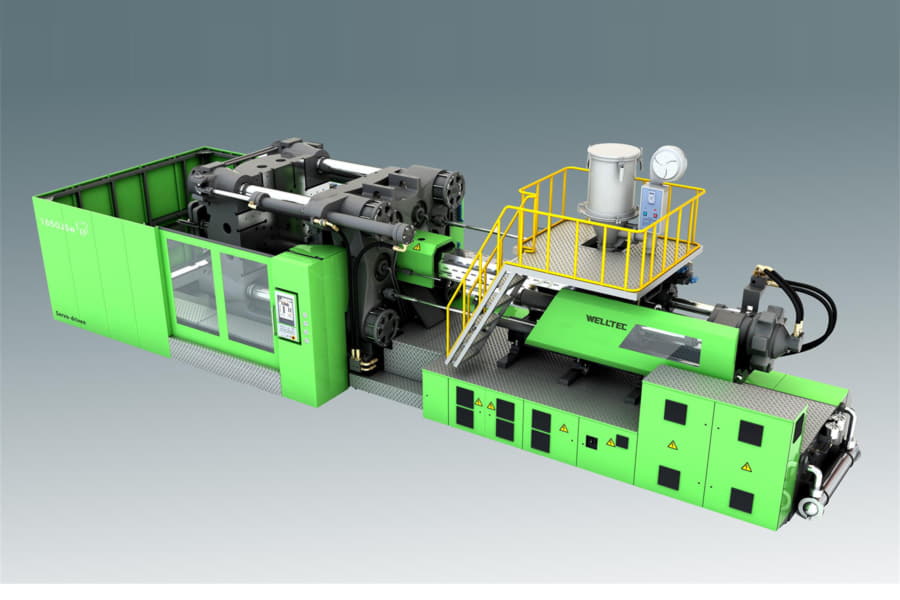
In addition to the 50-80% energy savings, each model of machine has a three-phase digital electricity meter and you can see your hourly consumption on the display. Continuously printing the same weight, i.e. the deviation in repeatability is around 0.4%. The cooling system required is half as much as for normal machines. Average (30-40% less) The amount of hydraulic oil needed for normal machines is 30% less for our JSEII series machines. So you will pay less money in installation. You will also save money on periodic oil changes. It is 10% faster than normal machines, so the amount of product produced increases with the number of cycles. With the flash memory in our machines, as many molds as desired can be memorized and copies can be made from one machine to another machine. In our machines, it is possible to monitor production for control purposes with remote access devices such as computer, ipad and iphone etc. (changes cannot be made, only monitored). With the multi-level password feature, authorized and unauthorized personnel can limit what they can do on the machine. Our JSEII series machines have a double close-loop control system. Faster cycle time with high speed mold movement Repeatability in mold opening position 1mm Synchronized movement structure with locking nut, no effect on the injection unit. It provides precise and smooth operation with its linear slide structure. Injection grammage repeatability 0.3 Wide inter-column distance, long mold height and long mold opening stroke. Stable production even at very low speeds with AC servo motor. Superior product repeatability, even at very low speeds and long ironing pressures.
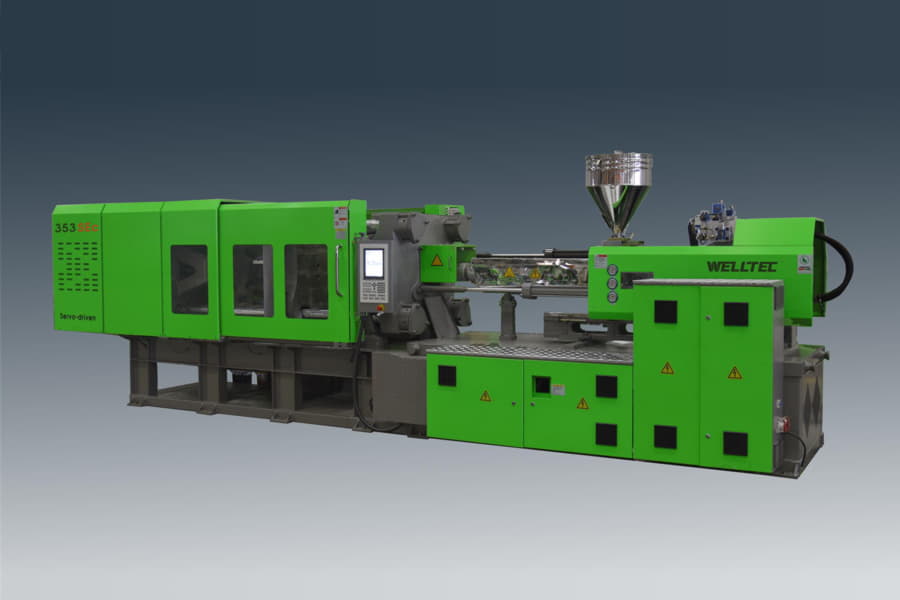
In addition to the 50-80% energy savings, each model of machine has a three-phase digital electricity meter and you can see your hourly consumption on the display. Continuously printing the same weight, i.e. the deviation in repeatability is around 0.4%. The cooling system required is half as much as for normal machines. Average (30-40% less) The amount of hydraulic oil needed for normal machines is 30% less in our SEc series machines. So you will pay less money in installation. You will also save money on periodic oil changes. It is 10% faster than normal machines, so the amount of product produced increases with the number of cycles. With the flash memory in our machines, as many molds as desired can be memorized and copies can be made from one machine to another machine. In our machines, it is possible to monitor production for control purposes with remote access devices such as computer, ipad and iphone etc. (changes cannot be made, only monitored). With the multi-level password feature, authorized and unauthorized personnel can limit what they can do on the machine. Our SEc series machines have a double close-loop control system. Optimal design to reduce the impact force when opening and closing the vise and provide high speed mobility. High speed super production and perfect products with precise and energy-saving servo machine. Injection speed is higher than 200mm/s, screw speed is higher than 850mm/s. Opening and closing mold speed can reach 500mm/s. Linear ruler precision in mold closing, clamp movements and energy consumption, with stable running and faster response, Wide inter-column distance to allow more large molds to fit and operate, High performance goods receiving with chrome plated screw. Faster heating and heat loss prevention with ceramic heating element. Speed and pressure control with closed circuit control system, superior product repeatability. B&R Control system is the most professional control system used in injection molding machine. 10.4 TFT color LCD display, Thanks to the advanced parameter memory, you can see in detail which user has changed which values. Thanks to statistical and graphical process data, you can see how good the stability of the machine is. Auto-tune feature allows you to adjust the temperature PID calibration very easily. You can save mold data to your USB stick and copy it to other injection molding machines. You can monitor the screen of the machine remotely via ethernet connection from your modem. With the multi-language option, you can access the desired screen in different languages.
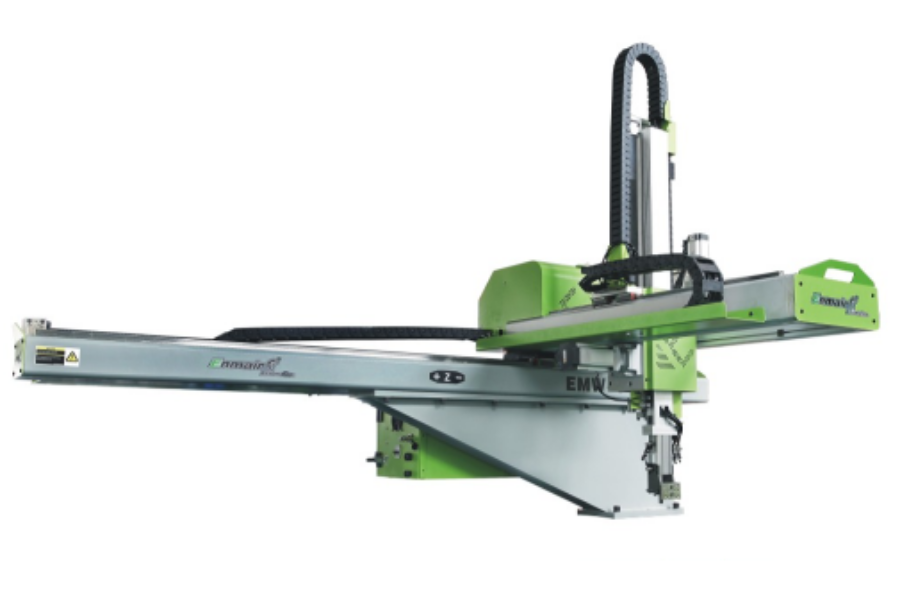
EMW Series robots can easily operate in plastic injection molding machines between 200 tons and 1600 tons. There are single arm and double arm models. In this series, the Z axis has a telescopic structure. We recommend working with this type of robots in places with height problems. Robot automation system adds speed to production and reduces the cost rates in production to a certain extent. The connection system to plastic injection molding machines is made using Euromap-12 and Euromap-67. It can also easily adapt to Far Eastern sockets in Far Eastern origin machines. The control panel provides ease of use with its convenient interface and touch screen. It provides convenience in copying and uploading programs with USB Interface connection. Enmair Robots are under warranty and service by Nokta Plastic Technologies with years of experience. With the faulty product separation feature, it separates faulty products with the injection machine interface. Multi-language option can be activated and used by the user. With the tracking function feature, you can set the pusher values in the actual position in the injection molding machine to prevent damage to the robot arm in the mold. With the product pick-up control feature, it is used to make arm movement in a suitable position. With the product stacking feature, it can stack products according to the actual need. With the arm descent delay feature, it is used to shorten and adjust the product removal time by waiting in the vertical arm. It can leave the runner at any point on the traverse axis. With the mold s range of motion feature, the robot can move freely in the mold to pick up the product. Buzzer feature activates when the robot alarms. Optionally, if standard I/O is not enough, additional input and output points are available. Optionally, it is possible to make multi-axis, more functional movements and increase tolerance by selecting RV reducer and servo motor. With the gripper rotation function, you can rotate the gripper outside and inside the mold area.
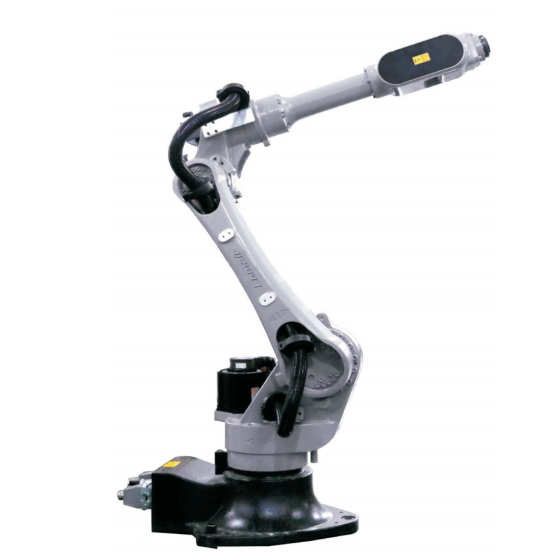
No product info found.
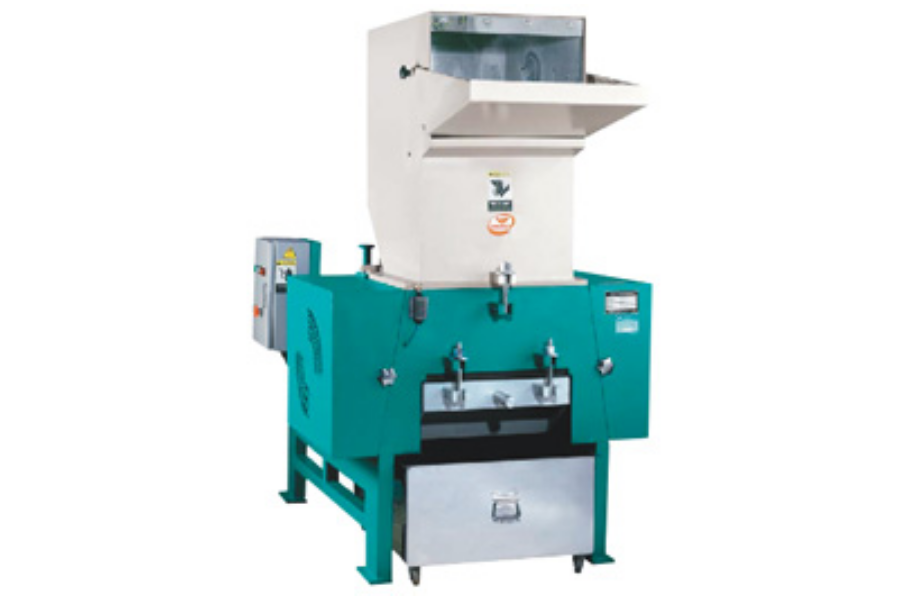
Strong construction with the use of impact resistant materials, Easy blade adjustment and replacement with top opening crushing blade, Easy sieve and machine cleaning with bottom opening body cover, The raw material hopper is stainless and wheeled, easy to clean and transport, Low vibration operation with rubber chocks, Noiseless operation with sound insulation, The control panel is on its own and complies with safety specifications, Material loss is prevented with crushing mouth design and screens.
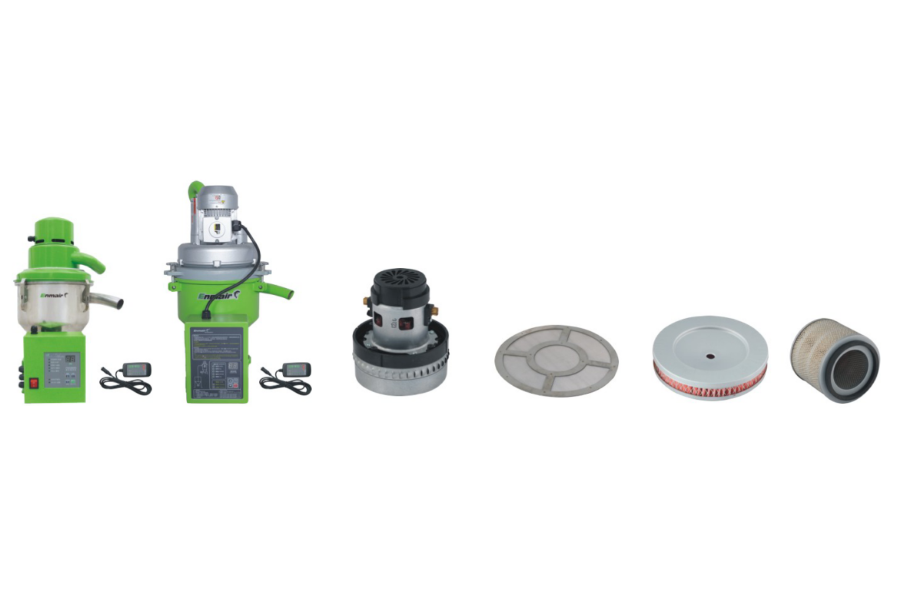
Simple Operation System Easy installation, simple and stable operation, long distance transportation capacity. Excellent Design. Open structure with special design, maintenance-free fan design, easy modification and working status display, alarm due to material shortage or malfunction, this alarm will alert the user with flash light alarm instead of buzzer. High Efficiency Operations It quickly transfers the material in the hopper to the dryer. The material is sent to the designated location on time and continuously without interrupting the production process. Stable Control System The loader with microprocessor control system provides precise operation control. There is illuminated LED on the interface. There is microprocessor memory EEPROM. Easy and Clean Maintenance Easy cleaning with independent filter Dust is reduced thanks to the high-power fan.
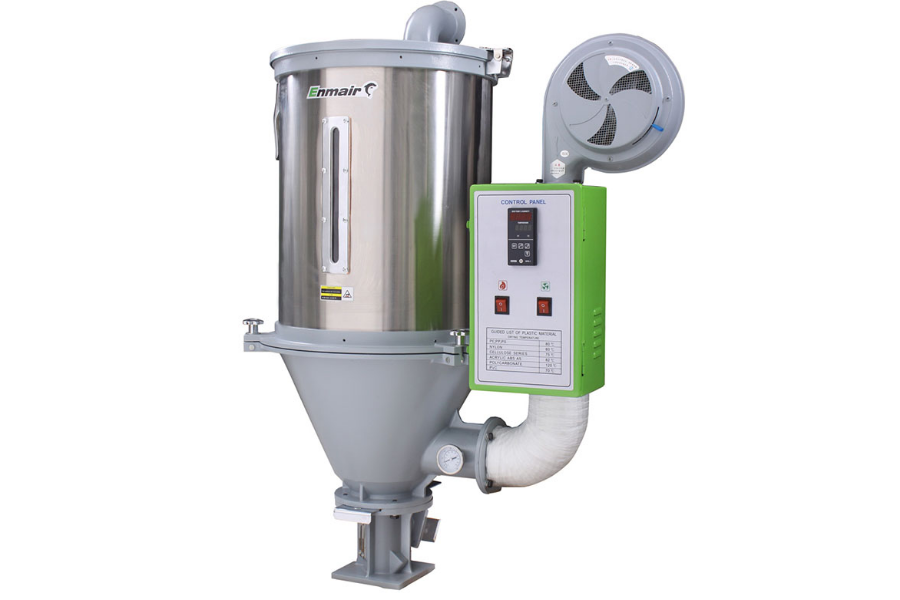
Our raw material dryers, which provide great convenience in terms of use and maintenance, perform a precise drying with its inner surface made of stainless steel. Stainless steel joint parts Precision aluminum rotor, smooth surface and superior performance that perfectly maintains the heat-setting process. Low noise air blower and optional installed air filter. Material tank with glazed sides. Curved heating cylinder designed to prevent dust formation. Thermostat indicator with proportional deviation designed to control the temperature setting. High temperature option for 50E-1500E with double walled hopper tank, stainless steel heating tube and high temperature air blower. Stainless steel baffle & tone separators. Smooth surface & body easy to maintain and clean.
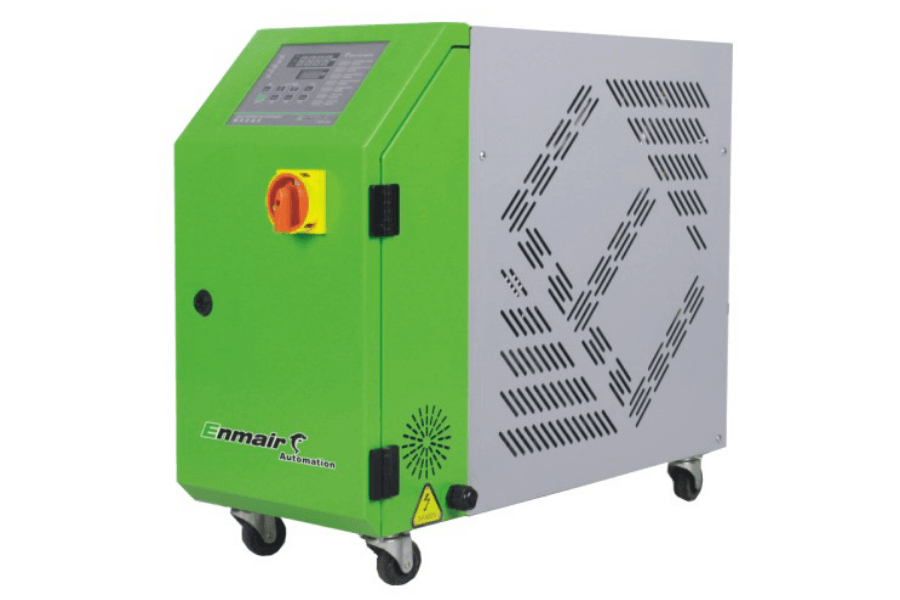
Models are available with operating temperatures of 120°C, 160°C or 180°C. Automatic air discharge function when the machine is running Automatic stop function in case of over-temperature Low and high pressure protection function Fast cooling function European standard design with explosion protection, High efficiency energy-saving pump Smart time switch design, By-pass pressure relief circuit function, Improved PID to keep the temperature constant within ±0.5℃ for a long time, high efficiency and energy saving. Six alarms are available: thermocouple open circuit alarm, phase failure, pump failure, overheating and oil leakage alarm. Dual digital display shows actual and set temperatures. Very easy to use and maintain. Stainless steel tank has no leakage, durable and anti-corrosive. Elegant appearance and small size.
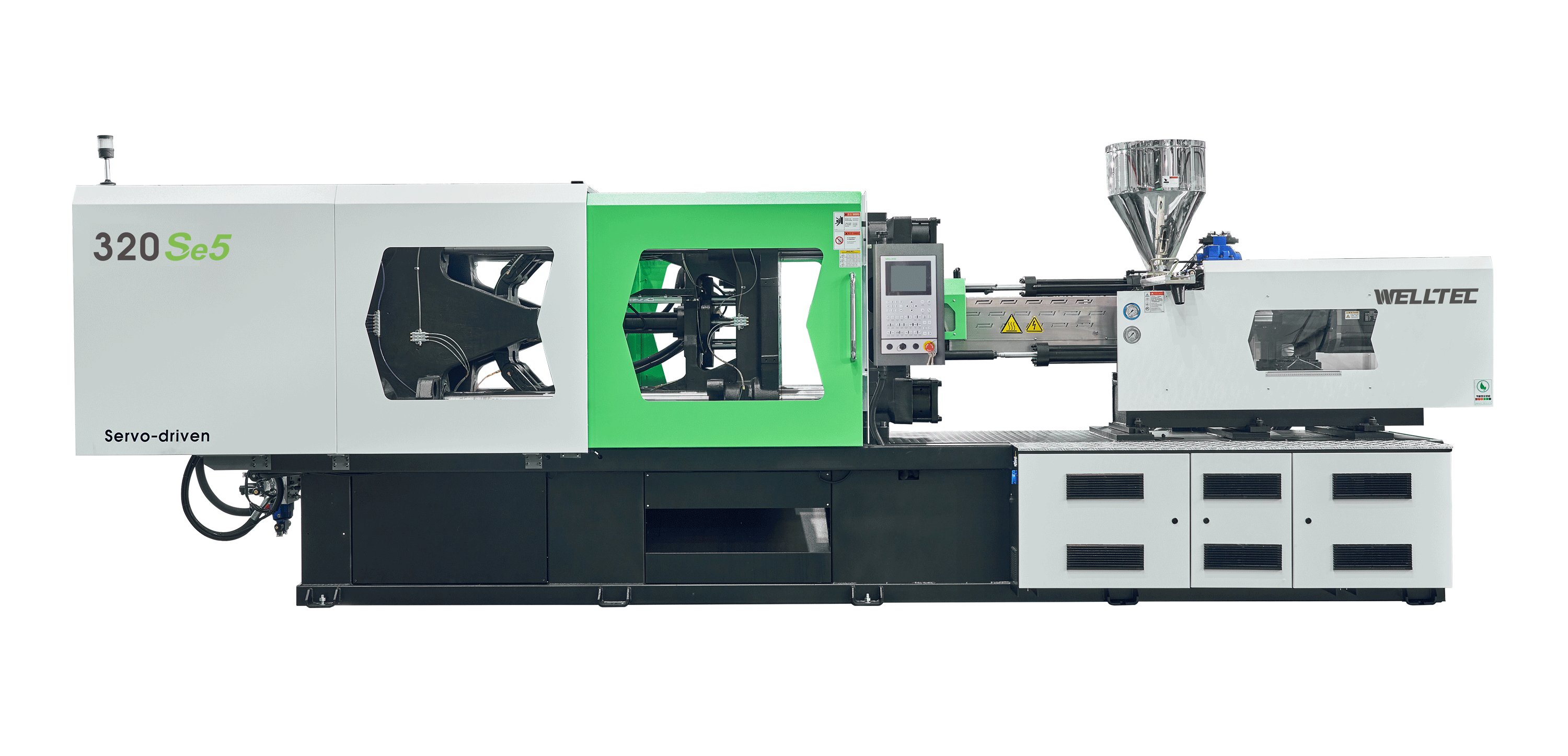
Ergonomically optimized design for the clamping unit to be durable and meet the requirements of high-density production. The optimized hinge movement is extremely smooth and the final position of the mold opening has high repeatability and accuracy. New injection unit design with better performance to meet higher processing requirements for various products. Equipped with electric plasticizing as standard, the plasticizing capacity is increased by 20%-45%. The speed of different models has been increased by 15%-25% to shorten the molding cycle and improve production efficiency. Energy consumption of the whole machine has been reduced by 20%. New optimized hydraulic pipeline design to minimize energy consumption loss, prevent oil temperature rise and reduce cooling water consumption.


The company has no registered brand information.