Company Name | Contact Info | Location | ||||||||||||
---|---|---|---|---|---|---|---|---|---|---|---|---|---|---|
PİOVAN MÜHENDİSLİK LTD. ŞTİ.
Kavacık Mah. Hülagü Cad. No: 15 34810 / Beykoz / İSTANBUL / TÜRKİYE
|
Contact Info: +90 216 331 4401
|
Hall: 8
Stand: 820
|
||||||||||||
Product Groups | ||||||||||||||
|
- Company Info
- Products
- Represented Companies
- Company Brands
Piovan Mühendislik is own office of Piovan SpA in Turkey. We provide sales and after sales service of auxiliary equipments for Turkish plastic sector. Piovan s range of auxiliary equipment able to satisfy all requirements in the various industry sectors PET preforms & bottles, rigid packaging, automotive components, technical parts, medical solutions, thermoforming & technical sheets, flexible film, pipes, profiles, cables, fibres & strapping, recycling & compounds with high engineering skills. Our product ranges; Single or central drying and feeding systems, Volumetric or gravimetric dosing systems, Granulator and schredders, Chiller and free cooler systems, Thermoregulators, Mould dryers, Full automation systems for PET material, Crystallisation systems for PET material, Outdoor or Indoor silos for raw material and silo feeding systems Mixers, Big-Bag unloading system, Automatic bag opening machine, Instruments for preforms, Solution for on-line moisture measurement and portable dew point meter, Monitoring and management software-hardware systems for all auxiliary equipments (Winfactory 4.0), Conveying and de-dusting system, Complete turn-key food production systems Piovan group companies; Una-Dyn Auxiliary equipments for US plastic market, Fdm Dosing and feeding systems for granule, recycle and powder materials, Aquatech Chiller and free cooler systems, Penta Silo, silo conveying and feeding systems for plastic and food industries, Energys Monitoring and management of energy systems, Progema Automation systems, Fea Conveying and storage system for food industry, Doteco Gravimetric Dosing system for extrusion lines Conair Auxiliary equipments for plastic market, Thermal Care Industrial chiller and process cooling systems, Pelletron Conveying and de-dusting systems, Our partners; MB Conveyor Conveyor systems, Local solutions Silo feeding, mixers, big bag unloading systems with crane or without crane and automatic bag opening machine. Piovan Mühendislik Ltd Şti. Address Kavacık Mahallesi Hülagü Cd. No15 Beykoz İstanbul/ Türkiye Tel +90 216 331 4401 e-posta info.tr@piovan.com
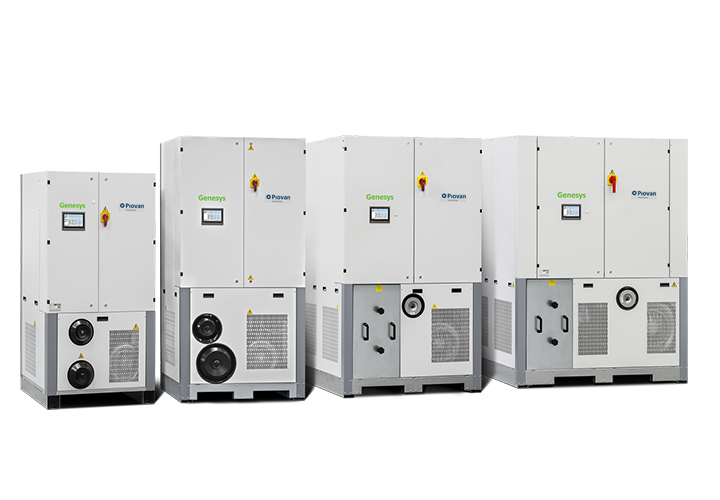
Genesys is a single-hopper, individual or central, fully automatic drying system. It can adapt and automatically control operating parameters based on ambient temperature, initial moisture level, type and quantity of polymer, the final moisture content of the polymer, and granule size. This innovative drying system adjusts and controls optimal operating settings for the material to be dried, using only the overall amount of energy strictly required. The settings are constantly compared with the data collected by the sensors installed on the system. A patented measuring unit, located in the air supply line, adjusts and controls the air flow instantaneously and independently. The airflow is modulated automatically by the drying unit, resulting in optimum process operating conditions. Configurations and features The Genesys range comes in 3 configurations SMART, PLUS and ADAPTIVE to meet diverse operating needs. A microprocessor, controlled by a Piovan proprietary software, provides electronic control. The operator s interface is an 7-inch, colour touch screen. The HMI offers access to all the system s components for specific adjustments or settings. Benefits ? Integral process variables control feature ? Full auto-adaptive operation ? Automatic air-flow adjust and stabilization ? Regeneration heat recovery system ? Different configurations to meet customer s need ? Winfactory 4.0 ready
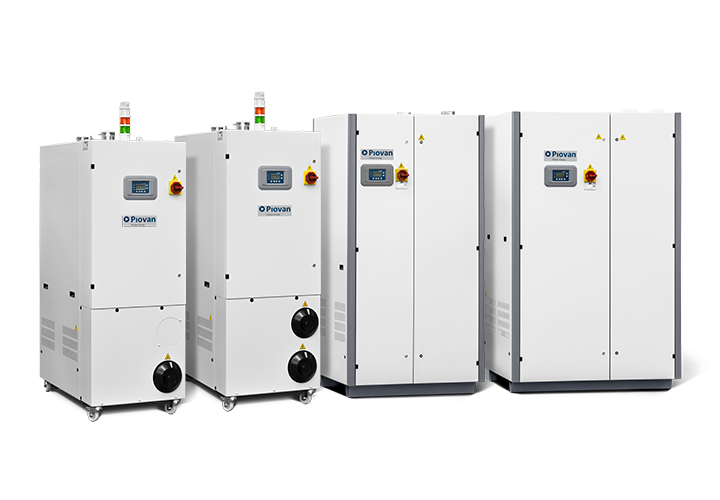
Double desiccant tower models, with an airflow rate from 200 to 800 m3/h, supply air at a dew point lower than 55°C. The process air temperature can be set up to 150°C (200°C for the HT version). CUSTOMER ORIENTED SOLUTIONS: Precision: Electronic control of the process temperature with self-tuning PID algorithm that ensures high precision. Easy utilisation: Simple and complete operator interface Microprocessor control Large display available in the operator s language. It shows the functioning status of the machine as well as any possible alarm or warning message On the main screen the following parameters of the dryer can be monitored: Drying temperature, Set-point, Dew Point value Flexible and modular configuration: The operator can simply and easily increase the number of hoppers at any time. Hoppers capacity from 300 to 2500 dm³; single or centralised systems Intelligent Energy Supervisor: In accordance with the effective requirements of the processing machine, the IES system optimises and adjusts the energy utilisation Intelligent Material Drying: optimises and adjusts the energy utilisation to prevent material thermal degradation or over-drying Benefits ? Single or Multi-hopper set up ? Temperature-control based regeneration cycle ? Dew Point Control ? Water Flow Control ? Automatic reduction of the process temperature ? Material consumption management ? Cooling stop ? Process airflow management ? Blowers and molecular sieves filtration system ? Solid state relays (SSR) ? Automatic set-up of the process air safety temperature ? Completely independent process air temperature safety control (temperature probe, power control and contactor) ? Warnings for the operation of the coolers (cooling water circulation only when necessary)
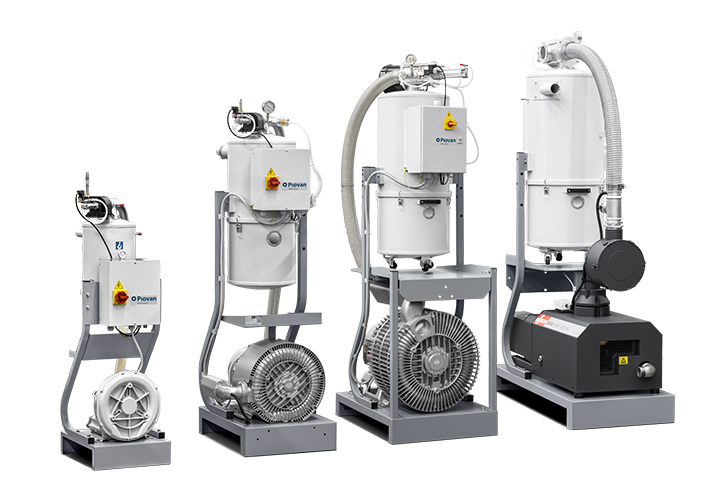
The F vacuum pumps, with a power ranging from 1.5 up to 11 kW, cover a production range of up to 1500 kg/h and a transport distance of 100 m maximum. The vacuum pumps can be equipped with the FZ cartridge filter or particularly compact and efficient filtering systems CF1, CF2 and CF3. The CF filter combines the cyclonic effect with dust separation and are recommended in the case particularly dusty materials are conveyed. Benefits ? Maintenance-free motors ? Noise level lower than 75 dB(A) ? High filtering efficiency ? Quick and simplified filter cleaning operations ? Vertical design solution requiring little floor space
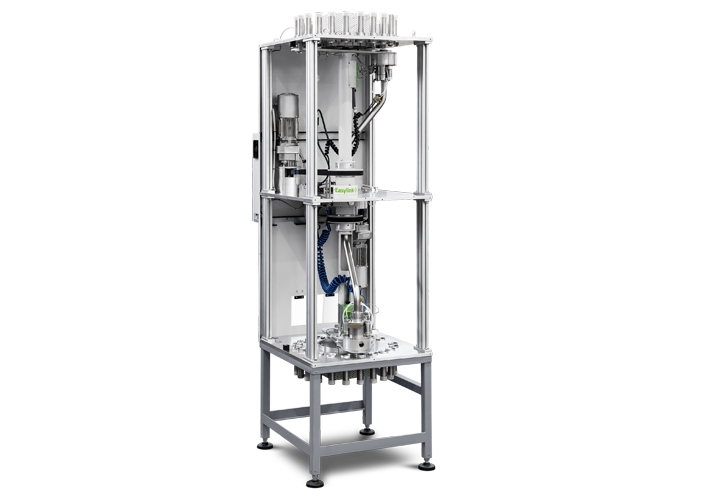
The new Easylink+ range has a state-of-the-art cleaning system integrated in the bottom inlet to guarantee perfect cleaning of the main arms and prevent contamination. The new main arms are manufactured with a special hardening treatment for even greater wear resistance. The floor space requirement is minimal even for the largest models with 60 inlets/outlets. Easylink+ has a compact, vertical design with moving parts inaccessible for optimal operator safety. In the case of applications where absence of contamination is critical, a slide gate can be installed on every outlet as a barrier against residual granules. Pneumatic fitting positions are encoder-controlled to ensure correct selection of the material source. The drives are equipped with inverters for fast, precise movements. An Easylink+ coupling station is able to control up to 60 sources and 60 destinations, and can be configured using all or some of the inlets and outlets, keeping the option of subsequent expansions open. Easylink+ is essential for reliable, complete material traceability. Integration with Winfactory 4.0 allows: ? maximum traceability of materials ? automatic setting of transport and line cleaning times ? raw material stock monitoring with automated reorder function ? remote connection from portable devices Benefits ? No contamination thanks to state-of-the-art pipe cleaning procedure ? High wear resistance ? Simplified maintenance ? Completely traceable materials ? Minimal floor space occupation and maximum accessibility ? Outstanding versatility thanks to a broad range of diameters - 40mm, 50mm, 60mm, 76mm - and the large number of possible inlet/outlet combinations
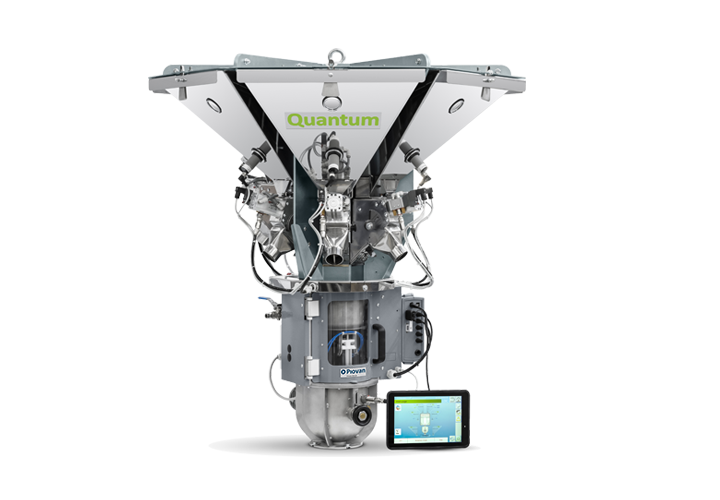
Quantum embodies innovations that radically change the way injection moulding machines and extruders are fed with blends of materials (virgin, recycled, masterbatch and additives). These innovations contribute to increasing the efficiency of production, and feature improved design, innovative technologies and high performance components, which translate into real advantages for the customer. Quantum is utilised in all application environments such as PET Preforms & Bottles, Rigid Packaging, Automotive Components, Technical Parts, Medical Solutions, Thermoforming & Technical Sheets, Flexible Films, Pipes, Profiles, Cables, Fibres & Strapping, Recycling and Compounds. Its flexibility derives from two distinctive and unique characteristics: All the surfaces that come into contact with the process material are stainless steel, usable also in the most critical environments, like those found in medical and food & beverage sectors. Low roughness prevents friction and permits uniform treatment of the polymer pellets, preventing the alteration of physical conditions. Quantum therefore protects the physical characteristics of the raw material, and thereby the quality of the plastic product. Every blender comes with up to 6 dosing stations, which can easily be removed, for emptying or cleaning. Each dosing station is dedicated to a single ingredient - be it principal or additive; easy removal therefore aids material changes and enables optimal operating conditions to be immediately resumed without contamination from powder or residue. These interventions do not require the blender to be dismantled and can be done manually by an individual operator. The dosing stations can be used across all Quantum blenders in a factory. Integration with Winfactory 4.0: The control system is designed for integration with Winfactory 4.0, the industrial supervisory software operating by application licence developed by Piovan, the outcome of consolidated knowledge in various application environments. Winfactory 4.0 can interface all Quantum blenders in the factory for: sharing recipes, managing material and production batches, and tracking raw materials; these are fundamental data for product certification, in particular in food & beverage and medical-pharmaceutical environments. Benefits ? Immune to vibrations ? Expandable configuration ? Portability ? Quick material change ? Simplified cleaning operations ? Perfect homogeneity of the blend ? For all plastic materials ? With remote mixer
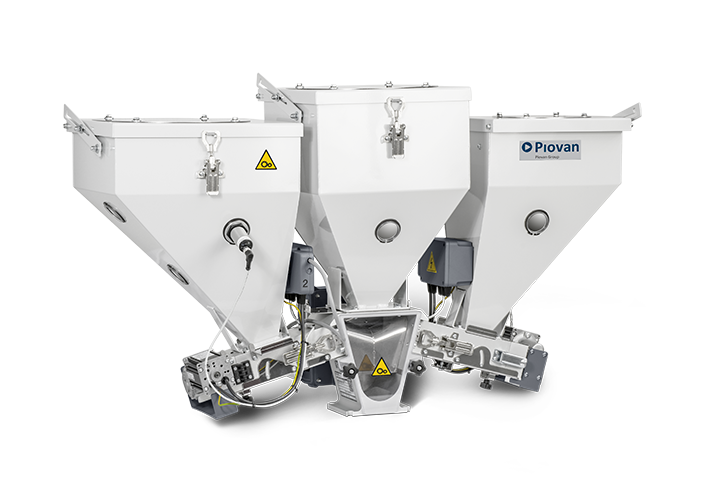
Single or double-station volumetric dosing units, with a throughput ranging from 0.005 up to 150 kg/h. Designed to dose masterbatch, additives and regrind into the plastification screw. CUSTOMER ORIENTED SOLUTIONS: A single unit covers a wide production range: The rich selection of screws and gear boxes allows multiple requirements to be met. Utmost versatility of use: Cleaning and maintenance operations are simple and require just a few minutes. No material wastage: The space-saving design of the central block results into no material wastage at the initial and final phases of the production job. Maximum ease of use: The combination of the construction solutions adopted and the user-friendly software ensures maximum ease of use.
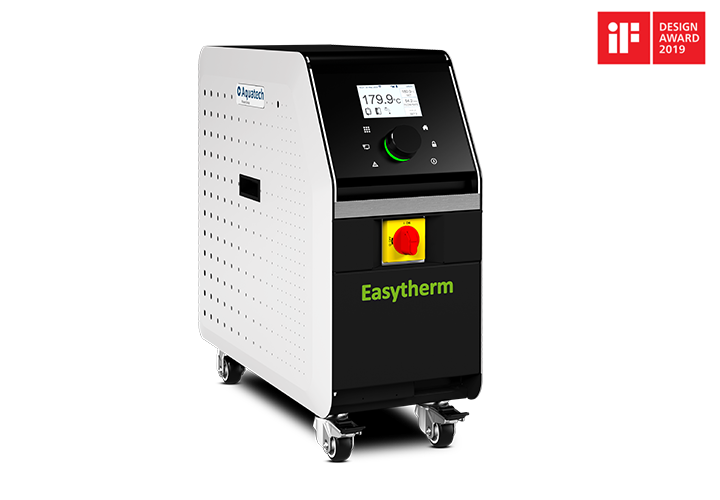
Temperature controller ETP and ETPHT are models of the Easytherm family for high temperature applications up to 180°c., technical moulding and high demanding applications. The new design is extremely compact and includes the FTH modules (Flow Through Heater), so the heating elements are no longer in contact with the process fluid. This avoids any risk of corrosion or any decrease in the heat exchange efficiency due to limestone deposits. The Easytherm pressurized version is available in two configurations according to the maximum running temperature: ETP up to 140°C and ETP-HT up to 180°c. Easytherm is manufactured using the best in class components to assure high performances throughout the life of the machine. Easytherm is ready to communicate through a wide range of different protocols for maximum flexibility, including OPC-UA according to Euromap 82.1 standard. Easytherm is also ready to be integrated into Winfactory4.0. Easytherm can be configured according to customer needs including the following options: flow meter for process water, pressure transmitter, temperature probes or thermocouple in the mould, automatic mould exhaust or additional filters on water connections. Easytherm is easy to use thanks to its rotating control, linked to the base LED system screen, which immediately displays the status of the machine. It is easy to manouvre thanks to the integrated handlebar and new robust wheels. Benefits ? Highly reliable and long life FTH module, without contact between fluid and heater ? Working temperature up to 140°C or 180°C ? High performance pumps and high cooling capacity ? Easier handling thanks to the new integrated handle bar and robust wheels ? Ready to communicate with multiple protocol included OPC-UA ? New layout for compact unit
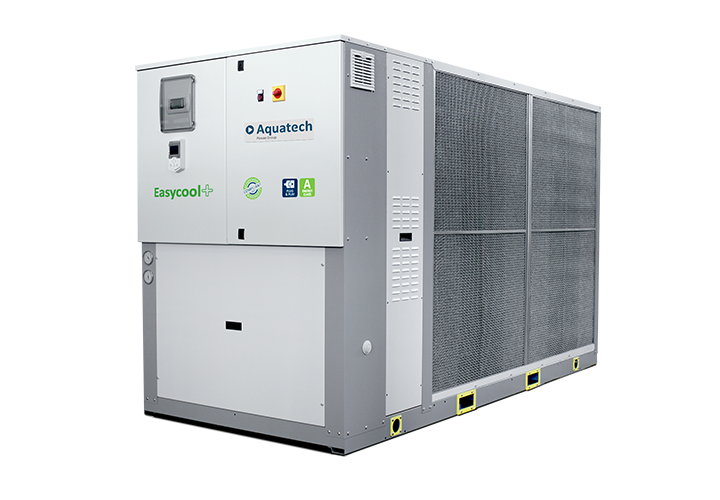
In order to ensure the effectiveness of the process, in most cases traditional industrial chillers consume a great deal of energy with consequential increases in production costs. Easycool+ by Aquatech overcomes this problem, because it is a chiller conceived, designed and built for cooling in specific industrial processes for plastics. Flexibility, energy efficiency, reduced footprint and low environmental impact: Easycool+ adds value and reduces the costs associated with the investment. The optimum temperature ensures the best product quality. When processing plastics, the temperature ranges to be maintained for different processes can vary significantly, requiring that the chiller provides different conditions of pressure and flow rate: the flexibility of Easycool+ ensures the best operating conditions are maintained at all times. Developed specifically for industrial plastic production processes, Easycool+ by Aquatech offers a number of benefits in a wide range of areas. Benefits ? PLUG&PLAY technology with integral circuitry in the machine ? a system made with Easycool+ is dimensioned so as to ensure the least possible coolant load ? robustness, quality components and comprehensive configuration ? energy efficiency, available in both Class B and Class A ? compact design ? power range from 10 to 500 kW, for maximum flexibility of use
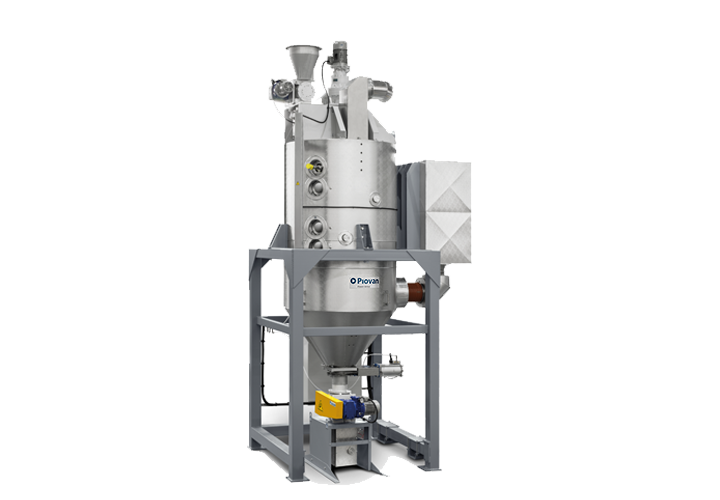
For those production processes which use amorphous PET both of virgin granules and of regrind from bottles, containers, fibres, thermoforming sheets and strapping, Piovan provides a complete range of crystallisers, to carry out the material preparation process before the injection moulding phase or extrusion. The models ranging from the CR 150 to the CR 4000 have been specifically developed to overcome the material glass transition temperature and to guarantee homogeneous crystallization, with no risk of sticking or formation of bridges. Once crystallized, the in-house regrind or the PCR are dosed and mixed with virgin granules by means of batch gravimetric blenders before the drying process. Good crystallisation allows optimisation and simplification of the drying phase, with no risk of material degradation and the possibility of recovering high percentages of regrind. Benefits ? Energy efficiency ? Self-adjustment of the system ? Optimal and continuous mixing of the material ? Feeding devices ? No risk of contamination ? Rapidity in production shift
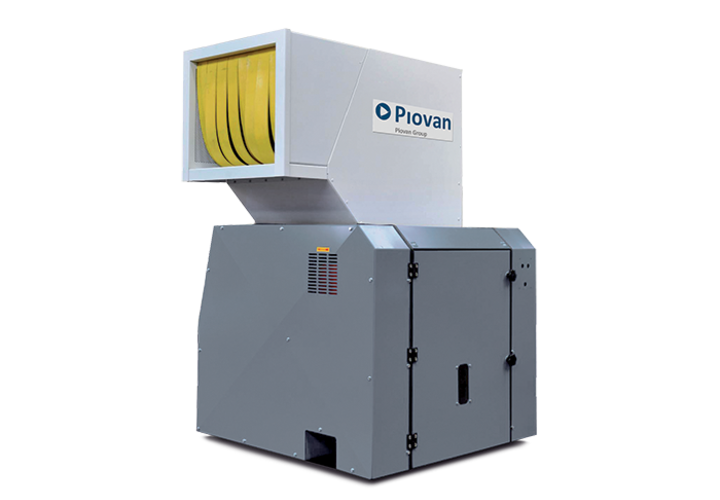
Models: N25-45 N35-60 N55-90 Cutting Chamber: ø 250 mm; ø 356 mm; ø 560 mm Technical data: Suitable for injection & blow moulding, extrusion and general purpose applications Hopper with inspection door for easier cleaning and maintenance Cutting chamber with discs and plates wear resistant Advanced scissors cutting action with adjustable rotor blades, reduces energy consumption, heat and dust generation A range of feed and discharge options are available to meet each customer requirements
No represented companies found.
The company has no registered brand information.