Company Name | Contact Info | Location | ||||||||||||
---|---|---|---|---|---|---|---|---|---|---|---|---|---|---|
SLEEVE MAK. MAKİNA SAN. VE TİC. LTD. ŞTİ.
Ikitelli OSB Mah. Pik Dökümcüler San. Sitesi Sok. No: 27 TEM 34 İkitelli B2 Kat No: 51/52 / Başakşehir / İSTANBUL / TÜRKİYE
|
Contact Info: +90 212 549 5581
|
Hall: 11A
Stand: 11A-112B
|
||||||||||||
Product Groups | ||||||||||||||
|
- Company Info
- Products
- Represented Companies
- Company Brands
Since 2002 Sleeve Mak Makina Ltd., produces Body Sleeve Machines, Steam Tunnels, Electric Tunnels, Temper Evident Application Machine, Conveyor and Automation Systems, Dryer Tunnels. In 2015, the company took the name of Sleeve Mak Makina Ltd. and continues its activities in a professional manner with its highly experienced team. Sleeve Mak Makina San. Tic. Ltd. Sti. has followed closely the development of its sector since its establishment, innovation and entrepreneurship. It has become a favorite in this sector with its technical infrastructure, knowledge and experience and its ability to provide quality. Our company following closely the requirements of the information age has adopted a human-oriented philosophy. While our customers needs are meeted, a smiling face, professional experience and business ethics are taken into account. We consider the idea of rapid and high quality service as our indispensable principles by closely following the sectoral needs of our institutional and individual customers who we serve. While meeting our customers needs, we fully use our technic information and professional experience. We think that creating a good future will be much easier by sharing our information with others. Since Sleevemak was established it has improved its production in parallel of the sector. Moreover, it enhances itself in parallel with the developments in the sector. With a dynamic and continuing excitement, Sleevemak keeps its institutional activities on a regional and national bases without delay. Our company which thinks that providing quality will be possible only with technic information and experience will continue to be the favorite company of the region and will always keep its respectability and general improving outlook among national companies.
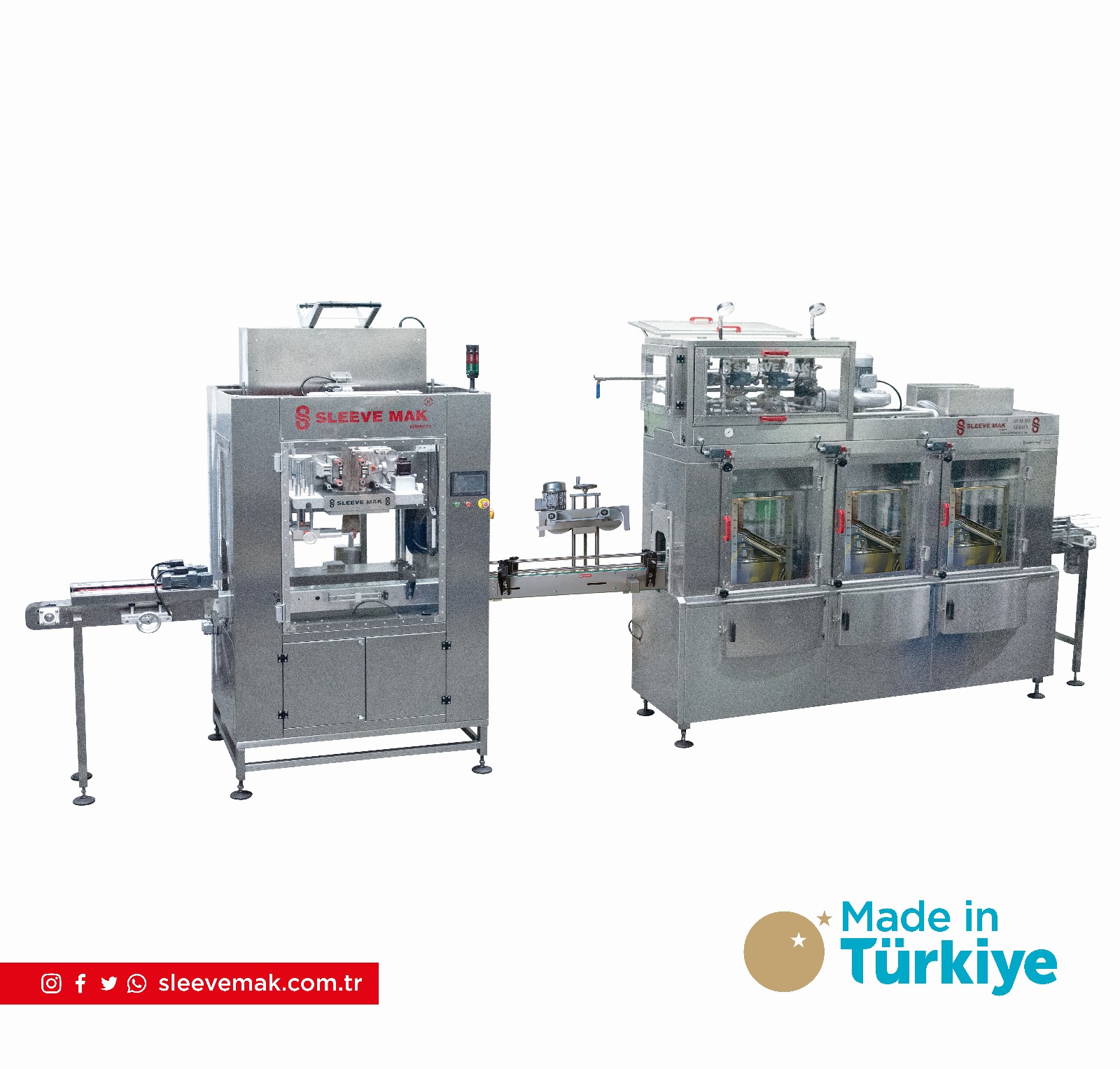
Our Main construction of the machine made from Stainless Steel AISI304, other parts made from hard anodizing aluminum that has high wearing resistance. Sleeve label applied on products automatically through linear line system. The machine can apply sleeve label on glass , plastic, PET, PE and metal products. The machine can apply both PET and PVC sleeve labels. The machine can work on sleeve labels with thickness from 35 to 80 µm Except for mechanical adjustments, all the machine can be controlled automatically through PLC system (OMRON). The machine can be controlled through LCD touchscreen monitor (OMRON). With range 40mm to 300 mm the length of the products can be adjust by moving the main block upwards and downwards automatically. The rotary cutting system working with Servo motor using cutting blades. The rotary cutting system can be easily assemblied and disassemblied also the speed of the blades can be controlled through the screen. Our machine can work on Product´s diameters with range from Ø40 mm to Ø150 mm with suitable equipments ( guide and blades´ box ) you can change easily between the products by changing the related equipments. The servo motors (OMRON R88 model with moiton control specification) used to drive the sleeve label pulling system , the shooting system and the rotary cutting system with total number 4 pcs. of servo motors. With sleeve label´s stretching system the label can be cutted accurately. The roll of the sleeve label can be changed fastly. The parameters and setting for different types of products can be saved on the memory of the PLC system. At the entrance of the machine when there is no product the machine automatically enter the standby mode. The chain of the conveyors made from INOX (model 82.50 mm) Adjustable side barriers to control the motion of the products. The emergency stop button can be found on the machine main panel in a reachable place. Saftey switch sensors to stop the machines if the doors opened. All the sensors are ZICK brand The machine contains 2 reducer motors CE certificated Total power: 3 Kw
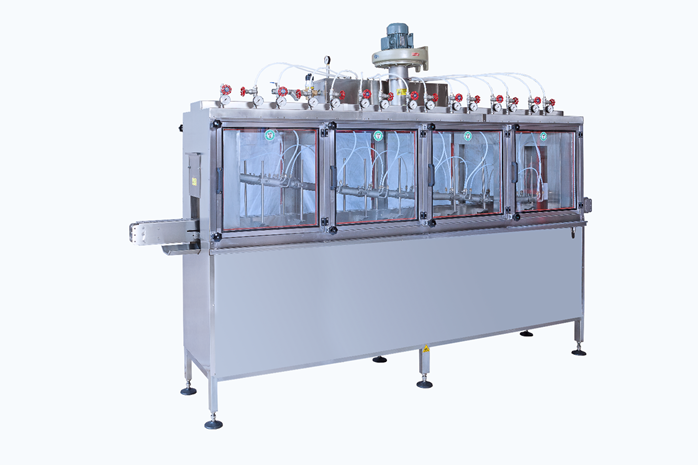
Our Main construction of the machine made from Stainless Steel AISI304. Sleeve label shrinking processed through linear system. The machine can shrink sleeve label on glass, plastic, PET, PE and metal products. The maximum product´s height is 300 mm. The maximum product´s diameter is Ø150 mm. The speed of the conveyor inside the tunnel controlled by frequency driver. The tunnel can be synchronized with the sleeve label applicator machine The steam nozzle body is made from aluminum contains steam paths inside inorder to heat the nozzle which prevent droplets at the tips of the nozzle. The nozzle´s position can be adjusted all round (360°) For evey nozzle there is a flow control valve with pressure guage to make Fine and sensitive adjustments for the flow of the steam outside the nozzle. At the steam entrance an adjustable pressure regulator (MIYAWAKI) to insure a constant pressure at all nozzles. The Windows of the tunnels are made of a heat resistanced glass with 25 mm thickness The steam tank is double walled to insure that there is no heat transfer. The chain of the conveyors made from INOX (model 82.50 mm). Adjustable side barriers to control the motion of the products. The emergency stop button can be found on the machine main panel in a reachable place. Total power: 1.2 Kw
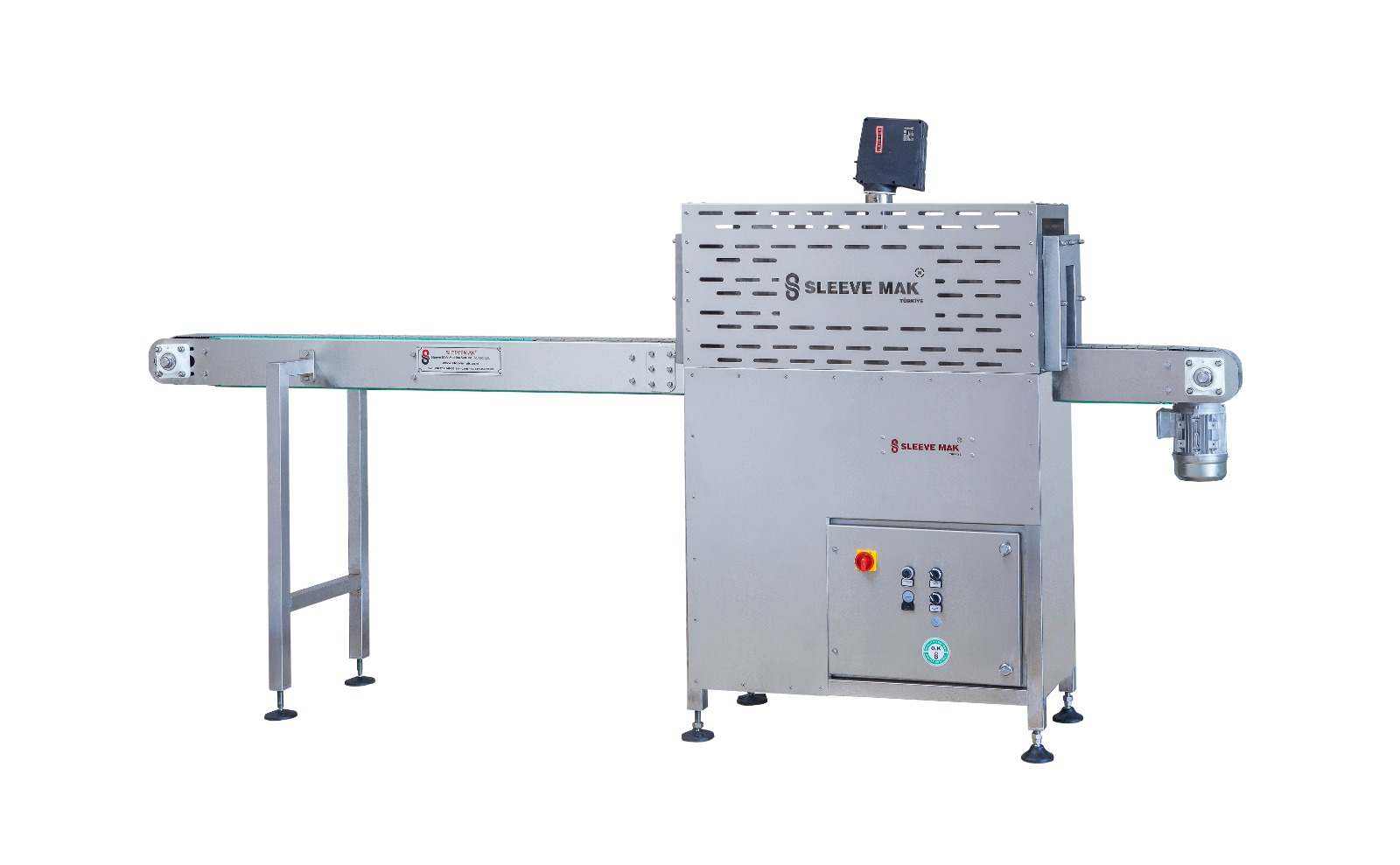
Our Main construction of the machine made from Stainless Steel AISI304. Sleeve label shrinking processed through linear system. The machine can shrink sleeve label on glass, plastic, PET, PE and metal products. Leister type: HOTWIND PREMIUM 5400 W. Air temperature up to 250ºC. The tunnel´s Temperature can be adjustable and measured by thermostate The design of the tunnel allow perfect air circulation Conveyor and fan controlled by Frequency Inverter The tunnel is isolated (Double walled) CE certificated
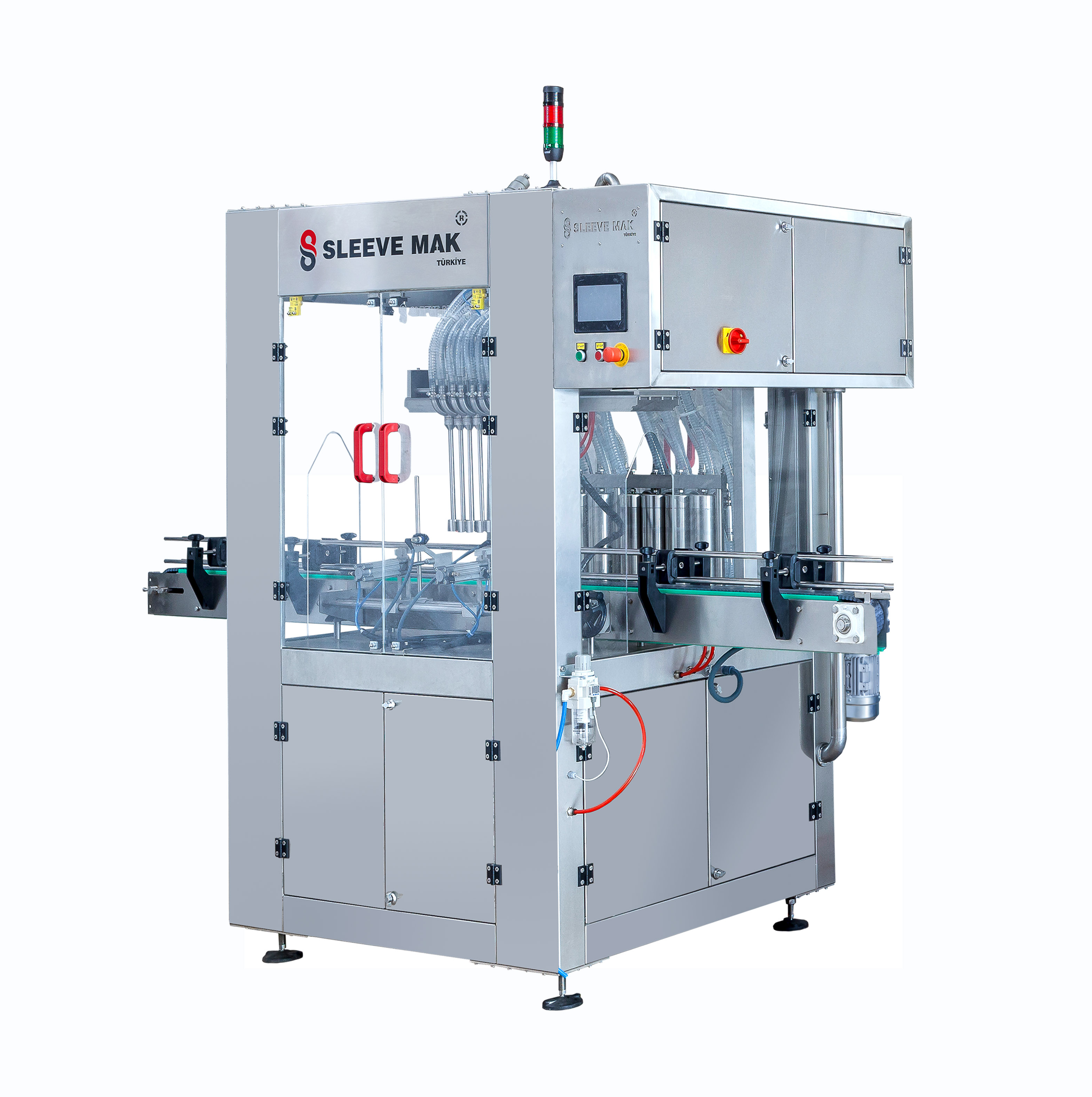
Our Main construction of the machine made from Stainless Steel AISI304. The machine used to fill light and low viscoisty liquids . Automatically filling process through linear line system. Nozzles can be moved up and down automatically according to the length of the products to be filled. Filling range: 3000 cm3- 5000 cm3. Filling nozzle number: 4 nozzles. Capacity: 1000 Pcs/hr. Filling Pistons are made from stainless steel AISI 304. Filling system: Dip and top. Without any mechnical interaction from the machine screen the requested volume can be adjusted easily with our PLC (OMRON) system . You can save all your recipes in the PLC system without losing any data and you can recall 100 % of the recipe at any time faster and cleaner more than ever. LCD Touchscreen (OMRON). Pneumatic system and connectors SMC. Filling and suction process´s speed can be adjusted from the screen. Air pressure: 6 bar Contains 3 m conveyor with 0.37 Kw motor. During filling process error rate not more than 0.003 L Machine dimensions: 110 x 170 x 225 cm Total Power: 4 Kw
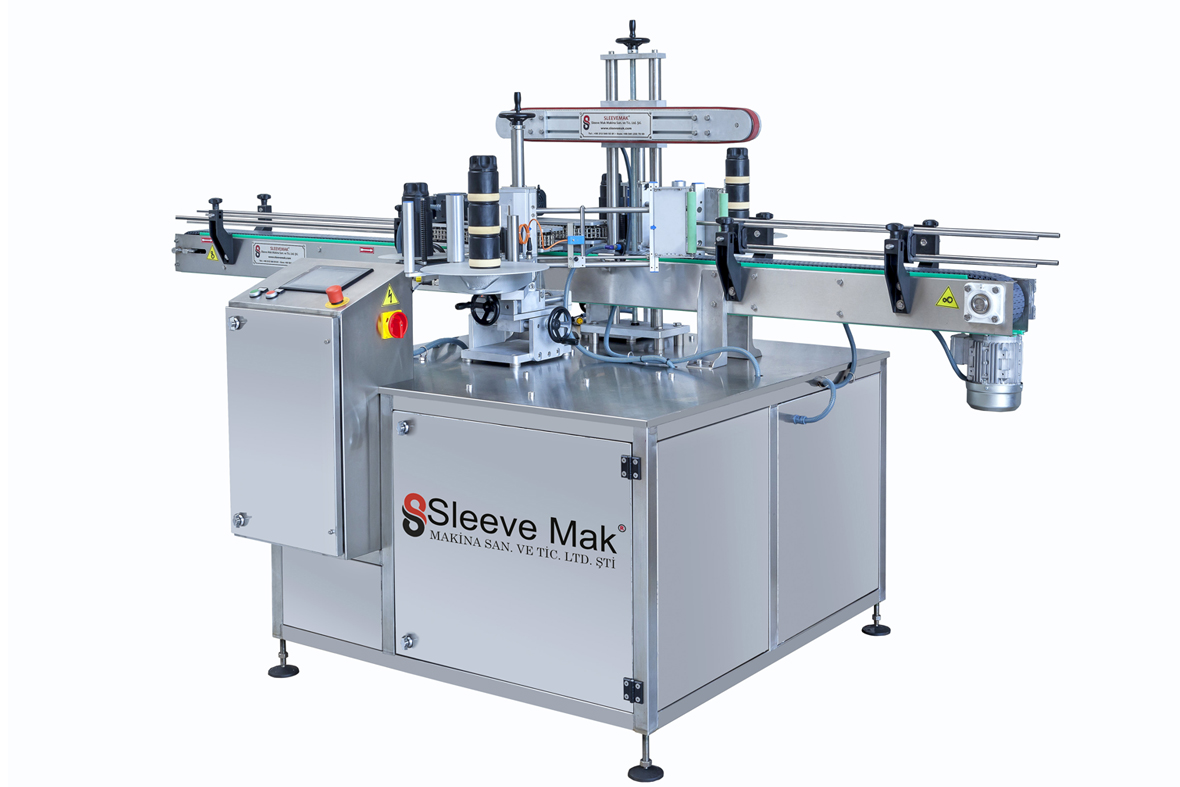
Our Main construction of the machine made from Stainless Steel AISI304, other parts made from aluminum. Labelling process through linear line system. The machine can be synchronized with the automatic filling machine. the machine can work on cylinder, oval, square and rectangular shaped productss. Labelling Module (German) two Module Reducer motors (Varvel-Italy) PLC system and frequency drivers (OMRON Japan).
No represented companies found.
- SLEEVE MAK MAKİNA SAN. VE TİC.LTD.ŞTİ.