Company Name | Contact Info | Location | ||||||||||||
---|---|---|---|---|---|---|---|---|---|---|---|---|---|---|
VİKOTECH MAKİNE SANAYİ TİCARET LİMİTED ŞİRKETİ
İkitelli OSB Eski Turgut Özal Cad. Haseyad 1. Kısım No: 23 C/C / Başakşehir / İSTANBUL / TÜRKİYE
|
Contact Info: +90 212 549 1972
|
Hall: 11
Stand: 1118
|
||||||||||||
Product Groups | ||||||||||||||
|
- Company Info
- Products
- Represented Companies
- Company Brands
A 10 YEARS Youth company with a great ambitions and wide achievement of gaining the trust of customers, specialized in manufacturing Plastic Recycling Machines and equipped with the latest technology along with the top experienced staff. All the machines that we manufacture will turn waste plastics into reusable High-Quality Virgin-Row Material. As VikoTech Machinery our missions are We always consider innovation and performance, when we make Research and Development R&D Being a brand-name at the world with manufacturing a high-quality Recycling Machines. Provide an easy and quick solution for the customers when they need it. Provide an excellent work environment for our employees. To increase the productivity by reducing cost of production process to accelerate the profit circle for our customers.
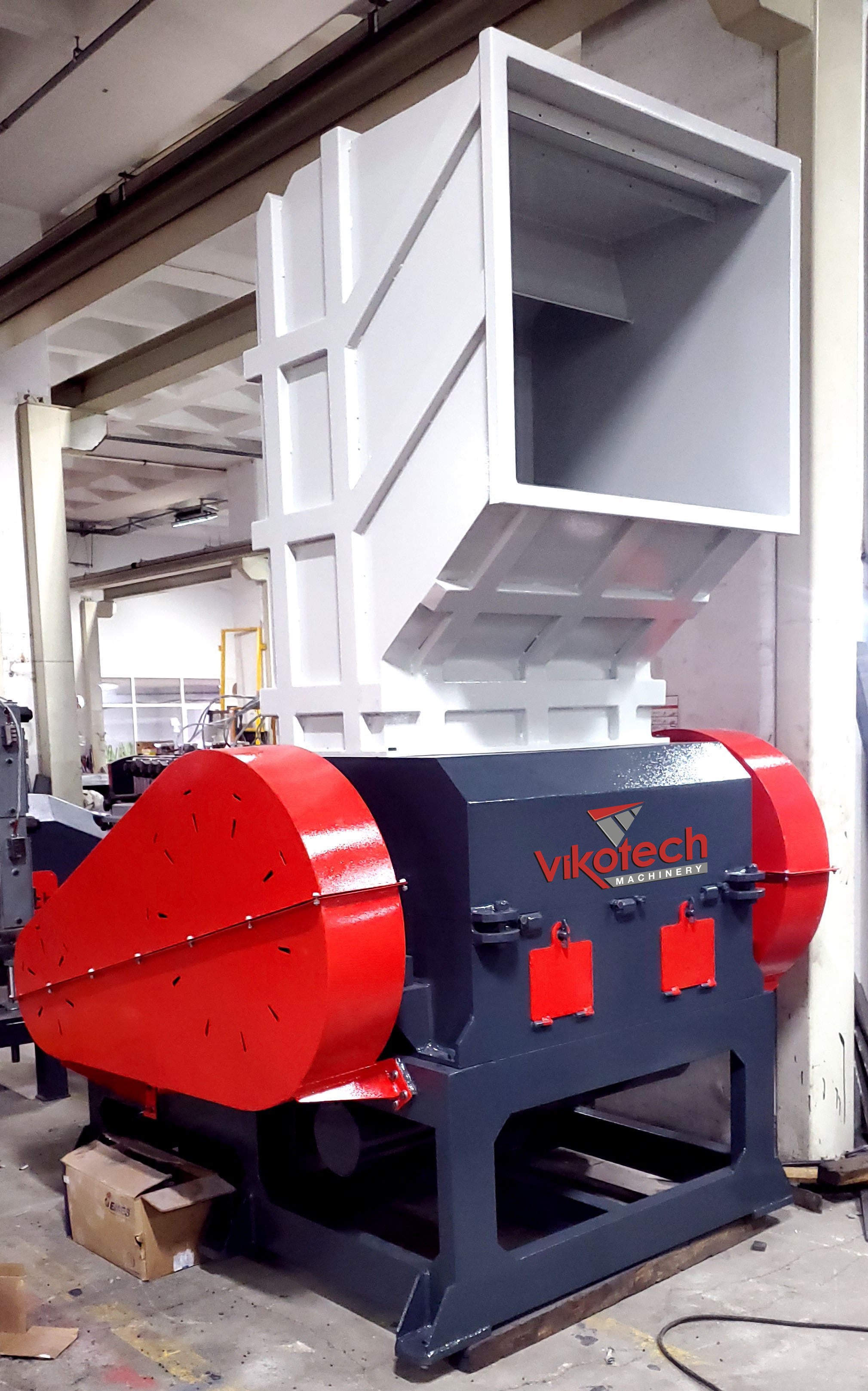
Plastic Granulator machine Crushers one of the key machines used in Plastic Recycling line. Compact body design, special bearings and Powerful Rotor design extends the life of the machine. Granulator machines are manufactured with production capacity starts from 100 kg/h up to 3000 kg/hr.
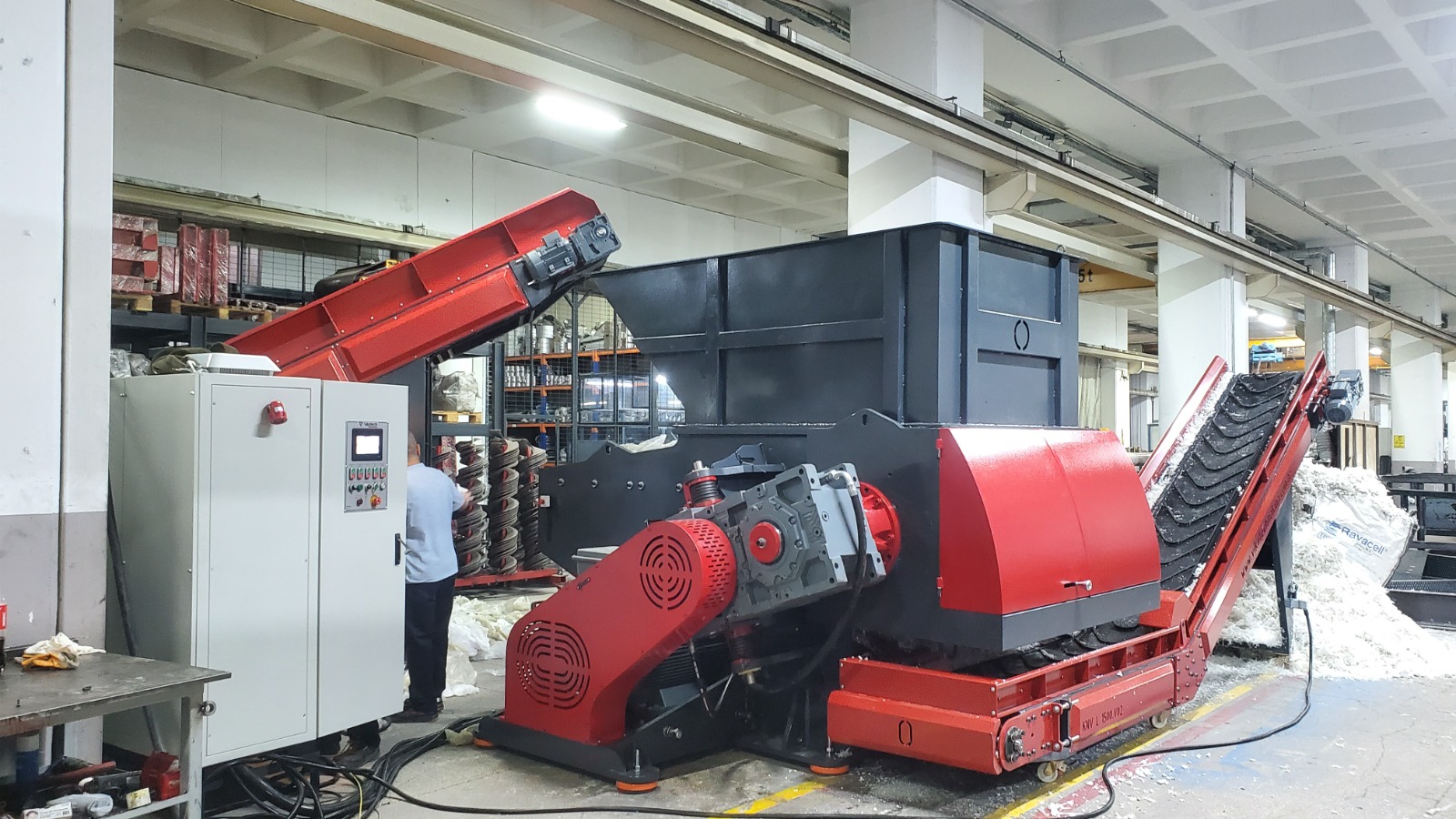
Single Rotor Shredders are used for size reduction of all types and forms of plastic scrap, cardboard, tex- tile, carpet, paper waste without getting affected by thickness and density of material. Rotor, blade, feeder and screen model is chosen according to the type and form of scrap to quarantee high capacity. Straight, inclined or swing type feeders are used for different forms of scrap and feeders can be powered by hydraulic or pneumatic power. Feeders are controlled by PLC system.
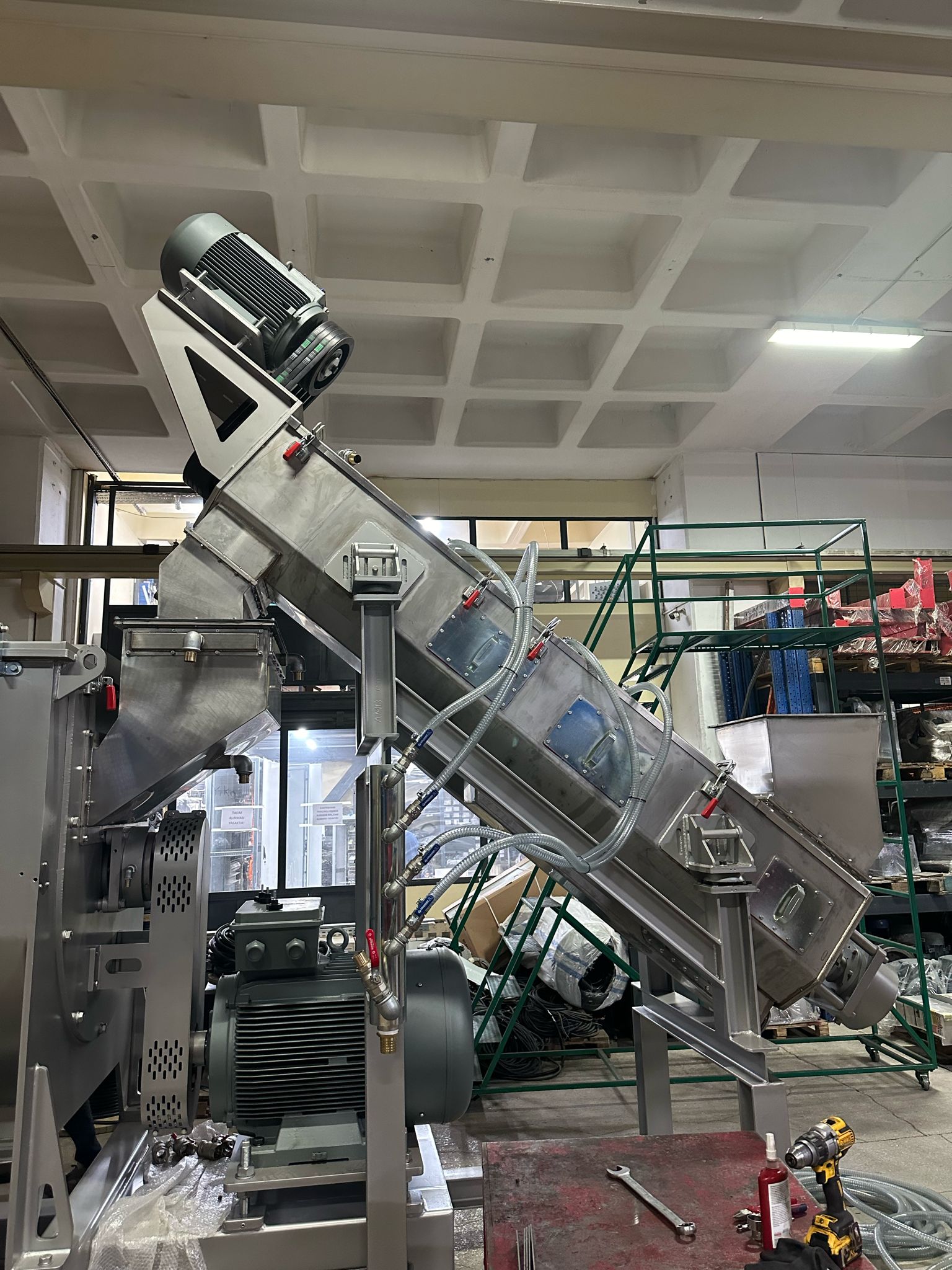
Horizontal Centrifuges VK-SNT are used for washing plastics under high speed and they clean plastics intensively by friction. Our improved rotor and rotor wings design creates more friction which increases centrifuge efficiency. VK-SNT are made of AISI 304 stainless steel material, and sizes between diameter Ø250-Ø500mm, and length 3000mm-5000mm according to required production capacity.
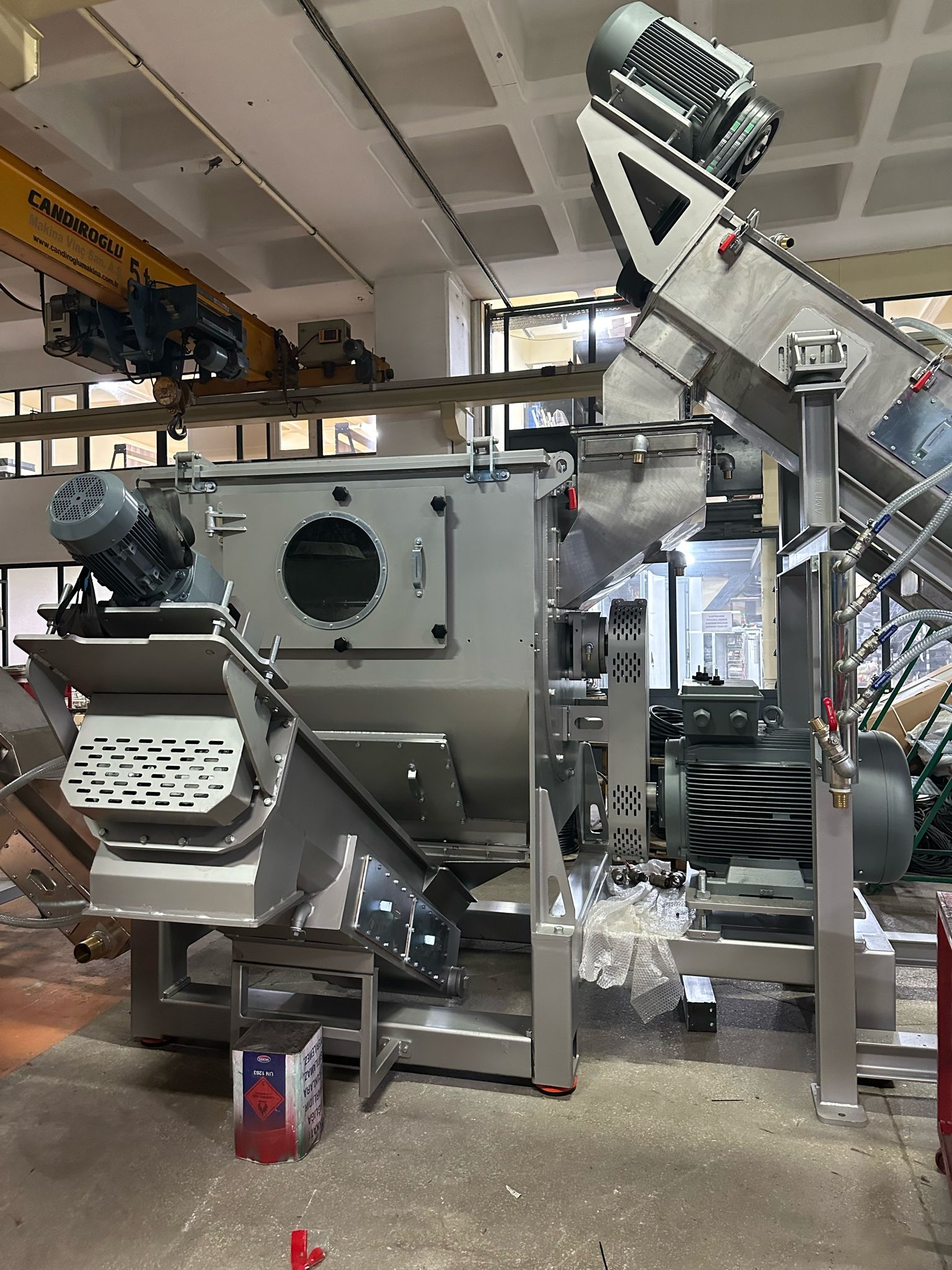
It s a multifunctional machine that can wash-clean, dry and separates crushed plastics materials such as PE, PP, PET, and LDPE While rotor on centrifuge turns at 1500 rpm the perforated trommel around it turns opposite direction for maximum intensive cleaning. Rotor at high speed with centrifugal principle collects all heavy plastics at bottom of machine and same time all the water and none plastics thrown out from perforated trommel holes. Drying is done mechanically without Reduces moist level less than %1 Trommel holes diameter changeable it depends on process to be Depends on process rotor and trommel speed ranges from 1000-1500 Easy access to trommel cleaning and According to customers request and needs drying and washing capacity range 500kg/hr to 3500 kg/hr
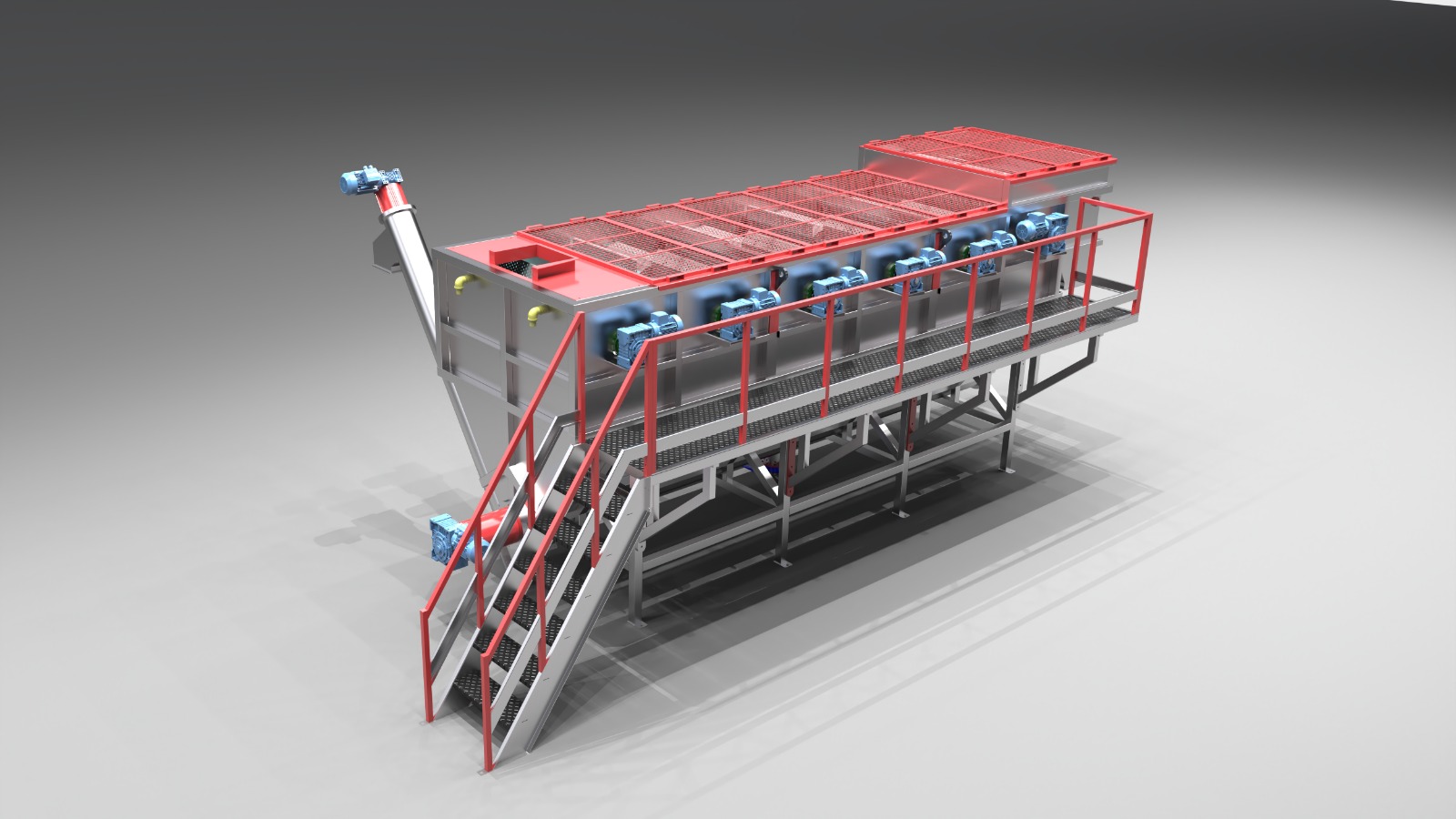
They are used for separating the floating plastics from contaminants like heavy plastics, mud and metals, Contaminants can be easily discharged by the under-tank discharge valve. Sink & float tanks are designed with maximum cleaning, minimum material loss method. Sink & float tanks can be made of AISI 304 stainless steel or DKP sheet, and length 3000mm-6000mm according to customer s demand.
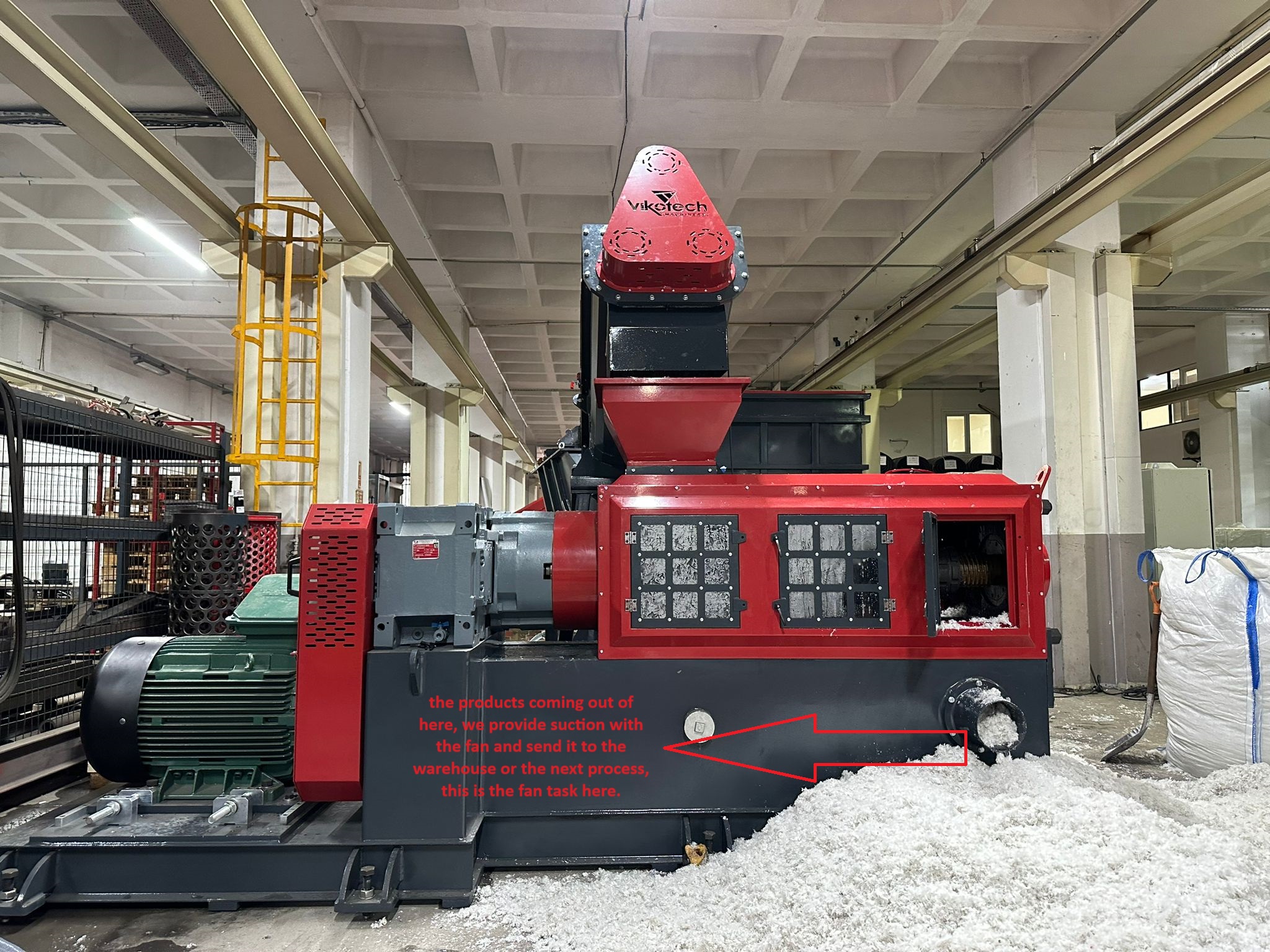
Plastic Film Dewatering Machine is one of the most important machines in Plastic Recycling line. All the crashed and washed contaminated Plastic FILM materials, dewatered by this machine. Material dewatered mechanically and it will not require an operator. Special designed heavy-duty screw and barrel will reduce the humidity level down to 4 8 %, and this will reduce the electricity consumption for next drying phase.
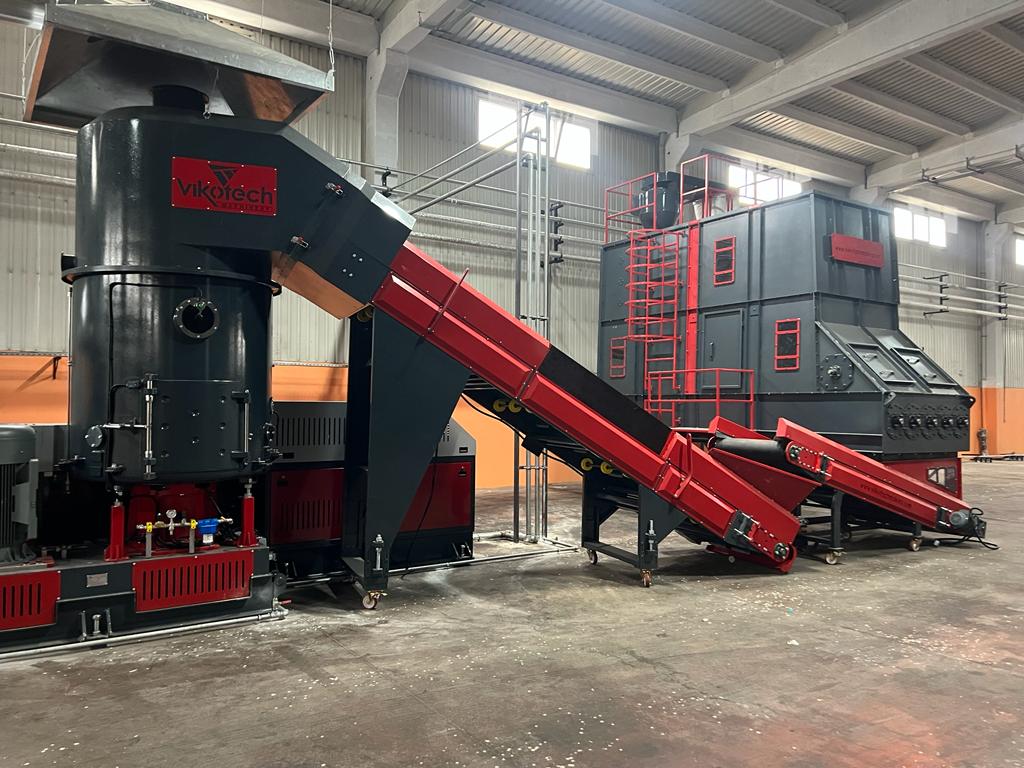
Our VK-CP extruder was made with the latest technology in recycling systems. It is the easiest to operate, offers the highest benefits and the lowest operating cost ratio among plastic granule extrusion systems. VK-CP The extruders require minimum manpower thanks to its automatic operating system. VK- CP extruders process plastic in all forms burr, bran, foam of: LDPE, LLDPE, HDPE, PP, PS, ABS material types. Even plastics with high moisture content up to 7% can be pelletized without problems. The high technical equipment of the VK-CP extruder allows: Final drying, condensation, homogenization & degassing Processes in one step. The VK- CP extruder operates with minimal manpower requirements thanks to its user-friendly PLC control system. With the recipe function, all parameters of the system are recorded. When processing plastics with different properties, different recipes are recorded and all parameters are automatically loaded into the system with just one click.
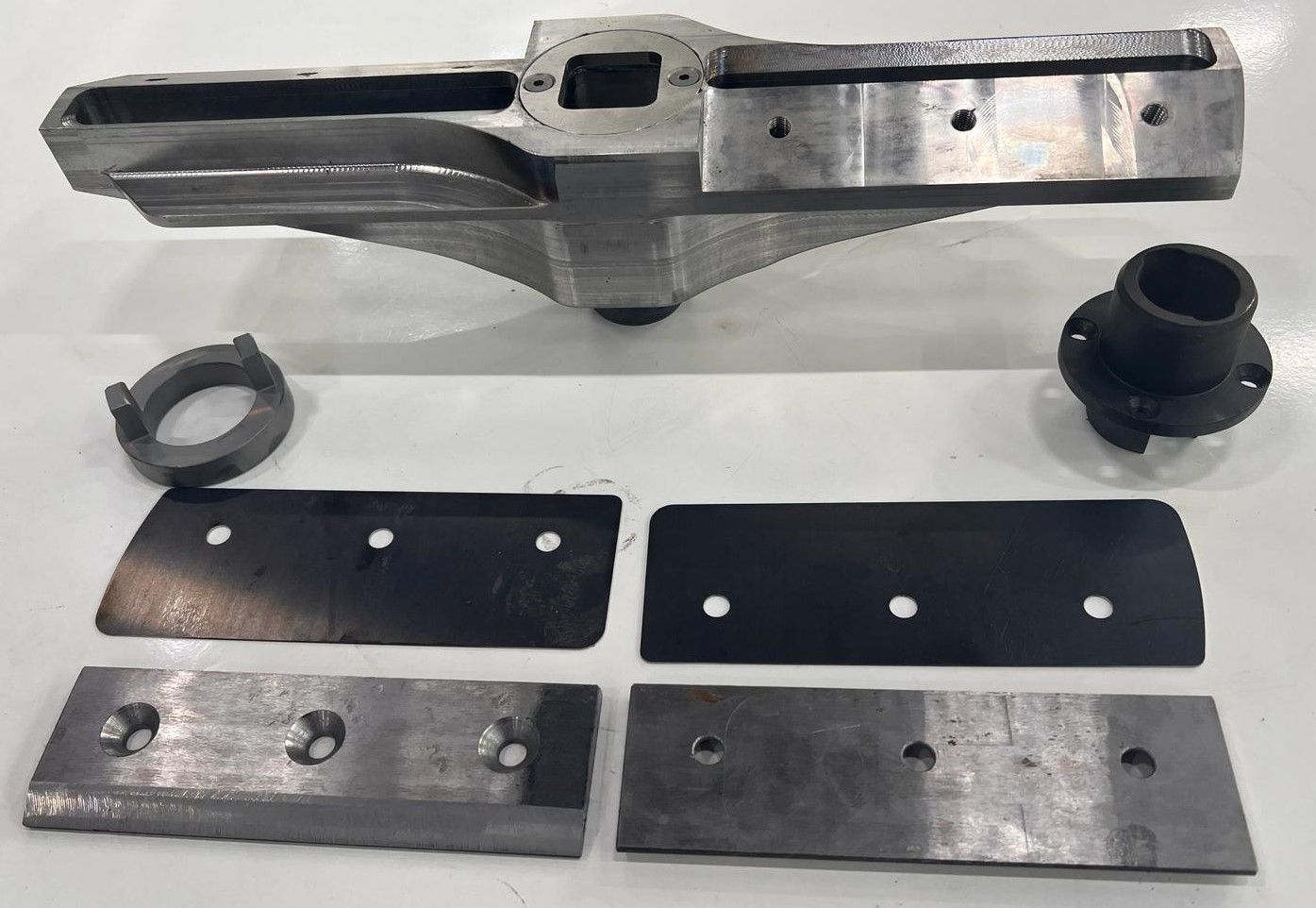
Screen change : - Sieve change every 4 to 15 days, depending on usage and material contamination - Through the blade system on the self-cleaning sieve, the impurities on the sieve surface are cleaned and thrown out automatically depending on the amperage - Automatic and continuous sieve cleaning Continuous sieve surface cleaning option thanks to the determined amperage scale Filter : - The VASC is a melt filter capable of managing any level of contamination and guaranteeing a reduced amount of waste and low maintenance costs. - The VASC can be adapted to your specific requirements such as the type of plastic material to be filtered, the hourly production rate, the filtration level and the type of contamination.
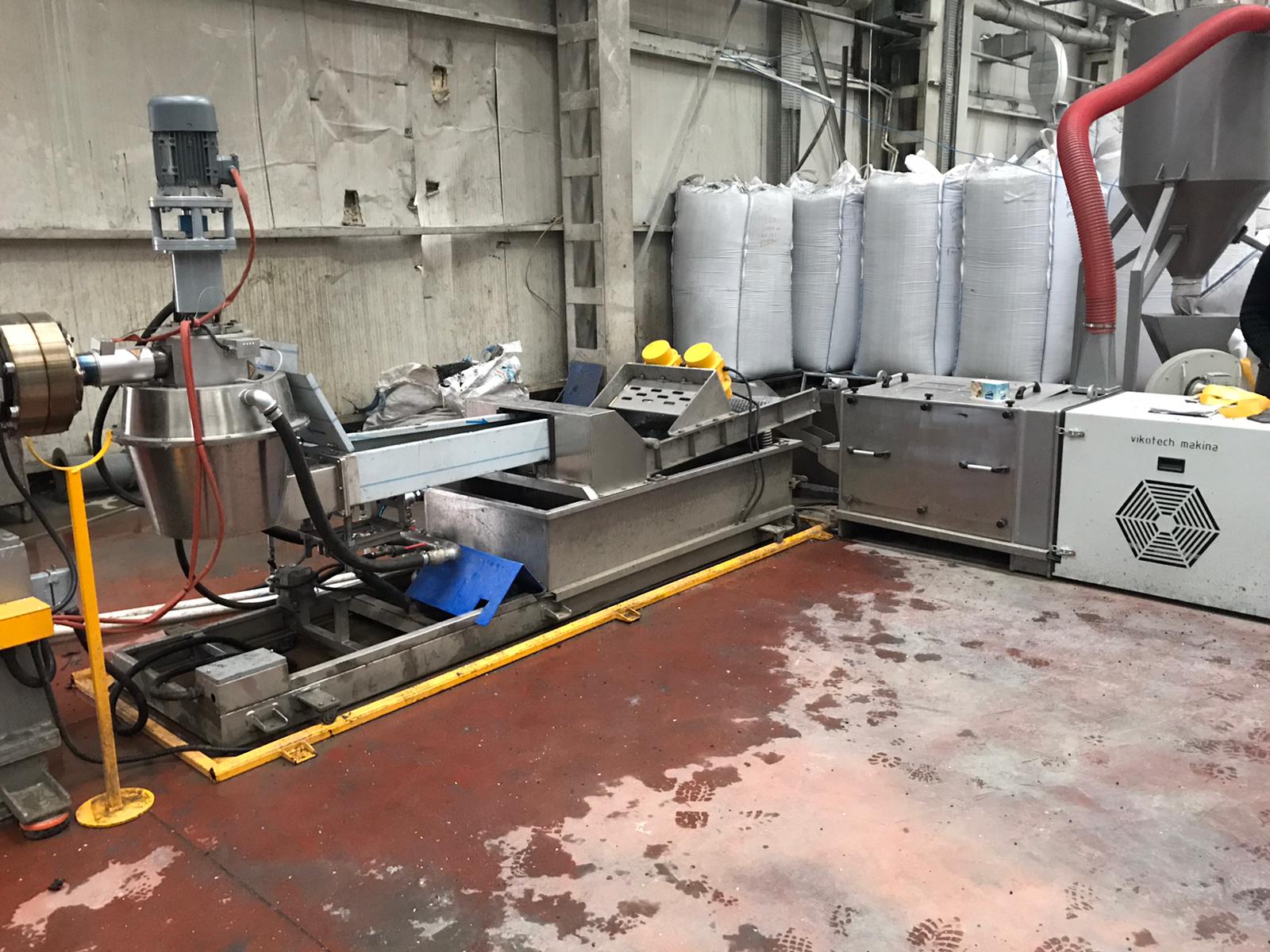
The pelletizing machine is used to cut the plastic melt that comes out of the extruder and turns it into a small pellet shape. This pelletizer can be used for PP, PE, HDPE, LDPE, ABS, PS and PU materials. The granule size can be adjusted according to customer s requirement. The cutting process is done by horizontal, water-cooled and easily adjustable spring-loaded blade system. Cutting blades are made of 1.2379 steel. Pelletizer are completely made of AISI-304 stainless steel. Easy changeable mirror and the Steel blades. Perfect vertical air system for drying with-in transfer to final storage-silo.
All the screw and barrel will be designed according to material that will be recycled, screw length/diameter ratio, venting zones amount will be designated according to production capacity and the type material. Extruder screw diameter manufactured between Ø15-Ø220mm depends on capacity. Screw & Barrel will be designed depends on which plastics are being used such as: LDPE, HDPE, LLDPE, PP, OPP, BOPP, CPP, PS, EPS, ABS. Screw Barrel made of DIN-8550, DIN-4340 and DIN-4140 material. Special hard welding is applied on screw to lengthen the life-time of screw also heat treatment and special hardening will be applied on screw and barrel.
No represented companies found.
The company has no registered brand information.